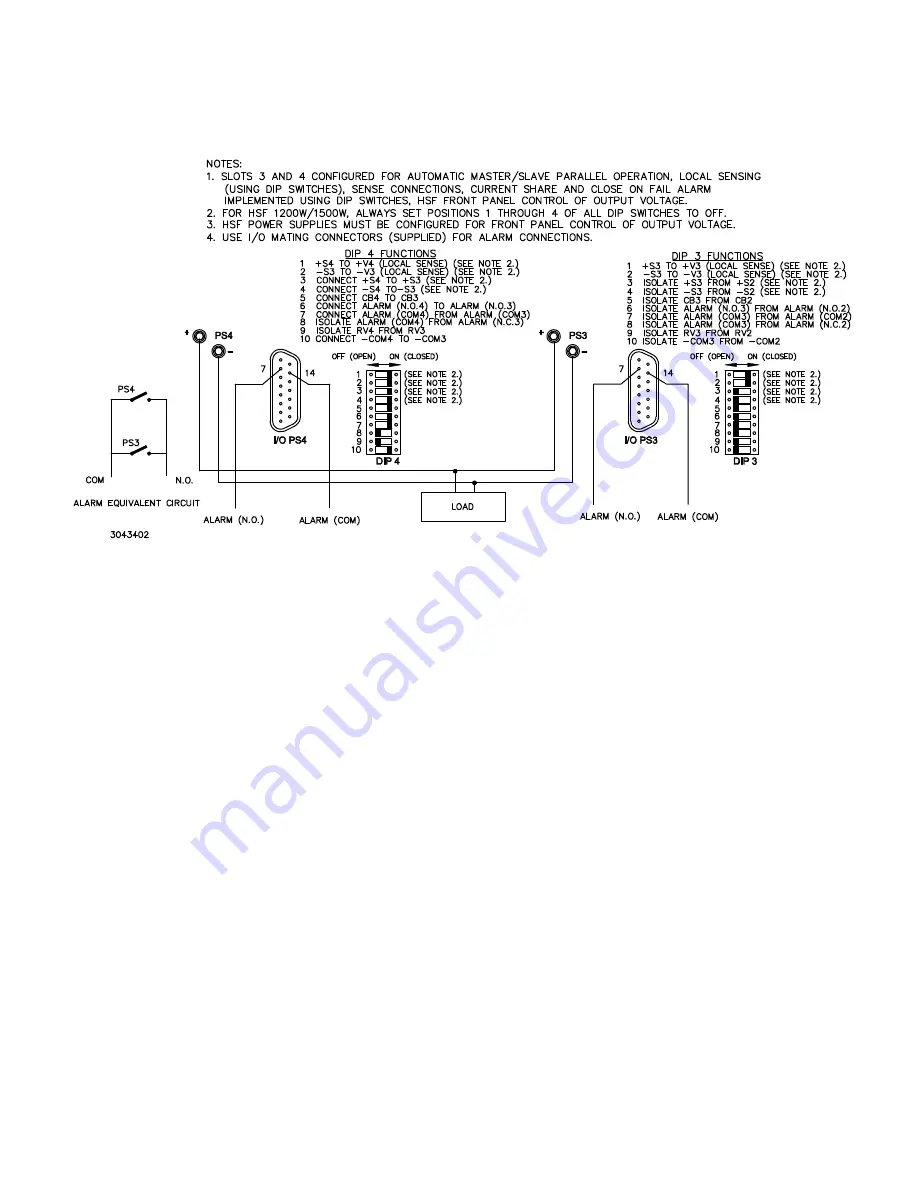
4
228-1671 REV 2
110122
KEPCO, INC.
131-38 SANFORD AVENUE
FLUSHING, NY. 11355 U.S.A.
TEL (718) 461-7000
FAX (718) 767-1102
http://www.kepcopower.com
email: [email protected]
the power supplies secure under severe shock or vibra-
tion conditions.
FIGURE 3. SLOTS 3 AND 4 CONFIGURED FOR PARALLEL OPERATION, WITH CLOSE ON FAIL ALARM CIRCUIT
IV — WIRING
A-C WIRING:
It is the user’s responsibility to obey all
local, national and international safety rules regarding
field-wired apparatus and the grounding of the metal
cover and case of any instrument connected to the a-c
power source. Grounding is an intrinsic part of the safety
aspect of the unit.
SOURCE POWER:
Source power requirements are
determined by the HSF power supply (see HSF power
supply Instruction Manual); no adjustment or modification
of the rack adapter is required.
Source power can also be custom configured via jumpers
on the internal PC board. Contact Kepco Applications
Engineering for further details.
Wire size range for each terminal block is AWG 20-10/
IEC, rigid: 0.5 - 6mm2, or flexible (stranded): 0.5 - 4mm2;
torque to 6 lb-in (0.6 N•M) maximum.
CAUTION: DO NOT
EXCEED MAXIMUM TERMINAL BLOCK RATING OF
500V AT 36A.
The terminals are labeled L, N, and G.
Their functions are:
• Terminal G (Ground) is the safety ground con-
nection for the RA 19-4C.
• Terminals L (Line Phase) and N (Neutral) are
connected to the input power entry connectors.
Source power is provided to the power supplies
indicated by the label on the rear panel.
CONTROL SIGNALS:
Access to all the control sig-
nals for each HSF power supply is provided via four 15-
pin D-subminiature I/O connectors on the rear panel of the
rack adapter (see Figure 1). Four mating connectors
(Kepco P/N 142-0449) are provided in a plastic bag. Basic
functions (Sense and Alarm) are also available via the 5-
pin ALARM I/O Euroheader.
OUTPUT LOAD:
Load connections to the rack adapt-
ers are achieved via four pairs (DC and –) of
output terminals located on the rear panel assembly. Wire
gage may be between 22 GA and 6 GA depending on ring
lug used; torque to 20 lb-in (2.3 N•M) maximum. As the
length of load wires increases, ripple and noise may
increase proportionally, therefore length and placement
are critical for minimum ripple and noise. A filter consisting
of a 50mF electrolytic capacitor in parallel with a 0.01mF
capacitor must be used to eliminate unwanted ripple and
noise pickup on the load wire during measurements. For
noise-sensitive applications the load wires and sense
wires must be twisted and/or shielded.