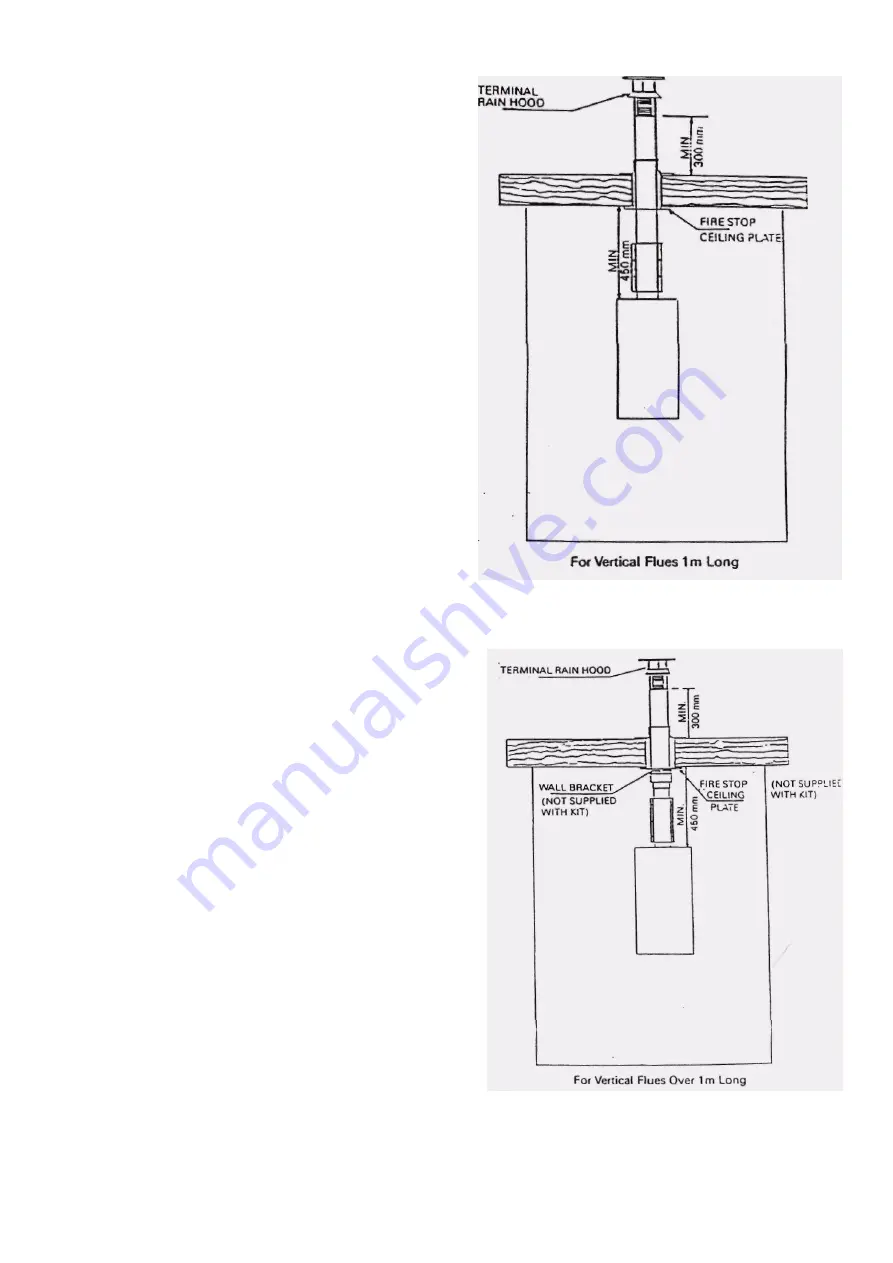
Page 16
If the flue length required falls between 1m and 1975 mm.
reduce the 910 mm length of 110 mm air pipe by the
required amount and remove the same amount from the
plain end of the inner flue pipe.
If the flue length required falls between 1975mm and
2975mm. reduce the 191O mm length of 110mm air pipe
by the required amount and remove the same amount from
the plain end of the inner flue pipe.
NB: The minimum height of a vertical flue is 1 metre.
f Measure a distance of 113 mm from the face of the wall to
the centre of the flue position and drill a hole of 130 mm
diameter through the ceiling or roof above the boiler to
receive the 100 mm diameter pipe or a hole of 145 mm
diameter to receive the 110 mm diameter pipe.
N6: If the ceiling is of a combustible material use a Ceiling
Fire Stop Plate in accordance with the manu- facturers
instruction.
g Wall mount the boiler in accordance with the paras 4.3 to
4.6. leaving a minimum distance of 450 mm above the
boiler.
h Fit the flue and air pipe extension pieces to the flue and
air connections on the top of the Boiler i If the extended
vertical flue kit is not being used continue the procedure
from step q of these Installation Steps.
For extended vertical flues only, (for tm vertical flues skip
steps j to p):
j Fix the wall bracket in the correct position to support the
flue assembly when in place. (See Fig 4.6)
k Separate the flue pipe with the terminal from the 1 metre
length of 1OO mm diameter air pipe.
I Fit the spring clips at equal intervals onto the metre length
flue pipes from the Extended Vertical Flue Kit. m Fit the110
mm x 100 mm reducing adaptor to the plain end of the
metre length of 100 mm diameter air pipe so that the air
pipe contacts the stop pins in the reducing adaptor Use the
reducing adaptor as a template to pre-drill 2 mm diameter
holes and secure using the screws provided.
n Fully engage the 110 mm air pipe to the 110 mm x 100
mm reducing adapter. Again use the reducing adaptor as a
template to pre-drill 2 mm diameter holes and secure using
the screws provided to Fit the flue pipe with terminal to the
remaining Section(s) of flue pipe to form a complete length
of flue pipe. Use the pre-drilled holes as a template to drill
2 mm diameter holes and secure all connection with the
screws provided
p Push the assembled flue pipe through the assem-bled air
pipe so that the terminal is just clear of the air pipe as
shown in Figs 4 8 & 4 9 For 1m and extended vertical flues.
q Slacken off the screws on the detachable flue pipe sleeve
and slide over the end of the flue pipe extension piece
attached to the outer (See fig 4 8)
r Lousely assemble the 110 mm long by 60 mm diameter
distance piece into the open end of the detachable flue
pipe sleeve (See Fig 3)
Summary of Contents for Thermomatic RSM20/FB
Page 2: ...Page 2...
Page 12: ...Page 12...
Page 17: ...Page 17...
Page 33: ...Page 33...
Page 37: ...Page 37 Complete boiler wiring schematic...
Page 39: ...Page 39 Examples of standard wiring connections to most popular models...
Page 40: ...Page 40...
Page 45: ......
Page 46: ......