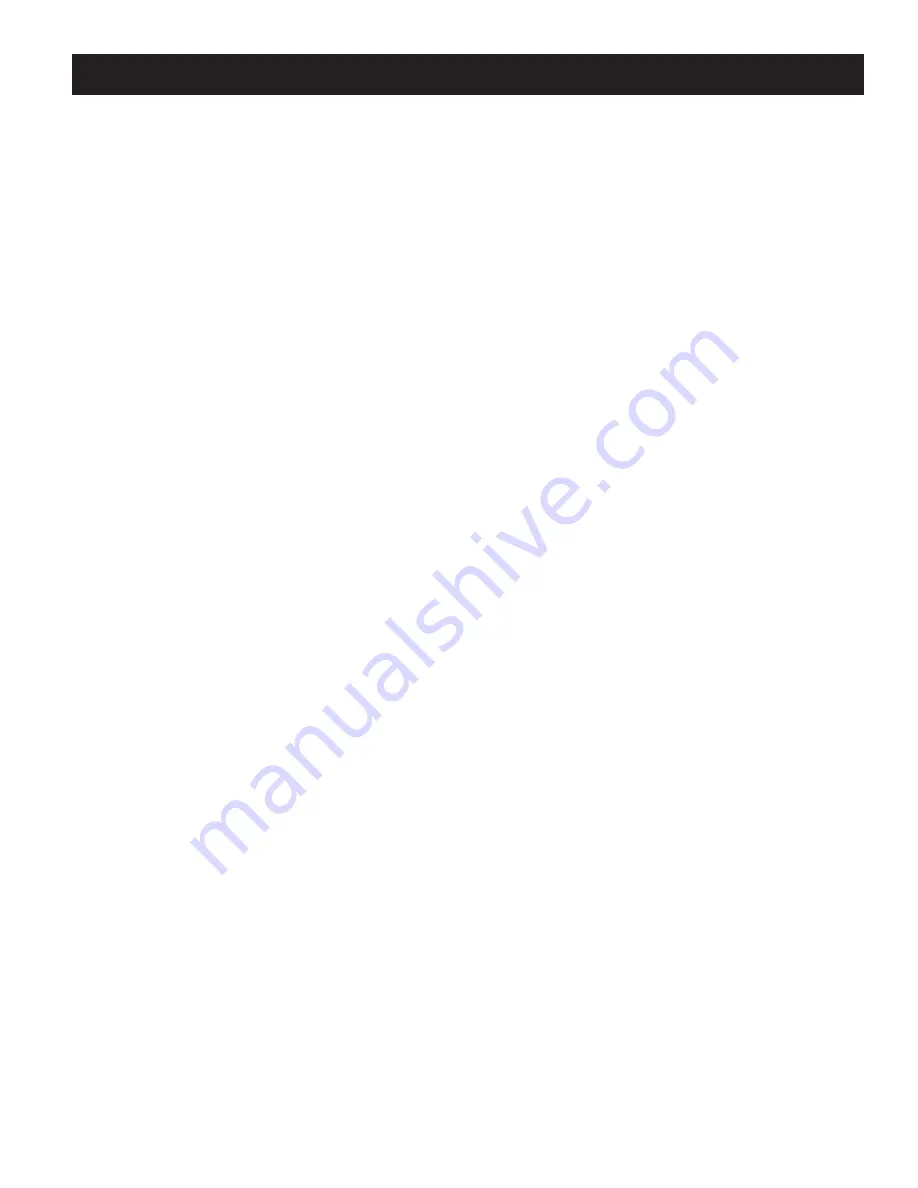
3
PRE-INSTALLATION QUESTIONS and ANSWERS
Why does my fireplace or stove give off odour?
It is normal for your fireplace to give off some odour. This is due to the curing of the paint, adhesives,
silicones and any undetected oil from the manufacturing process as well as the finishing materials used
with the installations (e.g. marble, tile and the adhesives used to adhere this product to the walls can react
with heat and cause odours).
It is recommended that you burn your gas fireplace or stove for a minimum of four hours at a time with
the fan off after the curing of the paint has been completed. These odours can last upward to 40 hours of
burn time, keep burning at a minimum of four hours per use until odours dissipate.
About curing of the paint
Your stove or fireplace has been painted with the highest quality silicone stove paint. This paint dries
quickly in 15-20 minutes when first applied at the factory. However, due to the high temperature silicone
components, the paint will cure when heat is applied to the appliance as it is first used.
The following information
applies to the curing process
to get the paint fully hard and durable.
Fire the appliance four successive times for 10 minutes each firing and a 5 minute cool down between
each. Be aware during log and firebox paint curing that a white deposit may be developing on the inside
of the glass doors. It is important to remove this white deposit from the glass doors with an appropriate
cleaner to prevent build-up (such as Windex or a commercial fireplace glass cleaner).
• Babies, small children, pregnant women and pets should leave the area during the cure phase.
• Ventilate well, open doors and windows.
• Do not touch during curing.
Noise coming from the fireplace?
• Noise caused by metal expanding and contracting as it heats up and cools down, similar to the sound
produced by a furnace or heating duct. This noise does not affect the operation or longevity of your
fireplace.
• Different types and thicknesses of steel will expand and contract at different rates resulting in
“cracking” and “ticking” sounds throughout the heating and cooling periods.
• You should also be aware that as temperatures change within the unit these sounds will likely re-
occur. Again this is normal for steel fireboxes, and is not a defect.
Cleaning the Glass
During the first few fires, a white film may develop on the glass front, as part of the curing process. The
glass should be cleaned after the unit has cooled down or the film can bake on and become very difficult
to remove. Use a non-abrasive cleaner and do not attempt to clean the glass while it is hot.