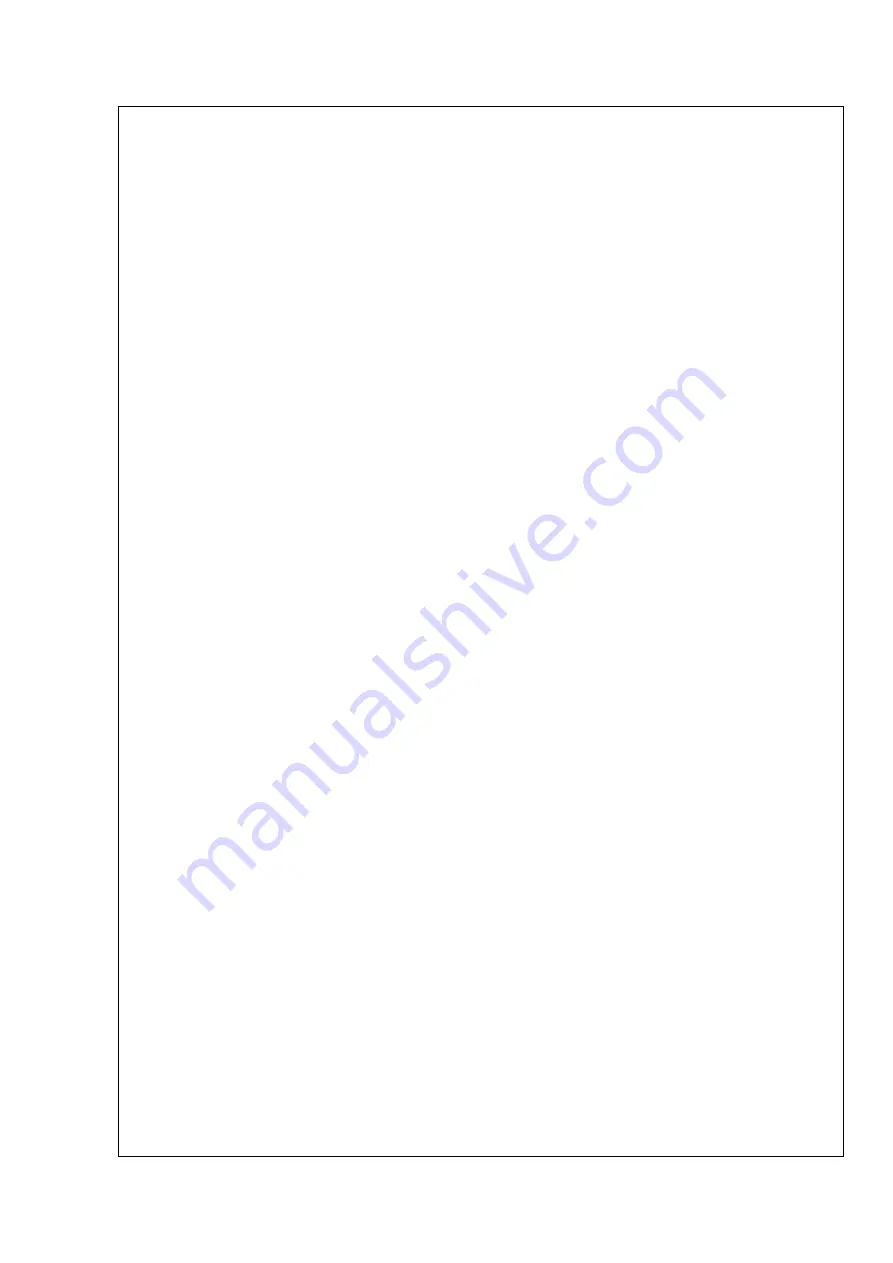
CHECK POINTS
1. Suction pipe, foot valve choked.
2. Nominal diameter of suction line too small.
3. Suction pipe not sufficiently submerged.
4. Too many bends in the suction line.
5. Clearance around suction inlet not sufficient.
6. Shut off valve in the suction line in
unfavourable position.
7. Incorrect layout of suction line (formation of air
pockets).
8. Valve in the suction line not fully open.
9. Joints in the suction line not leak-proof.
10. Air leaking through the suction line and stuffing
box etc.
11. Suction lift too high.
12. Suction head too low (difference between
pressure at suction connection and vapour
pressure too low).
13. Delivery liquid contains too much gas and/or
air.
14. Delivery liquid too viscous.
15. Insufficient venting.
16. Number of revolutions too high.
17. Number of revolutions too low.
18. Incorrect direction of rotation (electric motor
incorrectly connected, leads of phases on the
terminal block interchanged).
19. Impeller clogged.
20. Impeller damaged.
21. Casing rings worn out.
22. Separation of crystals from the flow of
pumping liquid (falling below the temperature
limit/equilibrium temp).
23. Sealing liquid line obstructed.
24. Sealing liquid contaminated.
25. Lantern ring in the stuffing box is not
positioned below the sealing liquid inlet.
26. Sealing liquid omitted.
27. Packing incorrectly fitted.
28. Gland tightened too much/slanted.
29. Packing not suitable for operating conditions.
30. Shaft sleeve worn in the region of the packing.
31. Bearing worn out.
32. Specified oil level not maintained.
33. Insufficient lubrication of bearings.
34. Ball bearings over-lubricated.
35. Oil/Grease quality unsuitable.
36. Ball bearing incorrectly fitted.
37. Axial stress on ball bearings (no axial clearance
for rotor).
38. Bearings dirty.
39. Bearings rusty (corroded).
40. Axial thrust too great because of worn casing
rings, relief holes obstructed.
41. Insufficient cooling water supply to stuffing box
cooling.
42. Sediment in the cooling water chamber of the
stuffing box cooling.
43. Alignment of coupling faulty or coupling loose.
44. Elastic element of coupling worn.
45. Pump casing under stress.
46. Pipeline under stress.
47. Shaft runs untrue.
48. Shaft bent.
49. Rotor parts insufficiently balanced.
50. Rotor parts touching the casing.
51. Vibration of pipe work.
52. Non-return valve gets caught.
53. Contaminated delivery liquid.
54. Obstruction in delivery line.
55. Delivery flow too great.
56. Pump unsuitable for parallel operation.
57. Type of pump unsuitable.
58. Incorrect choice of pump for existing operating
conditions.
59. Voltage too low/power supply overloaded.
60. Short circuit in the motor.
61. Setting of starter of motor too high.
62. Temperature delivery liquid too high.
Summary of Contents for 65-DSM 315M
Page 15: ...14 CROSS SECTION ASSEMBLY OF DSM 1E CCW CROSS SECTION ASSEMBLY OF DSM 2E CCW...
Page 17: ...16...
Page 18: ...17 CROSS SECTIONAL ASSEMBLY OF DSM 3ME CCW NOTE ALSO FOR DSM 3 3 ME...
Page 29: ...1...
Page 30: ...2...
Page 43: ...15 7 1 2 NON THRU BORE TYPE PUMP Mechanical seal type...
Page 46: ...18...
Page 47: ...19...
Page 48: ...20...
Page 49: ...21...
Page 50: ...22...
Page 51: ...23...
Page 52: ...24...
Page 53: ...25...
Page 54: ...26...