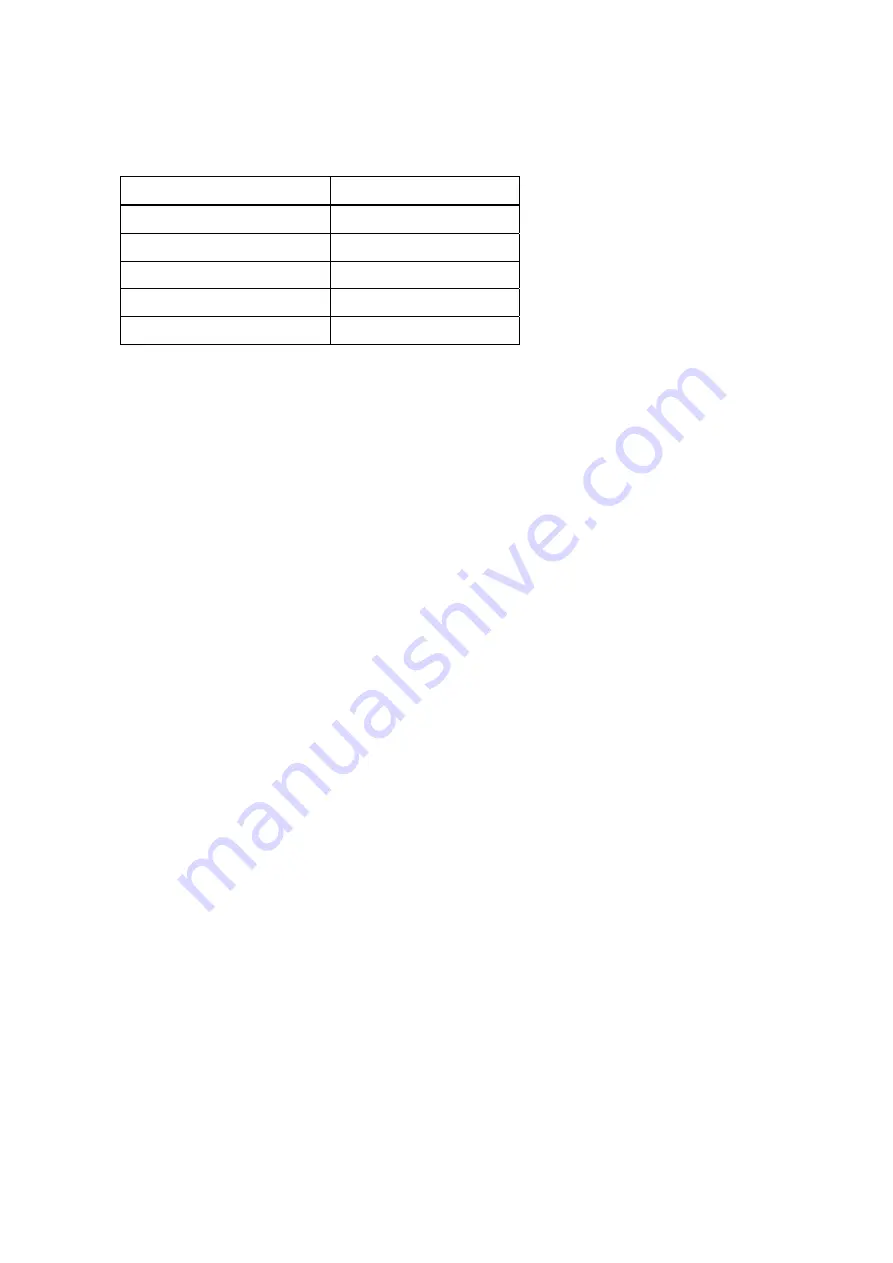
13
4-4. Recommended Lubricating Oil
・
Grade of Viscosity : ISO VG32
4-5. Safety of Oil and Antirust Oil Used for the Unit
4-5-1. Scope of application
・
Specified lubricating oil
・
Specified hydraulic oil
(
MR
,
MRT
,
MX
,
GT
,
TM2100
・
3100
,
TH2100
・
3100
,
TT(S)101
・
120
,
TT140
,
DM do not use
)
・
Antirust oil applied to the unit at delivery (Houghton Japan, Rust Veto 377)
4-5-2. First-aid treatment
Aspiration: In case of much aspiration, go to a place where there is fresh air, and cover
your body with a blanket to keep your body warm. Consult a doctor if necessary.
Sticking to your skin: Wipe off the oil, and wash your skin with water and soap. If you feel
itchy or you get inflamed, consult a doctor immediately.
Entering your eye: Wash your eye with fresh water for at least 15 minutes, and then consult
a doctor.
Accidental drinking: Consult a doctor immediately without vomiting forcibly. If you are
polluted in your mouth, wash with water thoroughly.
・
For lubrication oils and hydraulic oils other than specified ones, and antirust oils
prepared by the customer, refer to the safety information prepared for respective
oils.
4-5-3. Flammable characteristics
・
Watch out for fire since lubricating oil and hydraulic oil are flammable. Hazardous
substances will be generated if they combusted.
・
The flash point of lubricating oil and hydraulic oil put in the unit at the delivery
exceeds 200
°
C. It may be different from that of the lubricating oil and hydraulic oil
prepared by the customer.
Maker Oil
Name
IDEMITSU
Daphne Multiway 32MT
MOBIL
Vactra oil No.1
JX NIPPON OIL
&
ENERGY
Uniway EV 32
SHELL
Shell Tonna oil S32
COSMO Dynaway
32
Summary of Contents for MR250RAE13
Page 2: ......
Page 39: ...33 Note 1 Left Hand Front Side Back Side Note 1 ...
Page 47: ......
Page 48: ......
Page 49: ......