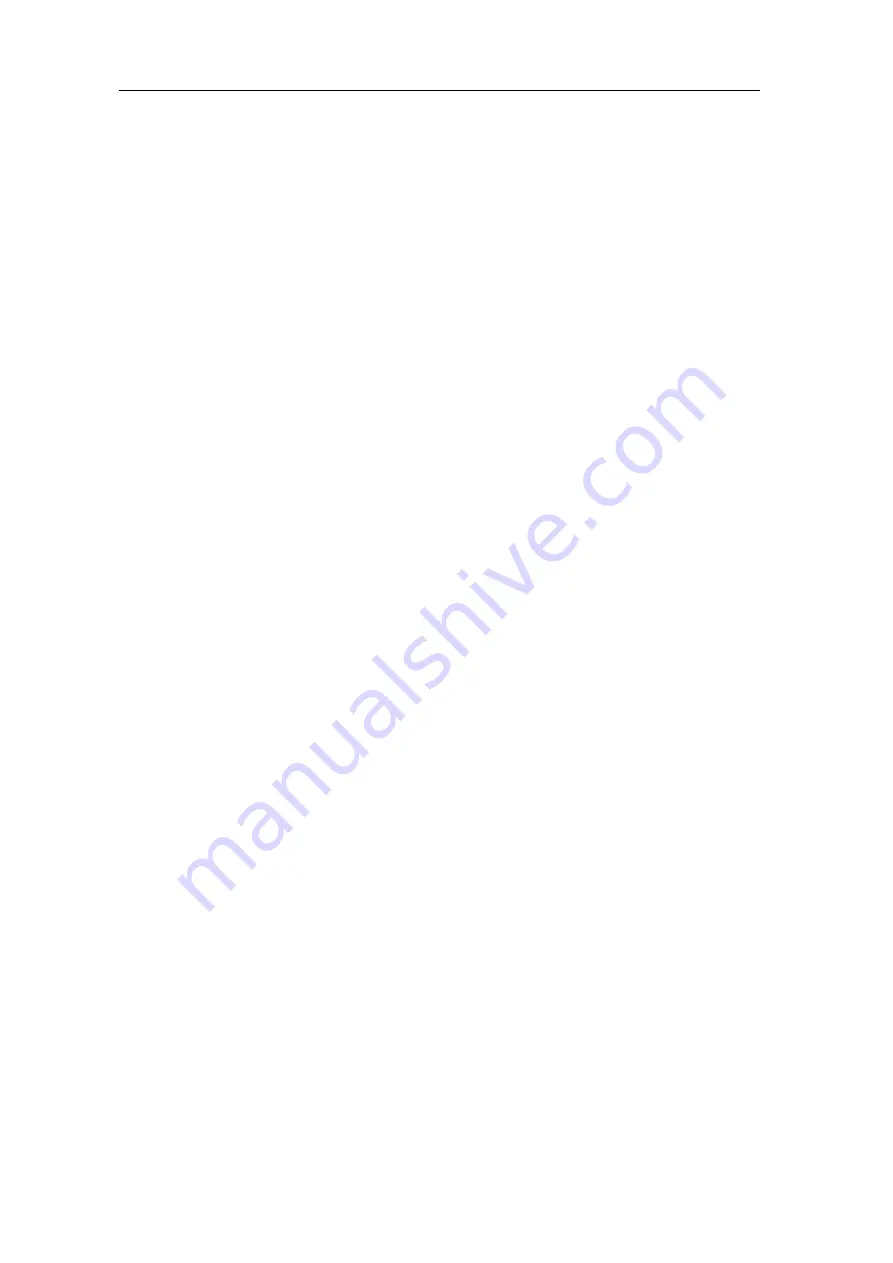
304G2
SERIES TRACTOR OPERATION MANUAL
59
⑥
front axle arms
⑦
left and right front wheel housings
Checking point
①
Engine dipstick
②
Rear axle housing dipstick,
Dipstick on left half shaft housing of front wheel drive axle
③
④
Checking plug on the cover of air pump
Oil outlet,
①
Bottom of engine sump,
②
bottom of rear axle,
④
bottom of air pump
;
⑤
bottom of front drive center housing, and
bootom of left and right retarder housing.
5.2 Periodic Service
According to accumulated working hours, technical maintenance of
G2
series tractor
should be operated every 10h, 50h, 200h, 400h, 800h or 1600h.
Details of the engine’s maintenance can be refered in the manual of engine.
5.2.1
10h
maintenance
1
、
Engine
①
Check the liquid level of engine sump
,
refill them if they are insufficient
,
and
make sure the level will be between the middle notch and the topper notch on
the dipstick. Never exceed the topper notch. A new tractor or one haven’t used
for a long time, the level must be checked again after filling and operating for
5 to 10 minutes.
②
Fill in enough diesel oil and cooling water.
2
、
Chassis
①
Check and fasten every external linkage bolts and nuts.
②
Use a press rod oil gun at these places: left and right retarder housing.
③
Check and eleminate if there is a leakage of oil, water or air. Clean off the dirt
and mud on the tractor.
④
Check the air pressure of front and rear tires, and inflate if they are insufficient.
3
、
Air Conditioning Systems
①
Check cleaning condenser, and insure the radiating fins clean and expedite.
②
Check the drive belt of compressor and engine, and insure it’s not loose.
Summary of Contents for 304G2
Page 1: ...OPERATION MANUAL KNEGT 304G2 WWW KNEGT INTERNATIONAL COM...
Page 86: ...304G2 SERIES TRACTOR OPERATION MANUAL 84 Appendix 3 Scheme of the electric system...
Page 90: ...304G2 SERIES TRACTOR OPERATION MANUAL 88...
Page 93: ...304G2 SERIES TRACTOR OPERATION MANUAL 91...
Page 94: ...304G2 SERIES TRACTOR OPERATION MANUAL 92 Appendix 7 E MARK certificate...
Page 95: ...304G2 SERIES TRACTOR OPERATION MANUAL 93...
Page 96: ...304G2 SERIES TRACTOR OPERATION MANUAL 94...
Page 97: ...304G2 SERIES TRACTOR OPERATION MANUAL 95...
Page 98: ...304G2 SERIES TRACTOR OPERATION MANUAL 96...
Page 99: ...304G2 SERIES TRACTOR OPERATION MANUAL 97...
Page 103: ......