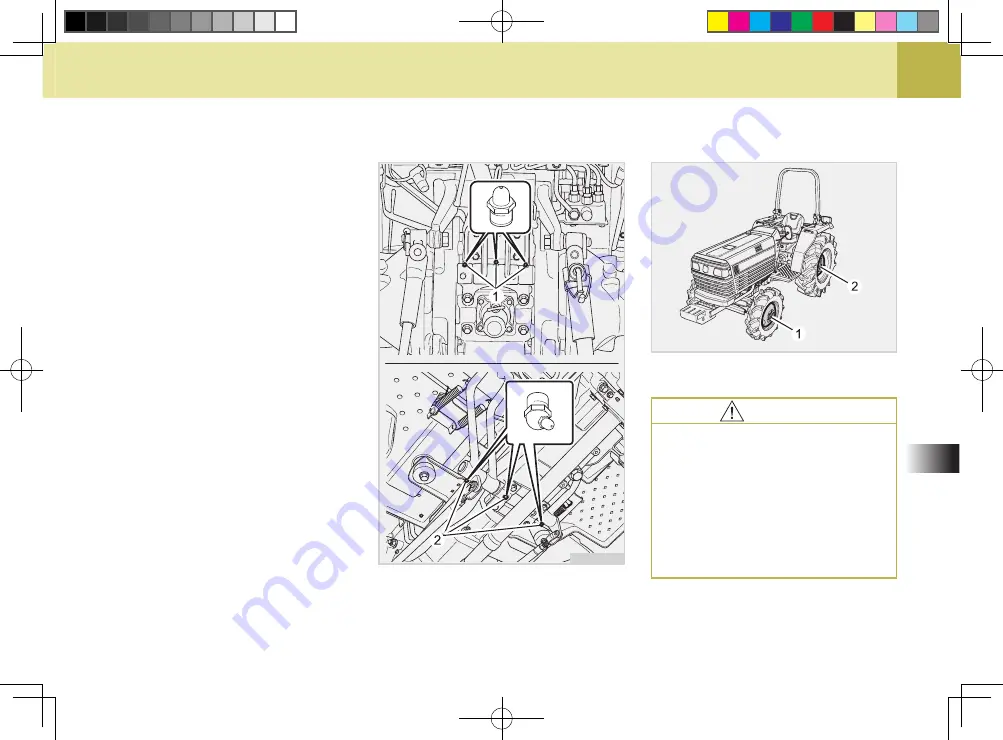
6
-1
PERIODIC SERVICE
6
eVeRY 50 hOURs
lUBRicatinG GRease FittinGs
You should apply a small amount of
multi-purpose grease to the following
points every 50 hours or as needed.
If your tractor is operated in extreme-
ly wet, muddy, or dusty conditions
you should lubricate the fittings more
often.
(1) Grease Fittings (Top Link Holder)
(2) Grease Fitting (Brake Pedal,Clutch Pedal)
621Oa17a
Check wheel bolts and nuts regular-
ly especially when new. If they are
loose, tighten them as follows.
checkinG Wheel BOlt
tORqUe
(1) 176 N·m (18 kgf·m, 130 lbf·ft)
(2) 284.4 N·m (29 kgf·m, 290.7 lbf·ft)
621Oa18a
caUtiOn
To avoid personal injury:
Never operate tractor with a
loose rim, wheel, or axle.
Any time bolts and nuts are
loosened, retighten to speci
-
fied torque.
Check all bolts and nuts fre
-
quently and keep them tight.
L3503_LK45-호주향-06.indd 17
2008-12-18 오후 1:53:21
Summary of Contents for L3503
Page 6: ...L3503_LK45 00 indd 6 2008 12 17 1 55 35...
Page 20: ...1 14 L3503 LK45 621O131a TRACTOR SAFETY LABELS L3503_LK45 01 indd 14 2008 12 18 1 51 54...
Page 23: ...SERVICING 2 2 SERVICING OF TRACTOR 2 2 L3503_LK45 02 indd 1 2008 12 18 1 52 04...
Page 32: ...MEMO MEMO L3503_LK45 03 indd 8 2008 12 18 1 52 17...
Page 38: ...MEMO MEMO L3503_LK45 04 indd 6 2008 12 18 1 52 25...
Page 114: ...MEMO MEMO L3503_LK45 07 indd 4 2008 12 18 1 53 41...
Page 122: ...MEMO MEMO L3503_LK45 08 indd 8 2008 12 18 1 53 50...
Page 123: ...INDEX 9 INDEX 9 2 9 L3503_LK45 09 indd 1 2008 12 18 1 53 56...