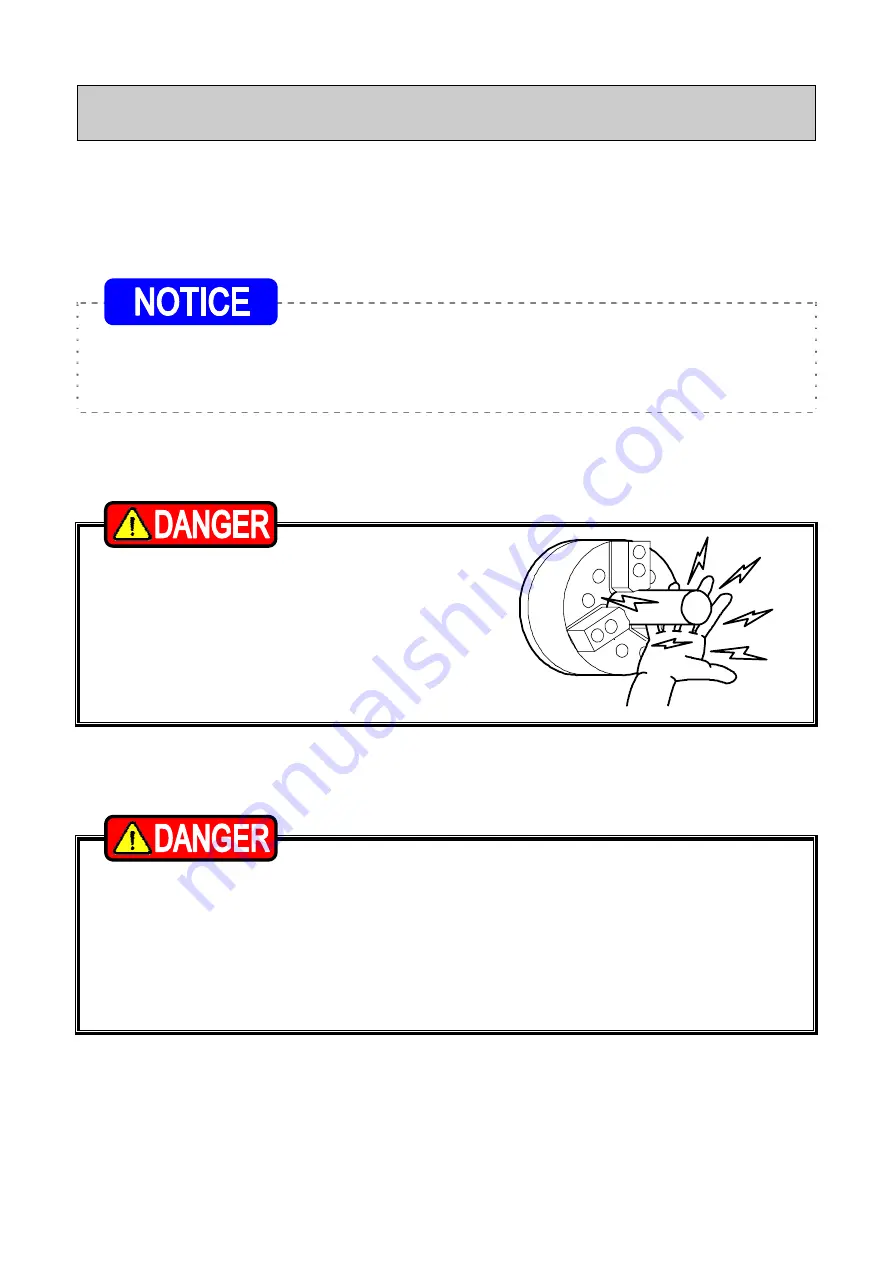
5. Usage
This product is a device to fix a work-piece when it is processed by the rotary table.
The handle closes the jaw manually and fixes a work-piece so that it does not move during
processing. The chuck opens the jaw after having processed it and remove a work-piece.
22
・
When replacing the top jaw, carefully clean the top jaw and the cross-key (key and
keyway) of base jaw. If not, it will cause an inadequate deflection accuracy.
5-1. Precautions during gripping work with chuck
・
When gripping a work with the
chuck, do not get fingers or hands
become caught. This could cause
crushed or cut fingers and hands.
5-2. Precautions during gripping work in irregular shape
・
If a work in an irregular shape is gripped the jaw may be broken. Consult our
company or the distributor if there is any concern.
・
Cast metal, pitched shape or taper shape cannot be gripped.
・
If the protrusion of the work is long, support it with a center or the steady rest.
If the protrusion is long the tip of the work turns, and this is dangerous as the
work will fly out.
Summary of Contents for JN N Series
Page 7: ...1 3 Parts list Fig 3 6...