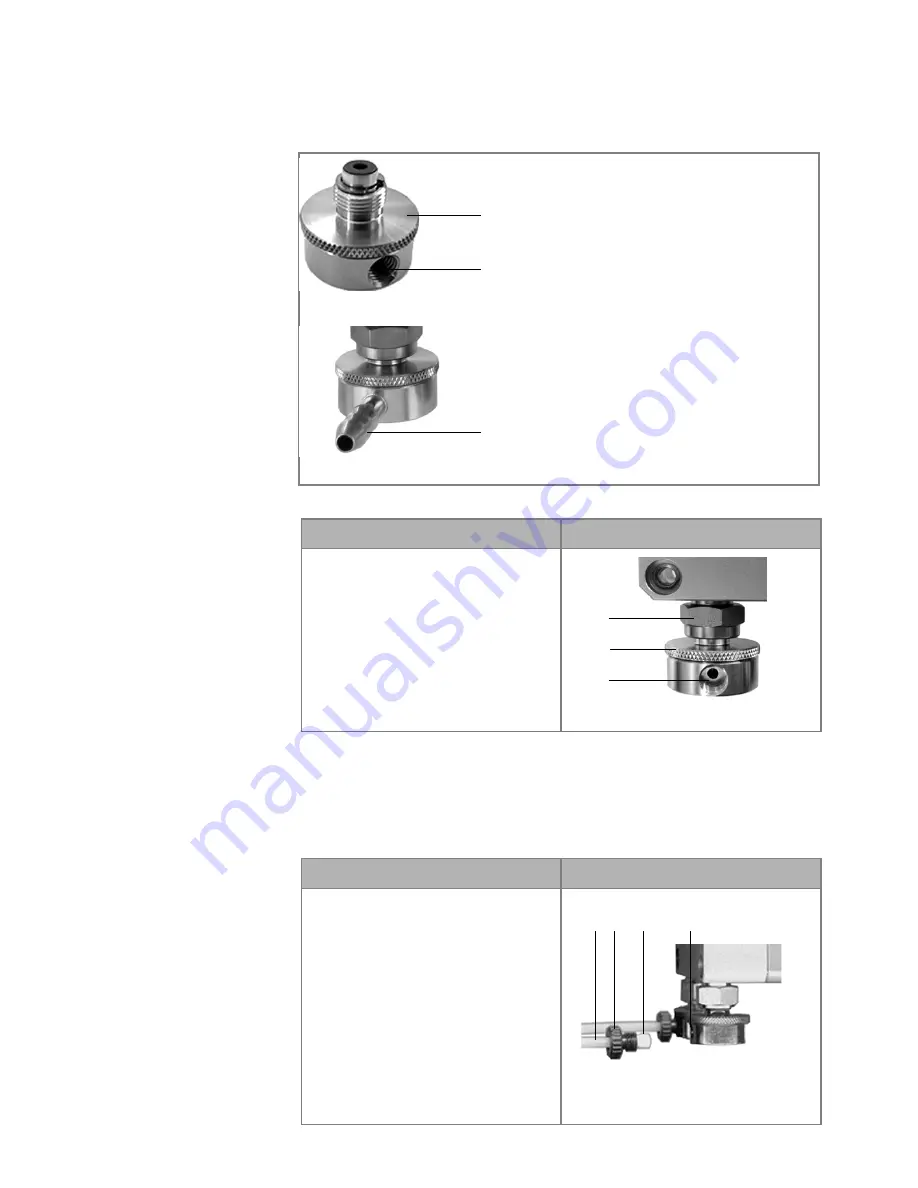
P 2.1L user manual V6840, version
3.
5
Installation
13
Eluent Inlet
The eluent lines are connected by the eluent inlet to the pump head. Before
the eluent lines are connected, the eluent inlet must be attached to the
pump head.
Connecting the Eluent Inlet to the Pump Head
Connecting the Eluent Line
Prerequisite
The eluent inlet has been connected.
Note:
If connecting a pump head from 100 – 500 ml, make sure that the
tapered side of the cutting ring is pointed towards the fastening screw of
the Teflon tube.
Legend
1
Knurled-head screw
2
Eluent inlet
3
Olive-type tube fitting
Fig. 8
Eluent inlet for 100-500 ml pump heads
Fig. 9
Eluent inlet for 1000 ml pump head
1
2
3
Procedure
Process
Figure
1. With the knurled-head screw
2
,
screw the eluent inlet into the
inlet screw fitting
1
of the
pump head.
2. Turn the eluent inlet until the
intake manifold input
3
points
forward.
3. Tighten the knurled-head screw.
Fig. 10
Eluent inlet, variant 1
1
2
3
Procedure
Process
Figure
Pump head:
100 ml
250 ml
500 ml
1. Push the Teflon hose
1
through
the fastening screw
2
and the
cutting ring
3
.
2. Insert the hose end as far as pos-
sible into the eluent inlet fitting
4
of the pump head.
3. Tighten the fastening screw by
hand.
Fig. 11
Connecting the eluent line to
the pump head
2
1
3
4