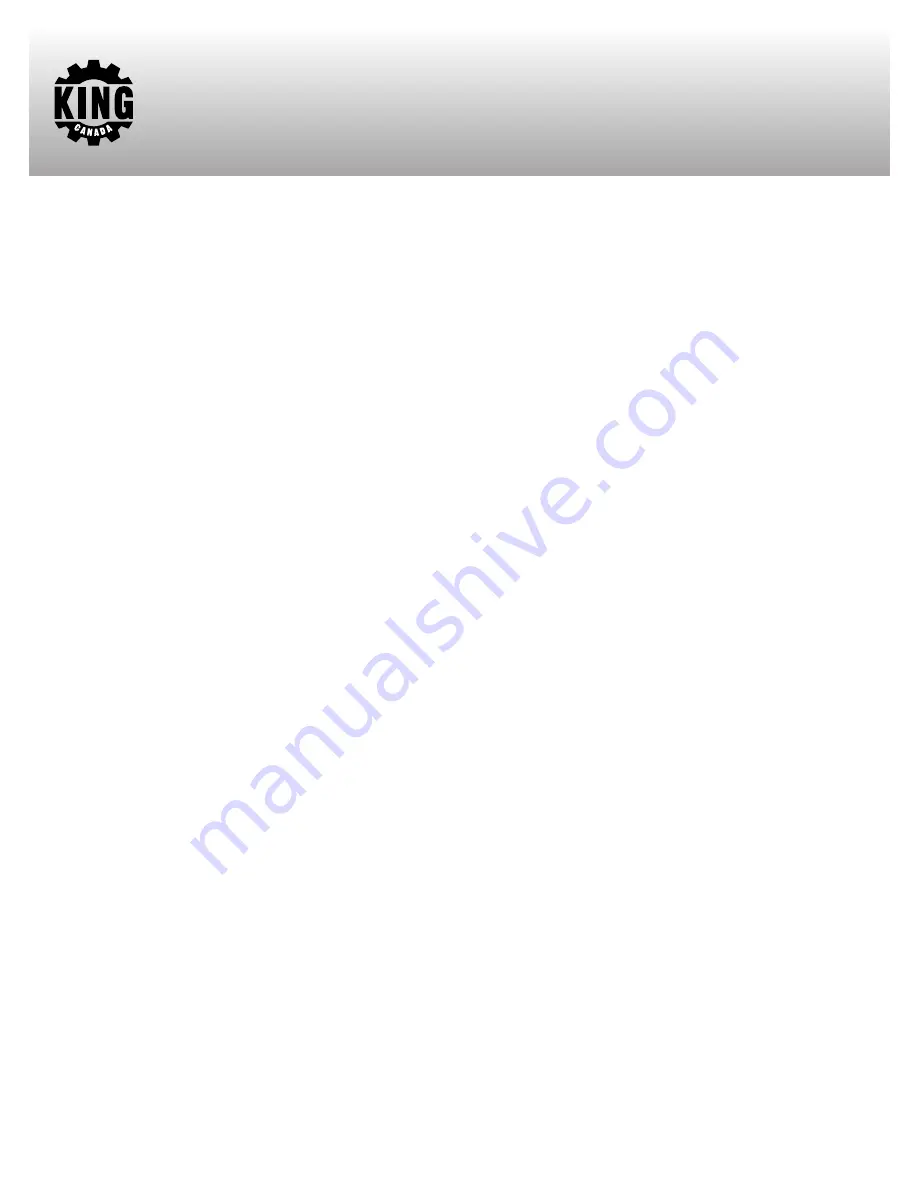
GENERAL SAFETY RULES
FOR POWER TOOLS
1. KNOW YOUR TOOL
Read and understand the owners manual and labels affixed to
the tool. Learn its application and limitations as well as its
specific potential hazards.
2. GROUND THE TOOL.
This tool is equipped with an approved 3-conductor cord and
a 3-prong grounding type plug to fit the proper grounding
type receptacle. The green conductor in the cord is the
grounding wire.
NEVER
connect the green wire to a live
terminal.
3. KEEP GUARDS IN PLACE.
Keep in good working order, properly adjusted and aligned.
4. REMOVE ADJUSTING KEYS AND WRENCHES.
Form habit of checking to see that keys and adjusting
wrenches are removed from tool before turning it on.
5. KEEP WORK AREA CLEAN.
Cluttered areas and benches invite accidents. Make sure the
floor is clean and not slippery due to wax and sawdust
build-up.
6. AVOID DANGEROUS ENVIRONMENT.
Don’t use power tools in damp or wet locations or expose
them to rain. Keep work area well lit and provide adequate
surrounding work space.
7. KEEP CHILDREN AWAY.
All visitors should be kept a safe distance from work area.
8. MAKE WORKSHOP CHILD-PROOF.
-with padlocks, master switches or by removing starter keys.
9. USE PROPER SPEED.
A tool will do a better and safer job when operated at the
proper speed.
10. USE RIGHT TOOL.
Don’t force the tool or the attachment to do a job for which it
was not designed.
11. WEAR PROPER APPAREL.
Do not wear loose clothing, gloves, neckties or jewelry (rings,
watch) because they could get caught in moving parts. Non-
slip footwear is recommended. Wear protective hair covering
to contain long hair. Roll up long sleeves above the elbows.
12. ALWAYS WEAR SAFETY GLASSES.
Always wear safety glasses (ANSI Z87.1). Everyday
eyeglasses only have impact resistant lenses, they are
NOT
safety glasses. Also use a face or dust mask if cutting operation
is dusty.
13. DON’T OVERREACH.
Keep proper footing and balance at all times.
14. MAINTAIN TOOL WITH CARE.
Keep tools sharp and clean for best and safest performance.
Follow instructions for lubricating and changing accessories.
15. DISCONNECT TOOLS.
Before servicing, when changing accessories or attachments.
16. AVOID ACCIDENTAL STARTING.
Make sure the switch is in the ‘’OFF’’ position before plugging
in.
17. USE RECOMMENDED ACCESSORIES.
Consult the manual for recommended accessories. Follow the
instructions that accompany the accessories. The use of
improper accessories may cause hazards.
18. NEVER STAND ON TOOL.
Serious injury could occur if the tool tips over. Do not store
materials such that it is necessary to stand on the tool to reach
them.
19. CHECK DAMAGED PARTS.
Before further use of the tool, a guard or other parts that are
damaged should be carefully checked to ensure that they will
operate properly and perform their intended function. Check
for alignment of moving parts, breakage of parts, mounting,
and any other conditions that may affect its operation. A guard
or other parts that are damaged should be properly repaired or
replaced.
20. NEVER LEAVE MACHINE RUNNING
UNATTENDED.
Turn power ‘’OFF’’. Don’t leave any tool running until it comes
to a complete stop.
1. TO AVOID INJURY FROM PARTS BEING THROWN
BY THE SPRING
Follow the instructions exactly as given and shown in
“Adjusting the quill return spring”.
2. USING A DRILL PRESS VISE
When using a drill press vise, always fasten it to the table.
3. NEVER DO “FREEHAND WORK”
Never do any work “Freehand” (Hand holding the workpiece
rather than supporting it on the table) except when you have
polishing to do.
4. SECURE
the lock head to the column, table support to
column and table to table support before operating the drill
press.
5. NEVER
move the head or table while the drill press is
running.
6. USE THE RECOMMENDED SPINDLE SPEED
for the
specific operation and workpiece material. Check the panel
inside the guard cover for drill information. For accessories,
use the instructions provided with the accessories.
7. NEVER
climb on the drill press table, you could break or pull
the entire drill press down on you.
SPECIFIC SAFETY RULES
FOR DRILL PRESS