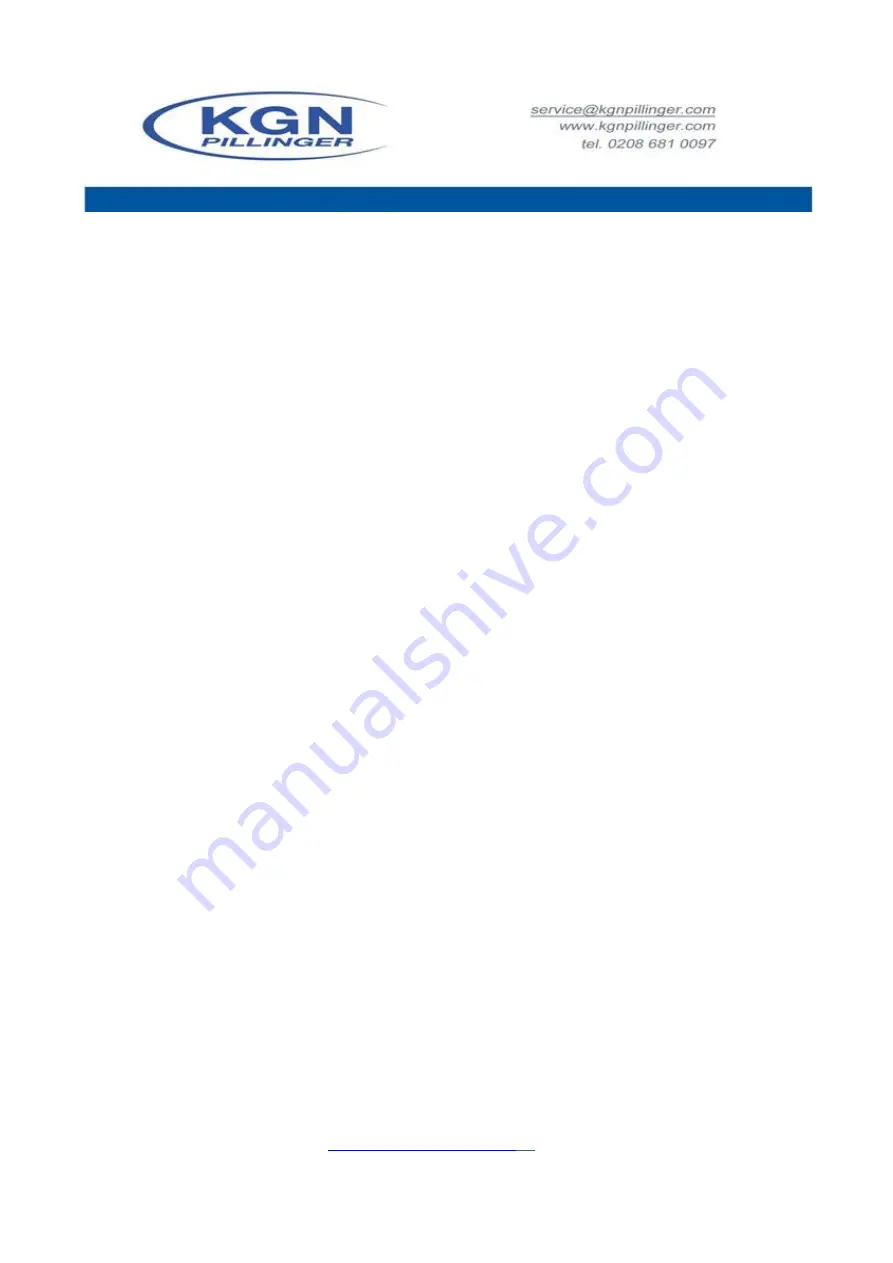
0208 681 0097
12
Operating & Maintenance
Dry Well Submersible Pump Set
Operation
–
Continued:
➢
Should the duty pump be running and the level continues to rise to the high level
float/electrode, the high level light will illuminate and the buzzer will sound. This may be
muted by pressing ‘cancel alarm’. This alarm may be reset once the level is below the high
level float switch.
Duty/Assist
These units are designed to operate from either:
1). Float switches -
‘Stop’, ‘Duty Start’, ‘Assist. Start’ and ‘High Level’.
2). Electrodes -
‘Stop’, ‘Duty Start’, ‘Assist. Start’, ‘High Level’ and ‘Common’.
➢
In manual control each pump may be run on its own by operating the respective ‘manual’
switch mounted on the door.
➢
In auto co
ntrol the pump/s will run under level control by operating both ‘auto’ switches. As
the fluid level rises the duty pump will become enabled via the relative float/electrode.
➢
If the level continues to rise the Assist Pump will become enabled via the second
float/electrode. The pump/s will continue to run until the level falls below the stop position of
the float/electrode.
➢
The pump duty is now alternated so that another pump becomes the duty unit next time they
are called to run.
➢
Should the duty pump be running and the level continues to rise to the high level
float/electrode, the high level light will illuminate and the buzzer will sound. This may be
muted by pressing ‘cancel alarm’. This alarm may be reset once the level is below the high
level float switch.
➢
Should the duty pump have stopped or failed to clear the sump water and the level has
reached the high level float/electrode, the assist pump will start and run until the level falls
below the stop float. Visual and audible indication of high level will also occur again at this
point.
➢
The remote beacon will be illuminated until the level falls below the high level float at which
point pressing ‘cancel alarm’ will extinguish the beacon.