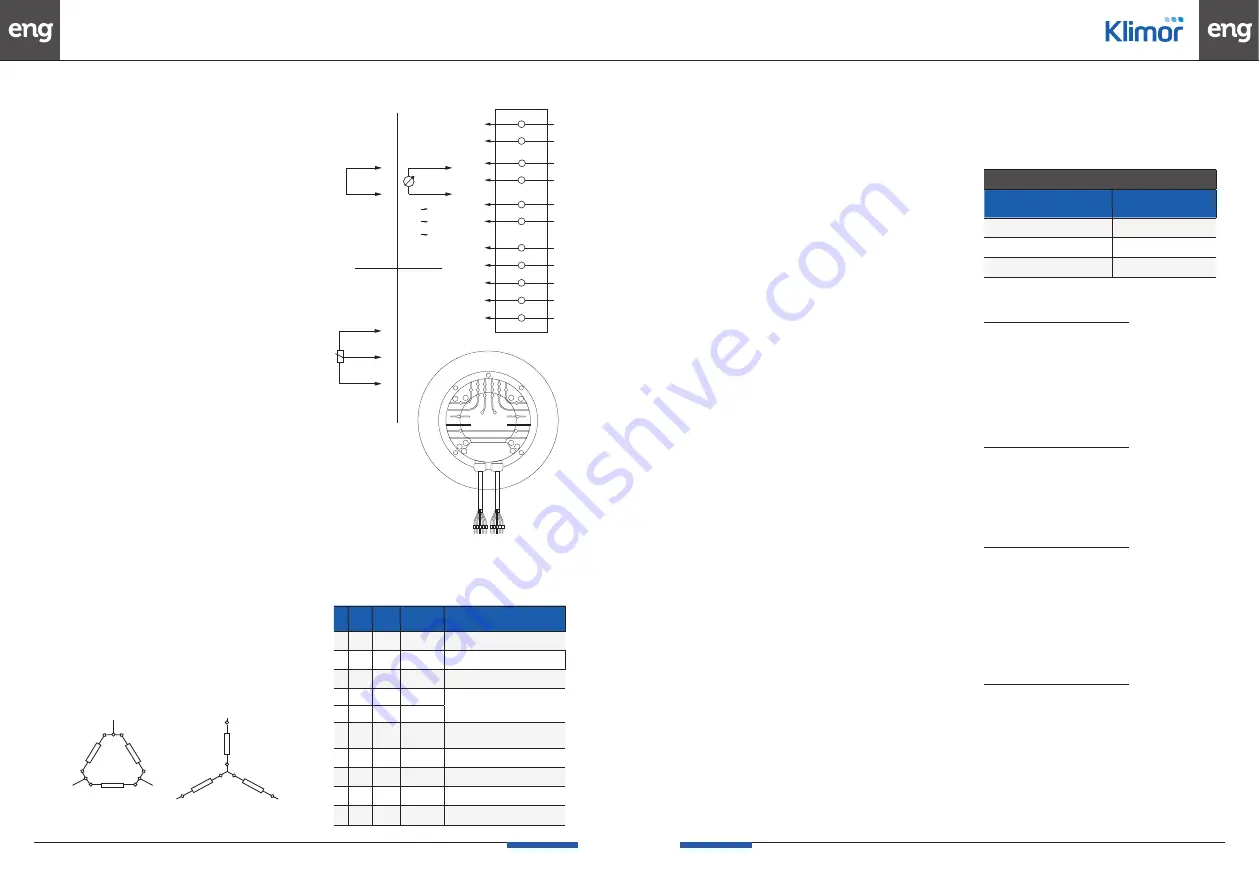
32
33
www.klimor.com
www.klimor.com
MCKT - SUSPENDED MODULAR AIR CONDITIONING AND VENTILATION UNITS
OPERATION AND MAINTENANCE MANUAL
6.10 Electric heater
The electric heater should be connected so as to pre-
vent switching on (operation) of the heater when the
fan is not in operation. The moment the fan is stopped,
heater operation should be stopped as well. Adjust-
ment degrees (1, 2 or 3) of the heater’s power output
are on the terminal strip from which supply wires
should run through stuffing boxes placed in the unit’s
ceiling.
Access to the terminal strip is possible after the inspec-
tion panel has been removed. The strip has got termi-
nals for connecting the neutral and earth wires and ter-
minals for the thermostat protecting against excessive
air temperature rise inside the heater (occurring as a re-
sult of an interruption or reduction of airflow). The ther-
mostat contacts, included in the heater supply control
circuit, open in air temperature close to the thermostat
ranging from 65 to 75ºC. When the temperature drops
by about 25K the thermostat contacts close. The heat-
er control circuit must be unconditionally fitted with
a thermostat. In order to guarantee safe maintenance
operations on the unit in the supply line, a mainte-
nance switch must be installed that allows disconnect-
ing power supply during power consumption. Should
it be necessary to remove the inspection panel of the
module with the motor or/and heater (maintenance,
failure), all supply circuits should be switched off.
6.9 Fan Motor
The fans used in the units are powered by three-phase
squirrel-cage motors, whose revolutions can be easily
controlled by inverters. The recommended setting of
the inverters for the start-up/warm-up time of the fan
is a minimum of 30s. The engine should be powered in
accordance with applicable regulations and standards
and in accordance with data on the motor’s nameplate.
Connection should be done with the use of overload
and short circuit protection depending on the rated
current of the installed motor.
Before connecting the power supply, the diagrams be-
low should be checked for compliance with the data on
the motor’s nameplate.
In order to ensure safe maintenance operations, it is
necessary to install a maintenance switch in the fan
section to cut off power supply to the fan motor. The
switch should be installed within sight of the personnel
performing maintenance operations.
DRAWING 17:
Connection diagram of three-phase motor winding
DRAWING 18:
Connection diagram of
electric fan with built-in
EC motor (electronic
commutation).
In case of a fan with a built-in EC motor, control is done
according to DRAWING 18.
Table No. 5
Connection indication of fan with EC motor
No. Conn.
Destina-
tion
Color
Function
1
1, 2
PE
Green-Yellow
Protective earth
1
3
N
Blue
Power supply cable neutral
1
5
L
Black
Power supply cable phase
1
6
NC
White 1
State ralay: floating status contact,
break with error max 250 V / 2 A, min. 10 mA
1
7
COM
White 2
2
8
0-10V
Yellow
Analogue input 1 (set value);
0-10V; Ri=100kΩ;
2
10
RSB
Brown
RS485 interface for Modbus, RSB
2
11
RSA
White
RS485 interface for Modbus, RSA
2
12
GN
Blue
Reference ground for control interface SELV
2
13
+10V
Red
Fixed voltage 10 V +/-3%;
6.12 Heat Pump Module
Complete information about the power connection of
the heat pump module is available in OMM of control
system.
6.13 Control system
Since it is possible to use one of many control systems,
this manual does not include information regarding
the installation of automation elements, their start-up
and operation.
MCKT units are fitted with automation elements that
are installed inside the unit, i.e. antifreeze thermostat
for water heaters and thermostat preventing overheat-
ing in electric heaters. These elements have protective
functions only when cooperating with the appropriate
control system.
All information is included in OMM re. control system.
7. Preparing for First Start-up
Only appropriately qualified and trained installation and
start-up team can perform first start-up of the unit after the
ventilation or air conditioning installation has been com-
missioned.
It is a requirement that start-up be preceded by the follow-
ing operations:
• checking whether all the unit’s modules are connected
together and suspended correctly,
• checking whether the air installation has been con-
nected correctly and there are no leaks,
• checking hydraulic and Freon installations for leaks,
their readiness for work and whether the heating or
cooling medium is available at start-up,
• checking whether power connections are correct,
checking wiring and operational readiness of power
receivers,
• checking correct installation of traps and the system for
condensate drain from drip trays,
• checking correct installation of automation elements.
Moreover, it is necessary to clean the interior of unit casings
and ducts cooperating with them. One should also make sure
that the parts of the units, hydraulic installation and automa-
tion fittings have not been damaged during installation works.
7.1 Power Supply Installation
It should be checked whether power installation and
safeties of all power receivers have been connected
properly.
7.2 Filters
Remove protective foil from filters. Make sure the con-
dition of the filters is correct (leakproofness, fixing on
the tracks). Set the pressure switches correctly (if they
have been removed), determining the admissible final
drop of static pressure on the filter – when the drop
has been exceeded, it is recommended that the filter
be renewed.
The table presents the admissible pressure drop for the
filters used:
Table No. 6
Filter Type and Class
FILTER TYPE AND CLASS IN MCKT
Filter Type and Class
Admissible Pressure Drop
according to PN-EN13053:2008
Cassete Filter G1÷G4 (EU1-EU4)
150 Pa
Bag Filter M5÷F7 (EU5-EU7)
200 Pa
Bag Filter F8÷F9 (EU8-EU9)
350 Pa
7.3 Water Heaters
The following should be checked:
• condition of exchanger lamellas (mechanical damage,
contamination),
• correct connection of supply and return pipeline,
• fixing of antifreeze thermostat capillary, which should be
undone on the heater,
• set the antifreeze thermostat to +4°C,
• whether the exchanger is free of air.
7.4 Electric Heaters
The following should be checked:
• condition of electric heating elements of the heater, if
they are not damaged or are not in contact with the ele-
ments inside the heating module,
• correctness of power connections,
• correct connection of protective thermostat.
7.5 Water and DX cooling coils
The following should be checked:
• condition of exchanger lamellas (mechanical damage,
contamination),
• correct connection of supply and return pipeline,
• position of condenser with regard to airflow direction,
• correct fixing of the trap, trapping height and perme-
ability of the drain installation. Before start-up of the
unit the trap must be filled with water,
• whether the exchanger is free of air.
7.6 Cross-flow Counter-current Exchanger
The following should be checked:
• condition of exchanger lamellas (mechanical damage,
contamination),
• operation of the air damper mounted on the exchang-
er and bypass air damper,
• correct fixing of the trap, trapping height and perme-
ability of the drain installation. Before start-up of the
unit the trap must be filled with water.
• Check the mounting of the actuator on the bypass
damper and in the case of HPM on the actuator on
exchanger damper. Check the direction of acuator
rotation.
TRIANGLE CONNECTION
STAR CONNECTION
PE
PE
N
L
NC
COM
0-10V
RSB
RSA
GND
10V
CUSTOMER CIRCUIT
full speed
adjustable speed
with potentiometer
8
2
3
5
6
7
8
10
11
12
13
1
12
external
adjustable
speed signal
(0-10V)
FAN CIRCUT
8
+
_
13
1-10V
10V n=max
1 V n=min
<
1V n=0
13
8
10K
12
PE
PE
N
L
NC
COM
0-10V
RSB
RSA
GND
10V
CUSTOMER CIRCUIT
full speed
adjustable speed
with potentiometer
8
2
3
5
6
7
8
10
11
12
13
1
12
external
adjustable
speed signal
(0-10V)
FAN CIRCUT
8
+
_
13
1-10V
10V n=max
1 V n=min
<
1V n=0
13
8
10K
12