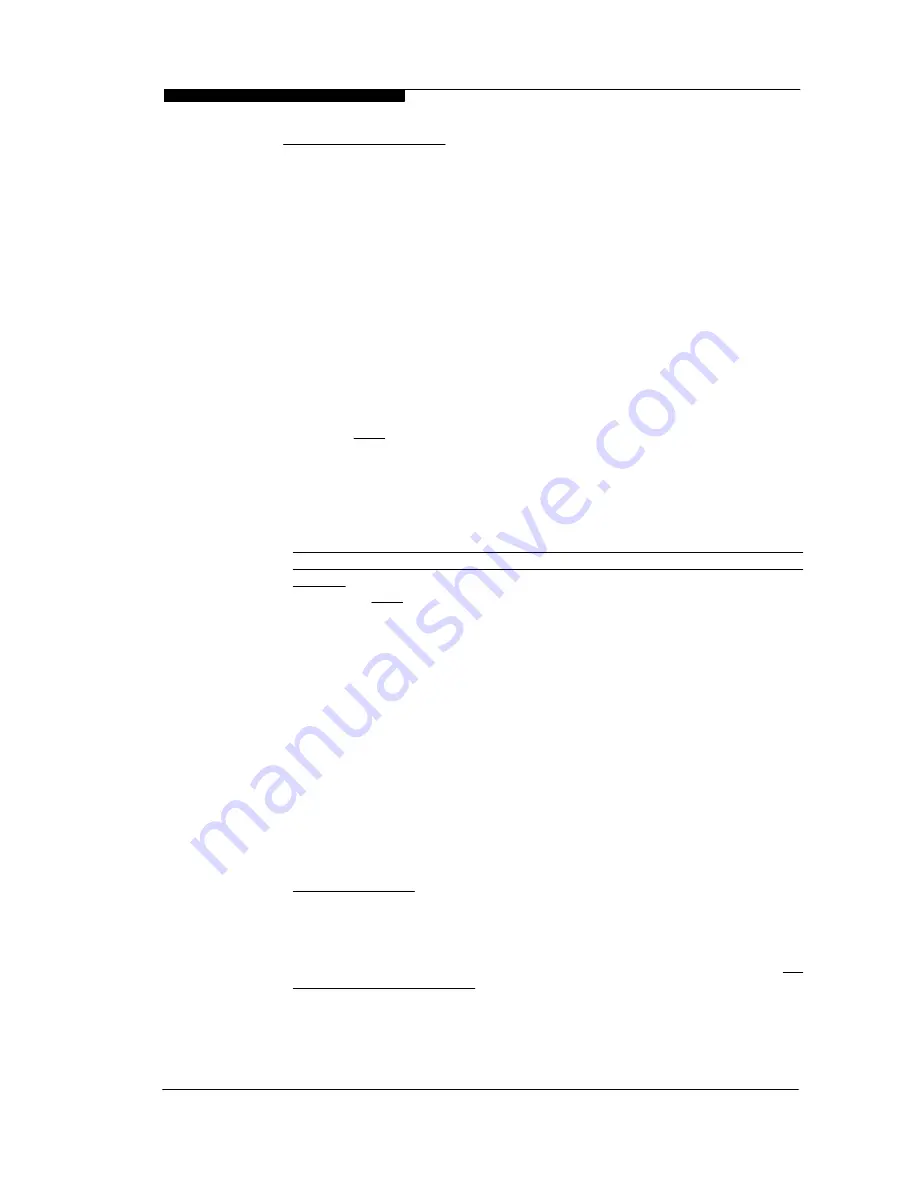
LPG pressure must be maintained between 31.5 mbar (12.4 in w.g) and 37.6 mbar (14.8
in w.g) while the boiler is running.
Gas pressures above or below these levels will lead to problems associated with the gas
valve's internal pressure regulator.
Supply pipes to the boiler must not be sized less than the boiler inlet connection
(22mm). Due consideration must be given to the supply pressure to other gas
appliances in the premises. Reduction in dynamic gas supply pressure will result in
intermittent ignition failures. Ensure gas supply pipe work is adequately sized for
the length of run from the meter to the boiler at a supply rate of 38kW (i.e. a natural
gas supply should be considered to be a minimum of 22mm diameter. If gas runs greater
than 14m, including the allowance for bends, are involved the pipe size should be
increased further).
3.7
WATER SYSTEMS
All piping must be installed in accordance with all applicable local and Water Supply
Bylaws for forced hot water heating systems.
Consideration must be given to pipe capabilities and pressure drop through the piping
when selecting pipe sizes. The primary pipe connections to the boiler must be sized
according to the system load, not dictated by the boiler connection sizes.
Water treatment must be carried out to BS 7593 : Treatment of Water in Hot Water
Central Heating Systems.
In IE the requirements given in the current edition of IS813 and the current Building
Regulations must be followed.
a
The Q37 is suitable for use on open, vented water systems with combined feed
and vent fitted to the boiler return.
b
It is preferable for use on sealed water systems, provided the appropriate
components required (see Section 3.7.2 Sealed Systems) are included in the
system.
c
Any system must be thoroughly flushed clean of grease, dirt and debris, prior to
connection with the boiler. A trap may be installed in the flow line to collect any
solder, or other debris, from the installation.
d
All water systems must be constructed to comply with requirements of the Local
Water Authority.
e
Always use a system complying with the requirements of BS 5449 and BS 6798.
f
System design must ensure an open circuit is always available to ensure
circulation when the pump overrun function is operating after boiler shutdown.
f
Isolation valves must be fitted on the flow and the return to enable isolation when
maintaining the boiler.
g
Copper tubing to BS 2871 Part 1 or barrier plastic pipe suitable to 110
o
C, such as
Unipipe, is recommended.
h
Jointing should be either with capillary, threaded or compression fittings. Pipes
should have a gradient to ensure air is passed easily to vent points and water
flows readily to drain points.
i
Draining taps must be located in accessible positions which permit the draining of
the boiler and hot water storage vessel. Draining taps should be at least 22 mm in
nominal size and be in accordance with BS 2879.
AIR VENT POINTS
j
These must be fitted at all high points where air will naturally collect and must be
sited to allow complete draining of the system.
k.
Where thermal stores are to be used the thermal store supplier should be
consulted as to the compatibility of the thermal store with a Keston Q37. Thermal
store units where the boiler directly heats an open vented thermal store are not
suitable for use with the Q37.
3.7.1
Open Vented Systems
A typical system is shown in Figure 3.7.1 which includes a combined feed and
vent. Note that the combined feed and vent must be fitted to the primary
WD500
Chapter 3 - Boiler Location
The Keston Q37 & Q37P Boilers
Installation & Servicing Instructions
Page : 13