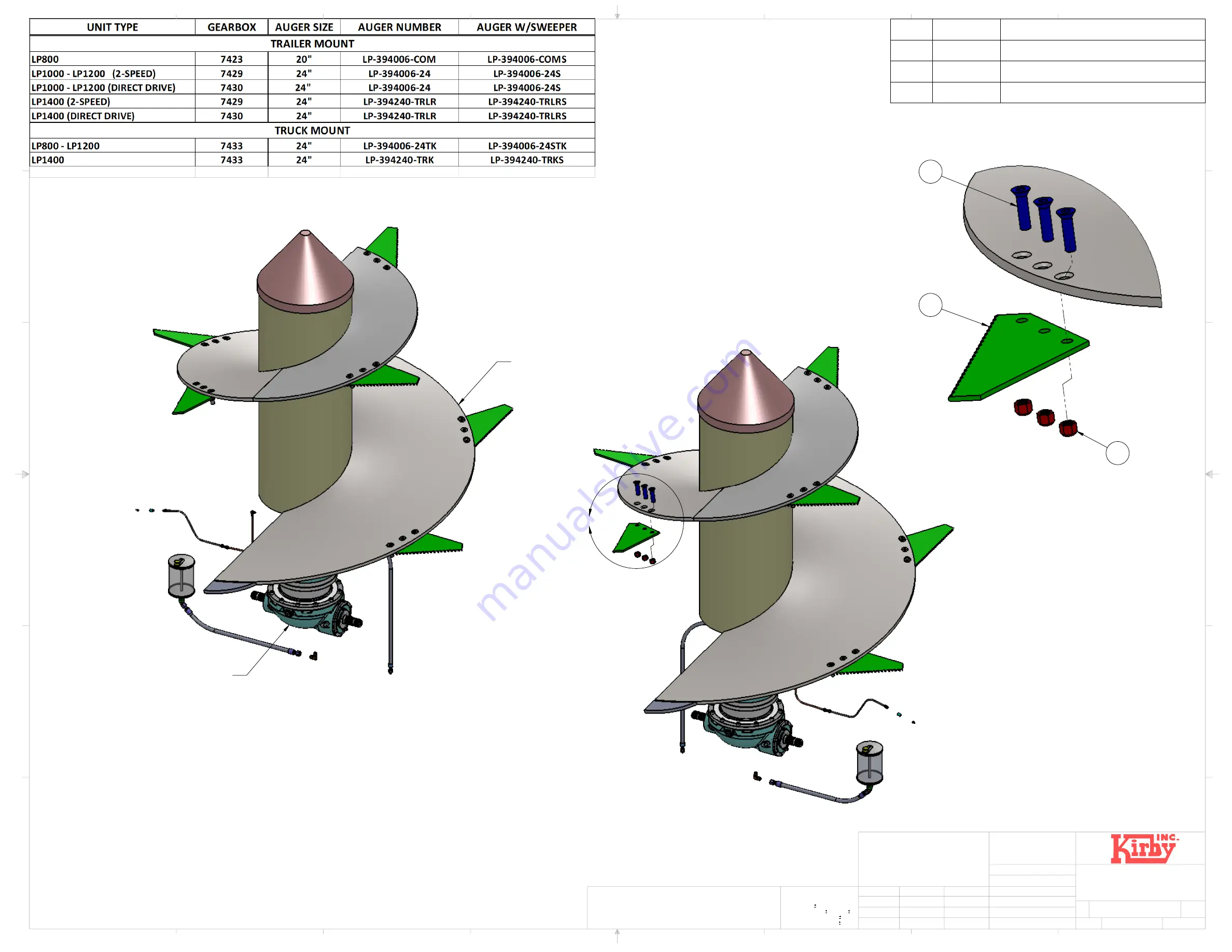
A
AUGER, SEE NOTE-1
GEARBOX, SEE NOTE-1
DETAIL A
3
1
2
NOTE: UNIT SERIAL # NEEDED
FOR ALL PART ORDERS
NOTES:
UNLESS OTHERWISE SPECIFIED
1 - SEE TABLE ABOVE FOR AUGER AND GEARBOX SELECTION,
OTHER VARIATIONS MAY EXIST.
AUGER BLADES SOLD SEPARATELY
ITEM NO. PART NUMBER
DESCRIPTION
1
7774
BLADE, VERTICAL AUGER
2
10647
NUT, 3/4" NC, NYLOCK
3
10730
BOLT, FLTHD SOCKET, 3/4" NC X 3" LG.
D
C
B
A
A
B
C
D
1
2
3
4
5
6
7
8
8
7
6
5
4
3
2
1
E
F
E
F
8-11-17
FINISH:
JOB #:
MATERIAL P/N:
MATERIAL:
SEE BOM
NAME
DATE
APPROVED BY:
DESIGNED BY:
DRAWN BY:
VENDOR:
VENDOR P/N:
SIZE
C
REV.
WEIGHT:
SCALE: 1:12
SHEET 1 OF 1
LP-002D
PART NUMBER
DESCRIPTION
AUGER AND
GEARBOX SELECTION
MCCLURE
DIMENSIONS ARE IN INCHES
TOLERANCES:
FRACTIONAL
ANGULAR: MACH BEND
TWO PLACE DECIMAL
THREE PLACE DECIMAL
THE INFORMATION CONTAINED IN THIS DRAWING IS THE SOLE PROPERTY OF
KIRBY MANUFACTURING INCORPORATED. ANY REPRODUCTION IN PART OR AS
A WHOLE WITHOUT THE WRITTEN PERMISSION OF KIRBY MANUFACTURING
INCORPORATED IS STRICTLY PROHIBITED.
PROPRIETARY AND CONFIDENTIAL
Notes:
P.O. BOX 989
MERCED CA 95340
PH (209)723-0778
FX (209)723-3941
Kirby Mfg Inc.
2790.041763 lbs
8-11-17
Summary of Contents for LP1000
Page 76: ...NOTE UNIT SERIAL NEEDED FOR ALL PART ORDERS ...
Page 77: ...NOTE UNIT SERIAL NEEDED FOR ALL PART ORDERS ...
Page 88: ......
Page 89: ......
Page 90: ......