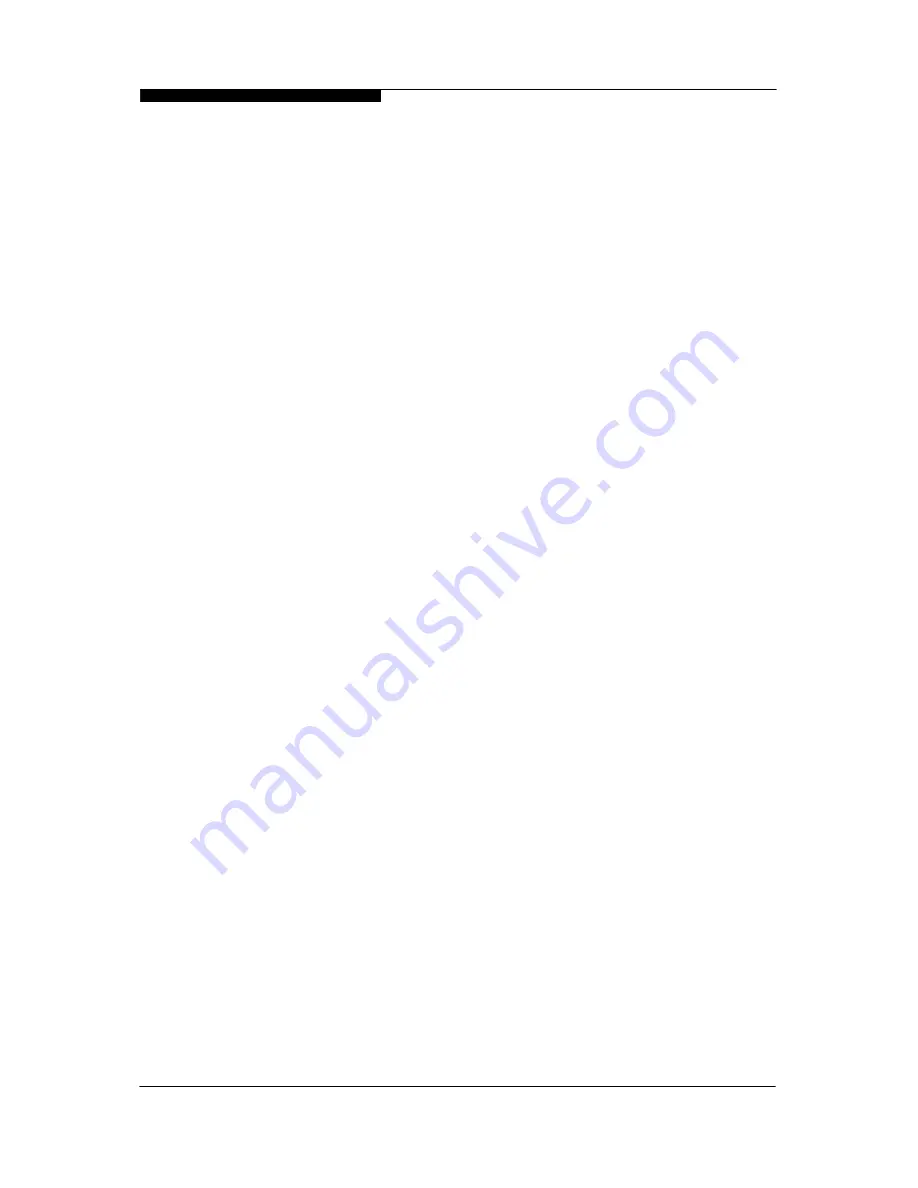
a)
Have the wall bracket nuts and washers to hand so that they can be accessed whilst
holding the boiler in position on its mounting bracket.
b)
The boiler has a dry weight of 41 kg (91 lbs) and will therefore require at least two people
to lift without the use of lifting aids - ensure co-ordinated movements during lift. Always
use assistance if required.
c)
Lift the boiler by gripping at the four corners of the boiler back plate. When lifting this
appliance the back should be kept straight at all times. Avoid twisting at the waist -
reposition the feet instead. Avoid upper body bending when holding the appliance and
keep the boiler as close to the body as possible.
d)
Lift the boiler and locate onto the two studs of the wall mounting bracket.
e)
Place the wall mounting bracket washers over the bracket stud protruding through the
back plate of the boiler.
f)
Secure the boiler onto the wall bracket by fixing the wall mounting bracket nuts onto the
wall bracket studs. This must be tightened well.
Safety footwear and gloves are recommended PPE when lifting this appliance - to protect
against sharp edges and ensure good grip.
The Q37 and Q37P boilers can be fitted in compartments with very small clearances required
around the appliance (refer to Section 3.1). Due consideration should therefore be given to
access within the compartment for lifting and positioning.
WD500
The Keston Q37 & Q37P Boilers
Page : iv