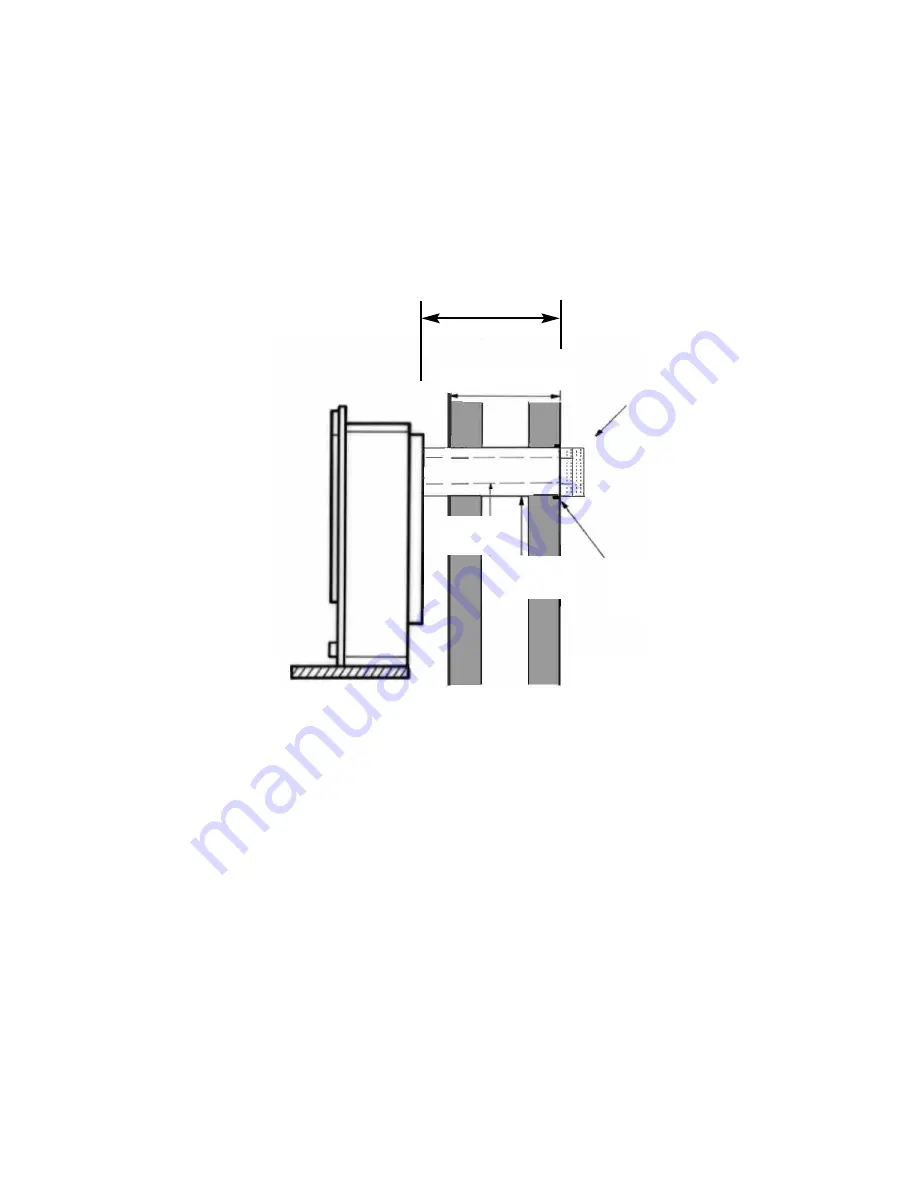
2.5
PREPARATION OF THE FLUE PIPES
a)
Place the firebox into the fire opening with the spacer (if required) fitted
and the fire surround correctly secured in the final position. From the
outside of the house measure from the face of the outside wall to the
rear panel of the firebox through the flue hole. This dimension is shown
below as
dimension A
, and cut the outer flue pipe (143mm diameter) to
Dimension “A”
Fig. 7
b)
For the inner flue pipe, (87.5mm diameter) add an additional 25mm to
dimension “A” and cut the inner flue pipe squarely to length.
IMPORTANT : DO NOT CUT FLANGED ENDS OF FLUE PIPE & ENSURE THE
PIPES ARE CUT SQUARELY.
c)
Using the screws and gaskets provided, fit both inner and outer flue
pipes to the firebox. (See Fig. 8 overpage).
d)
Using mortar or sealing compound, seal the outer flue pipe to the out
side surface of the wall, (See Fig. 7 for position of mortar).
Flue Terminal
Seal Area as indicated with
Mortar or Sealing
Compound
Wall Thickness “T”
Outer Cavity Wall
Inner Cavity Wall
Dimension ʻ“A”
Inner Flue
Pipe
Outer Flue
Pipe
10