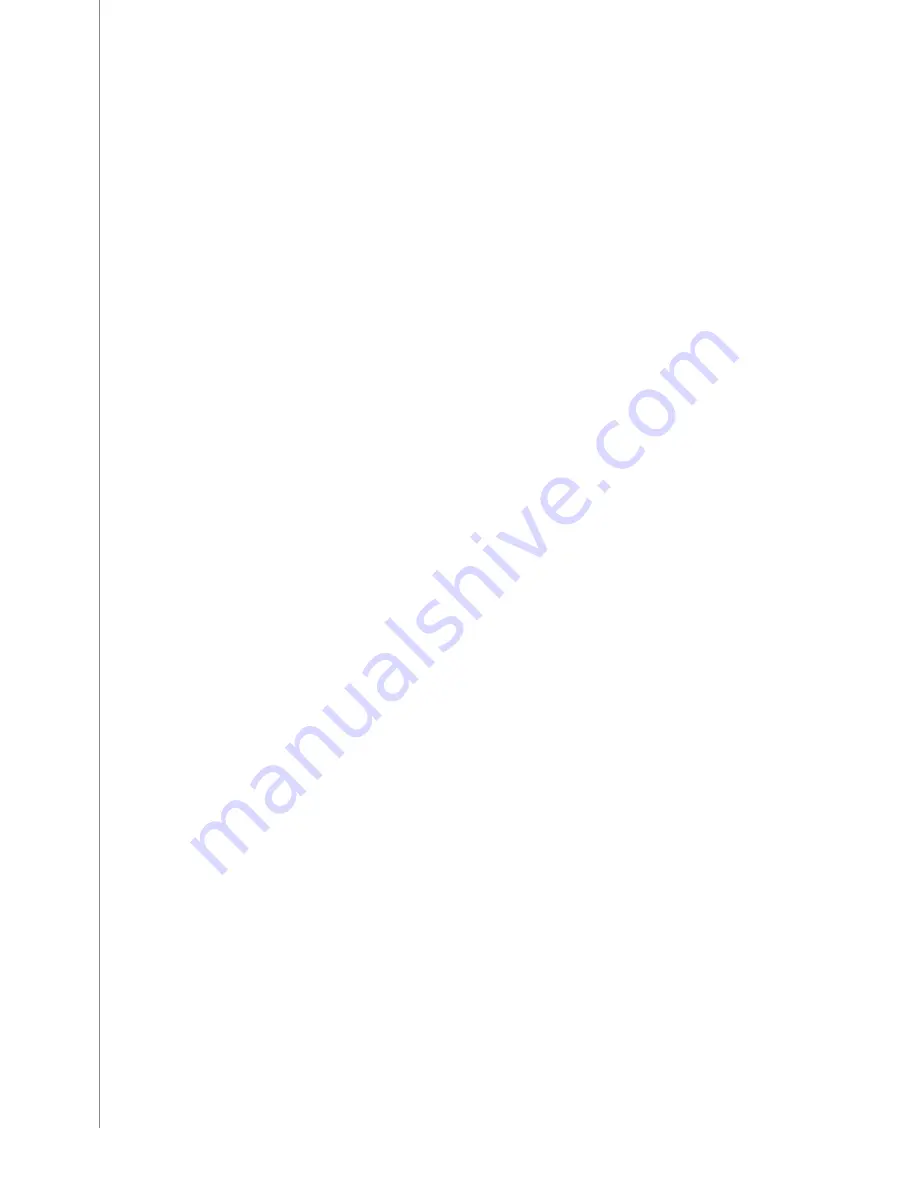
EN
Minilog
When torch switch is pressed gas flow starts. When you release the torch switch current goes
to Search Arc. By pressing shortly the switch current goes through upslope to Hot Start or Soft
Start current depending on adjustments and by pressing shortly again to welding current.
After next short press it goes to Minilog current, and you can select from two current levels:
the welding current and the Minilog current. You can move from one to the other by quickly
pressing the torch switch. Press the torch switch for one second, release it and current goes to
downslope and the arc is cut.
4T-lOg
When torch switch is pressed current goes to search arc; after the switch is released current
goes to welding current within the upslope time. When the switch is pressed again, current
goes to downslope and then to the tail arc. Current stops when the switch is released.
synergic quick pulse (sYnergiC)
Press the PULSE button (6) until the synergic light turns on. Pulse parameters are adjusted
automatically when average welding current is selected. Other pulse selections are not
necessary.
long pulse (pulse)
Long pulse method (button 6/PULSE) gives you the possibility to adjust all pulse parameters
(pulsing frequency, pulse ratio, pulse current and pause current). You can also adjust the
welding current, in which case you receive a new pulse current value. Pulse ratio and pause
current percentage remain constant. When you adjust the pulse current the new average
welding current value is shown on the display.
spot welding function (spOT)
The function (button 6/SPOT) can be used both in 2T and 4T mode. Enter the spot duration
by pressing arrow button, and when the led is lit you can choose the spot time needed by
turning the pulse control knob.
Tig -Micro tack welding function (MicroTack™)
You can select the MicroTack function with a long press of the MicroTack arrow button (6) and
MicroTack light turns on, the machine automatically enables the DC- welding mode, 2T switch
mode and contact ignition. This function can also be used with HF ignition, 4T mode and on
AC welding. To inactivate the MicroTack you press briefly the same arrow button (6).
The duration of the spot weld (SPt) can be adjusted by pressing Quick Setup button and
selecting a value in the range 1–200 ms. Also on AC welding the amount of spots (Pco) can be
adjusted between 1 – 5.
The spot current can normally be adjusted with the control knob when the welding current
led is on.
MicroTack adjustments can be saved to memory channel according the next advise.
3.2.3 saving welding settings
ACX panel has 10 memory channels for user settings. The selections are made in the MEMORY
field. Not only welding parameters but also function selections can be saved in the memory.
MMA welding values can also be stored in memory channels. Proceed as follows:
1.
Press MEMORY button and if the SET light starts blinking the channel is free. If a channel is in
use, the ON light will light up. Press again, and the SET light will be continuously lit.
2.
Select memory channel by pressing CH button.
3.
Select the parameters and press SAVE button.
4.
Press MEMORY button twice. ON led is lit.
5.
Start welding.
If the saved settings need to be adjusted the led has to be moved from ON to SET position in
order to select parameters. Press the SAVE button.
When the memory function is in OFF state (no lights on) it is also possible to save the currently
used panel parameters by pressing SET/SAVE, by choosing channel ja by pressing SET/SAVE
again. Channel is cleared if MEMORY and CH buttons are pressed simultaneously in SET mode.
16
M
ast
er
Tig MLS 3000, 3003 A
CDC / © Kemppi O
y / 1112