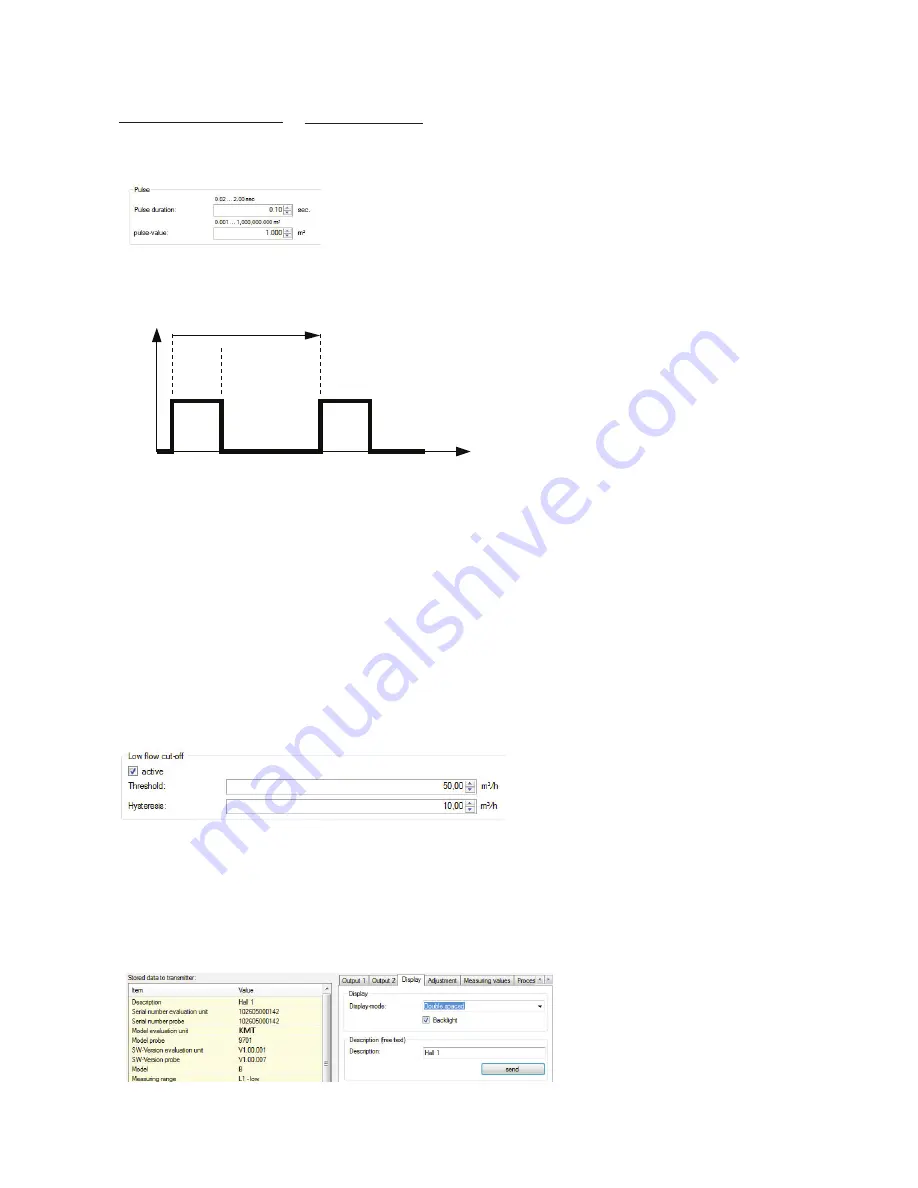
31
5.1.6. Output mode – pulse
If output 2 is configured for pulse, the measurand can be consumption only. Under “Pulse”, the duration of the
pulse and the pulse value (Significance level of pulse) can be freely configured.
Volume Flow [m
3
/h]
Number of Pulses
Hour
Pulse Value [m
3
/Pulse]
=
The duration of the pulse can be set between 0.02 and 2 seconds.
e.g. Duration of pulse = 100ms; one pulse for each Nm
3
consumed
The pulse – interval – ratio must be at least 1 : 2, meaning that the duration of the pulse interval must be at
least twice the duration of the pulse itself.
t
OUT 2
1/3
min. 2/3
≥ 2 s
Calculation of the minimum “pulse value” or the maximum “pulse duration”.
IMPW_MIN = NORMV_MAX [m
3
/h] * IMPL [s] / 1200
IMPL_MAX = IMPW [m
3
] * 1200 / NORMV_MAX [m
3
/h]
IMPW
pulse value [m
3
]
IMPL
pulse length (duration) [s]
IMPW_MIN
minimum pulse value [m
3
]
IMPL_MAX
maximum pulse length (duration)
NORMV_MAX
expected maximum volume flow (NM3/h)
5.2. Minimum flow shutdown
The minimum flow shutdown is switched on and off using the “active” checkbox.
If the output signal is ≤ than the set “Shutdown value”, the flowmeter issues 0 on the analogue output.
5.3. Display
If an optional display is installed, at the tab Display the following items can be entered:
Drop-down input field “Display-Mode”
•
Single spaced
•
Double spaced (default)
Checkbox “Backlight”
•
Checked = ON
•
Unchecked = OFF
In the input field “Description (free
text), a user specific name (max. 16
characters) for the transmitter can be
entered.
e.g.: HALL 1
With the button “send” only the description will be uploaded to the transmitter.
Summary of Contents for KMT-1
Page 36: ...www kobold com...