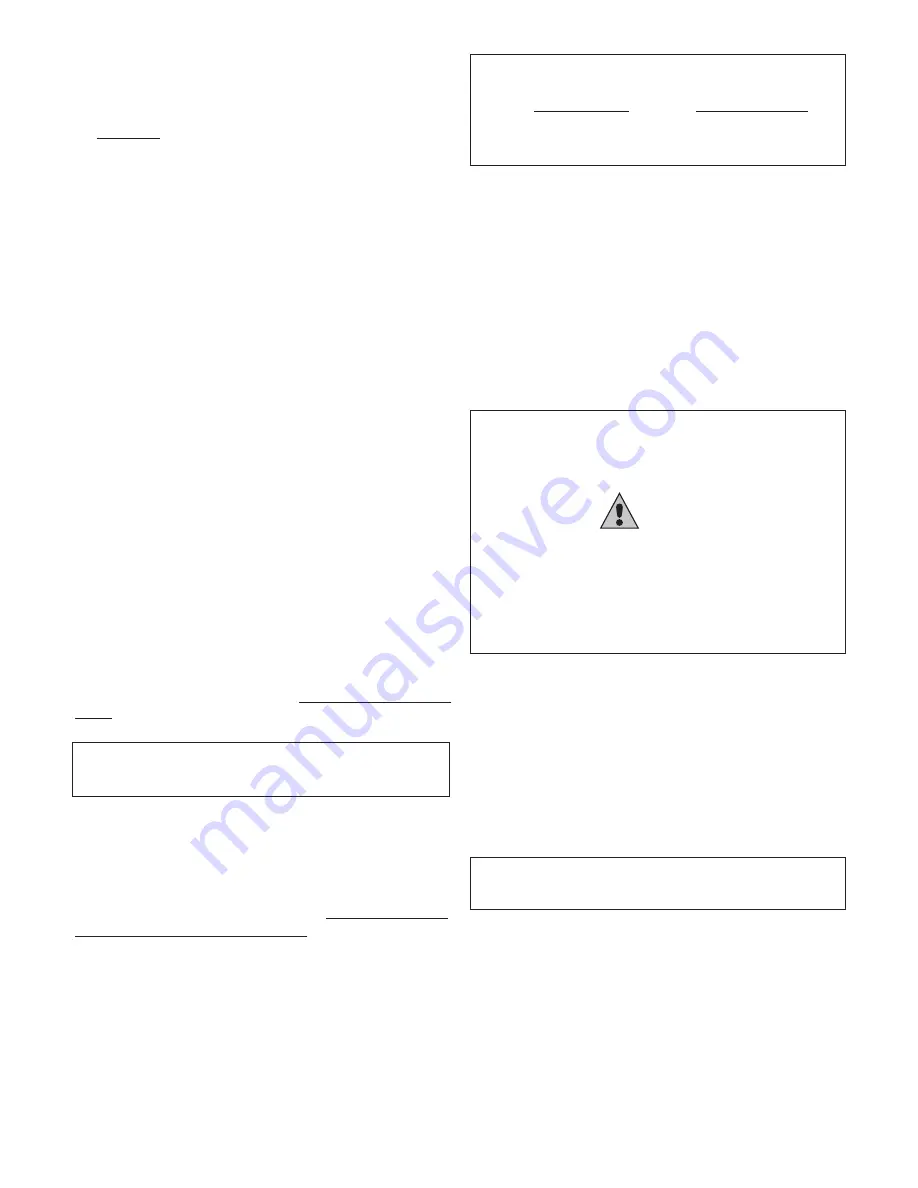
8
Thermostat Connection and On/Off Switch
Millivolt
Thermostat ( optional but recommended). All controls
are connected directly to the gas valve and the circuit is
made between:
• SIT Valve
TH
and
TP- TH,
See Section
19
6. GAS PIPING
All gas piping must be done in accordance with all
applicable codes CAN./CGA-BI49.1 or installation codes
or ANSI -Z223.1 as well as local codes.
The appliance and its individual shutoff valve must be
disconnected from the gas supply piping system during
any pressure testing of that system at test pressures in
excess of 1/2 psig (3.5 kPa).
The appliance must be isolated from the gas supply
piping system by closing its individual manual shutoff
valve during any pressure testing of the gas supply
piping system at test pressures equal to or less than 1/2
psig (3.5 kPa).
The gas line to the fireplace insert should be of
adequate size to minimize the pressure drop and should
never be smaller than that supplied with the valve. A
ground joint union should be used as close to the valve
as possible to facilitate removal of the gas valve and
burner base pan.
Check that the gas piping is not supported by the gas
valve. A manual shut-off valve should be installed in the
gas line, inside the fireplace. All piping joints must be
tight and an approved non-hardening sealing compound
shall be used ( one which is suitable for future service).
For the state of Massachusetts a
T-handle gas shut-off
valve
must be used on a gas appliance. This T-handle
gas shut-off valve must be listed and approved by the
state of Massachusetts. This is in reference to the state
of Massachusetts state code CMR238.
7. VENTING
Before any vent liner is run through a masonry chimney
or other approved venting system the
chimney must be
inspected. cleaned and repaired
if necessary . A
chimney which was used for a solid fuel fireplace must
be professionally cleaned in order to reduce corrosion of
the vent and other possible safety hazards.
CAUTION: Never use a flame to check for
leaks - use an approved leak test solution.
VENT LENGTH (4” Diameter Vent)
Vertical (rise)
Horizontal (run)
Min l0 ft - 3.1m
0 ft - 0.0 m
Max 50 ft - 16.2 m
2 ft - 0.6 m
This fireplace insert is approved for use with a
4” inch diameter.
All venting lining products must be approved and
installed according to the vent manufactures installation
instructions. All vent liners must terminate in a rain cap
to prevent debris and rain from entering the vent and
possibly damaging the appliance or creating an unsafe
condition. The area between the existing chimney and
liner must be capped off for the same reasons as above
and to reduce the chances of venting problems and
corrosion of the vent.
It is strongly recommended that the area between the
damper and the liner be blocked to prevent the
possibility of flue products entering the area between
the chimney and the vent liner.
If this fireplace insert is to be used to replace an existing
fireplace insert the existing vent liner must be of the
proper size and if so it must be inspected for
obstructions, damage and/or corrosion. Replacement
must be done as necessary .
This heater must be properly connected to a
venting system. This heater is equipped with
a vent safety spill switch shutoff system.
WARNING
Operation of this heater when not connected to a
properly installed and maintained venting
system or tampering with the vent safety spill switch
shutoff system can result in carbon monoxide (CO)
poisoning and possible death.
NOTE: Follow vent manufacturerʼs
installation instructions.