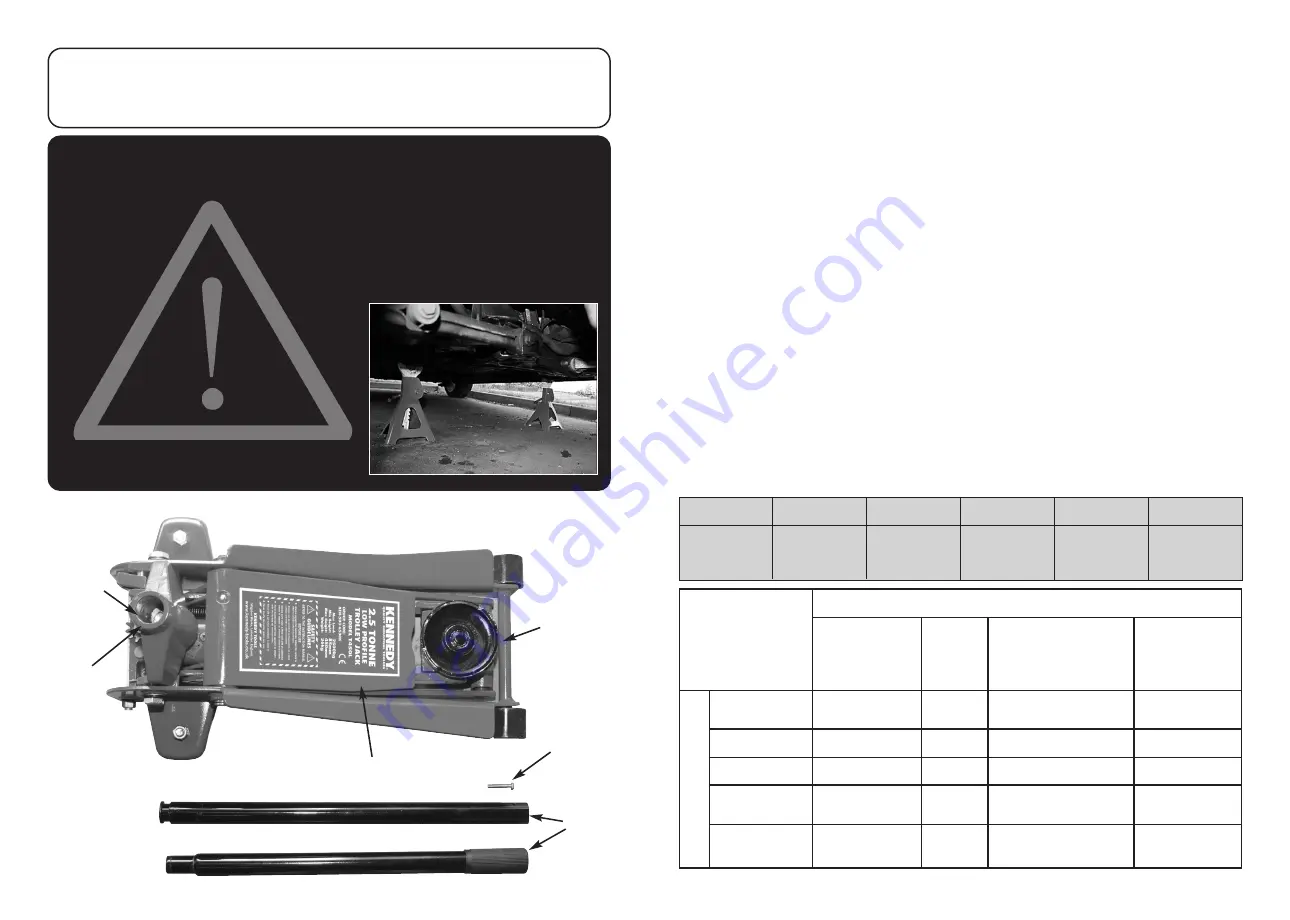
2
3
IDENTIFICATION
Saddle
Release
Valve
KENNEDY
Trolley Jacks are designed to help you work safely and efficiently.
Lifting equipment can be dangerous if the correct operating and maintenance
procedures are not followed. Operating instructions and basic safety procedures are
as follows:
SAFETY GUIDELINES
l
Always use on specified jacking points, on a level surface and with a solid
foundation.
l
Before use inspect the Garage Jack for abnormal conditions such as cracked
welds, damage, worn, loose or missing parts. Also check that the jacking
points are not corroded before use.
l
Always place chocking wedges either side of the wheels and engage the
handbrake before the vehicle is lifted to
prevent wheel movement.
l
Always use correctly rated axle stands as
an additional means of support when work
under a lifted load.
l
Never exceed the rated load capacity or
tamper with the factory set overload valve.
l
Never lean against the raised vehicle.
l
Never modify the jack, it is not designed to
support extensions or cradles and could
become unsafe.
OPERATING INSTRUCTIONS
ASSEMBLY
1.
Remove the wire clip securing the handle socket.
2.
Using the hexagonal bolt provided secure and fasten the
two pump handle poles together.
3.
Place the completed pump handle into the handle socket
and tightly secure.
OPERATE
Bleed the hydraulic system of air before using the
jack for the first time (see bleeding the system).
1.
To engage piston pressure, turn the pump handle
clockwise.
2.
Position the Jack under the vehicle so that the lifting
saddle will be centred on a specified jacking point.
3.
Pump the handle to raise the load.
4.
Once the load has been raised to the required height, use
an additional support (i.e. correctly rated stands) before
continuing work.
5.
To lower the vehicle, remove the additional supports.
Turn the pump handle counterclockwise, this will turn the
release valve. The speed at which the vehicle is lowered
can be controlled by how quickly the release valve is
turned.
MAINTENANCE
We recommend that maintenance is carried out on the
Trolley Jack on a monthly basis to keep it operational.
1.
Lubricate the ram, linkages, saddle and pump mechanism
with light oil.
2.
Clean all surfaces and maintain all labels and warnings.
3.
Check and maintain the ram oil level.
4.
Check the ram every 3 months for any sign of rust or
corrosion. Clean as needed and wipe with an oiled cloth.
When not in use always keep the saddle and ram in the
fully lowered position.
5.
Visually inspect for cracked welds, damaged, loose,
missing parts or hydraulic oil leaks.
6.
You should always inspect the Trolley Jack immediately if
it has been subjected to abnormal load or shock.
If the Trolley Jack is found to have been damage in any way,
worn or operates abnormally in any way it should be removed
from service until repaired by an authorized person.
Owners and operators should be aware that repair of this
product may require specialized equipment.
Do not use brake or transmission fluids or regular motor oil as
they can damage the seals. Always use a medium grade
Hydraulic Oil.
REFILLING OIL RESERVOIR
1.
Turn the release valve counterclockwise to allow the ram
to fully retract.
2.
With the jack in the level position, remove the rubber oil
fill plug. Stand the jack in a vertical position with the
handle socket down. The oil should be level with the
bottom of the fill hole. If not add more clean hydraulic jack
oil until level with the bottom of the fill hole.
3.
Replace rubber oil fill plug.
4.
Check that the Trolley Jack is fully operational and bleed
air from system as required.
BLEEDING THE SYSTEM
1.
Turn the release valve counterclockwise no more than one
complete turn.
2.
Remove the rubber oil fill plug.
3.
Pump the handle several times to force out any air.
4.
Turn the release valve clockwise until it can no longer be
turned.
5.
Replace the rubber oil fill plug.
STORAGE
Always store your jack in the fully lowered position. This will
help protect critical areas from corrosion.
The release valve has
not been fully closed.
Turn the release
valve clockwise until
it can no longer be
turned.
The oil level
is low.
See refilling
instructions.
The hydraulic system has
become blocked by dirt
particles. Manually pull the
piston up. Turn the release
valve anti-clockwise and push
the piston down quickly.
Air has entered the
hydraulics. See
bleeding the hydraulic
system instructions.
The hydraulic
system will not fully
extend.
The jack will not lift
the rated load.
The jack lowers
under load.
The hydraulic
system will
not lower.
The handle
raises or springs
back under load
.
l
l
l
l
l
l
l
l
l
C
O
M
M
O
N
F
A
U
LT
S
FAULT
FINDER
SOLUTIONS
Model
Max Load
Min Height
Max Height
Weight
Order Code
Number
(Kg/Tonne)
(mm)
(mm)
(Kg)
KEN-503
T359L
2,000/2
89
359
14.5
-6520K
T450L
2,500/2.5
85
450
36
-6530K
T510L
2,000/2
76
510
42
-6570K
T525L
3,000/3
140
525
50
-6580K
CAPACITIES
Pump
Handle
Handle
Socket
Ram
Hexagonal
Bolt