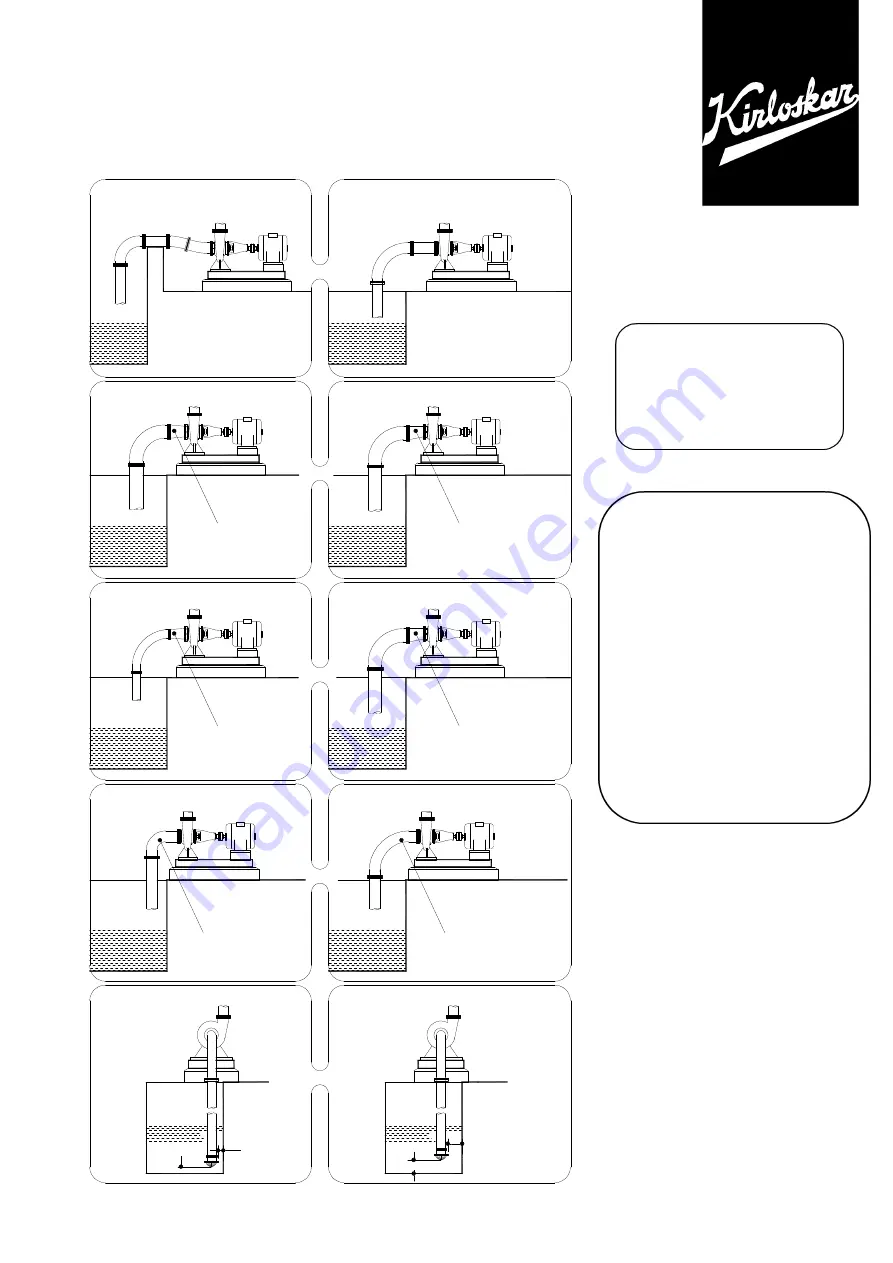
INCORRECT CORRECT
D
D
SPACE AROUND
FOOT VALVE
INSUFFICIENT
SHORT BEND
REDUCED SUCTION PIPE
D
D
SUFFICIENT
FOOT VALVE
SPACE AROUND
LONG BEND
INCREASED SUCTION PIPE
CONCENTRIC TAPER PIECE
INCORRECT LAYOUT OF SUCTION PIPE
ECCENTRIC TAPER PIECE
CORRECT LAYOUT OF SUCTION PIPE
FOR RECOMMENDATIONS OF
SUITABLE SUCTION AND
DELIVERY PIPE SIZE PLEASE
CONTACT OUR AUTHORISED
DEALER OR NEAREST
REGIONAL OFFICE
GENERAL
INSTRUCTIONS
FOR
INSTALLATION
OPERATION &
MAINTENANCE OF
KIRLOSKAR
CENTRIFUGAL
PUMPS
® Registered users – Kirloskar Brothers Ltd.
Summary of Contents for 65-DSM 315M
Page 15: ...14 CROSS SECTION ASSEMBLY OF DSM 1E CCW CROSS SECTION ASSEMBLY OF DSM 2E CCW...
Page 17: ...16...
Page 18: ...17 CROSS SECTIONAL ASSEMBLY OF DSM 3ME CCW NOTE ALSO FOR DSM 3 3 ME...
Page 29: ...1...
Page 30: ...2...
Page 43: ...15 7 1 2 NON THRU BORE TYPE PUMP Mechanical seal type...
Page 46: ...18...
Page 47: ...19...
Page 48: ...20...
Page 49: ...21...
Page 50: ...22...
Page 51: ...23...
Page 52: ...24...
Page 53: ...25...
Page 54: ...26...