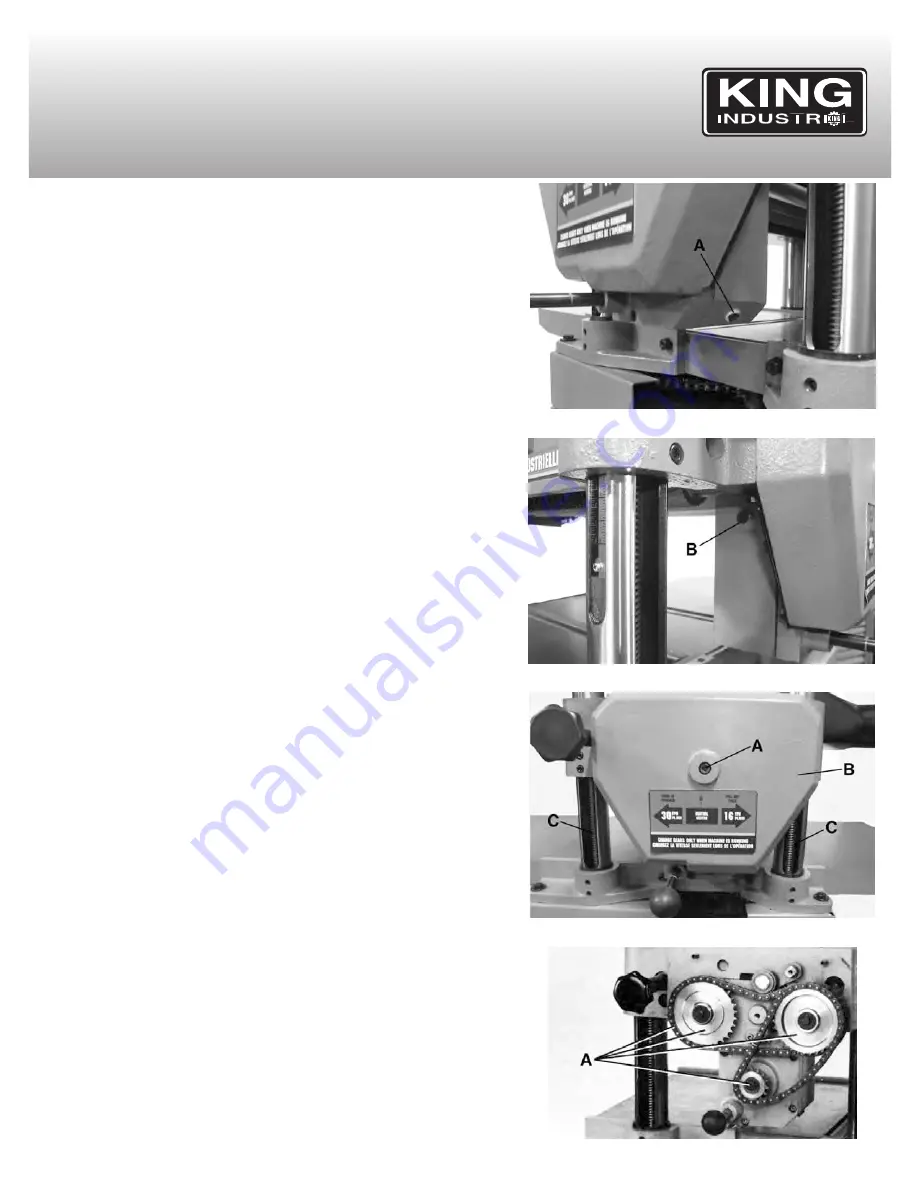
LUBRICATION & MAINTENANCE
LUBRICATION
The gear box oil should be changed after the first 20 hours of operation as part
of the normal break-in procedure, and then once a year using automotive
grade gear oil (80W-90W). The gear box drain plug (A) Fig.34 is located at the
bottom of the gear box. The oil fill and level plug (B) Fig.35 is located on the
side of the gear box.
The proper oil level is reached when it reaches the bottom of the oil fill and
level plug hole.
The four raising lead screws (C) Fig.36 should be lubricated as required using
a common grease.
Periodically remove cap screw (A) Fig.36 and side cover (B). Thoroughly
clean chains and sprockets (A) Fig.37 and lubricate using a light machine oil.
Replace side cover.
Cleaning maintenance
Regularly clean the planer parts to keep them in optimal condition, vacuum
excess wood chips and sawdust. Excessive dust and wood chips in the motor
could cause excessive heat. Every effort should be made to prevent foreign
material from entering the motor. A visual inspection should be made at
frequent intervals. Accumulations of dry dust can usually be blown out to
prevent the interference with normal motor ventilation. To remove dust, blow
off motor with a low pressure air hose.
The operator performing this cleaning function should wear safety glasses
and a filter mask. If any servicing (other than the above cleaning) becomes
necessary, it should be performed by an authorized service centre.
Daily maintenance:
- Clean unpainted surfaces of the table and relubricate.
Weekly maintenance:
- Clean cutterhead.
- Lubricate the lead screws (C) Fig.36 of the four columns.
Monthly maintenance:
- Inspect V-belts for tension.
- Clean dust build-up on motor.
- Lubricate lead screws.
- Lubricate chain.
Yearly maintenance:
- Change gear box oil (80W-90W automotive grade gear oil).
FIGURE 34
FIGURE 35
FIGURE 36
FIGURE 37