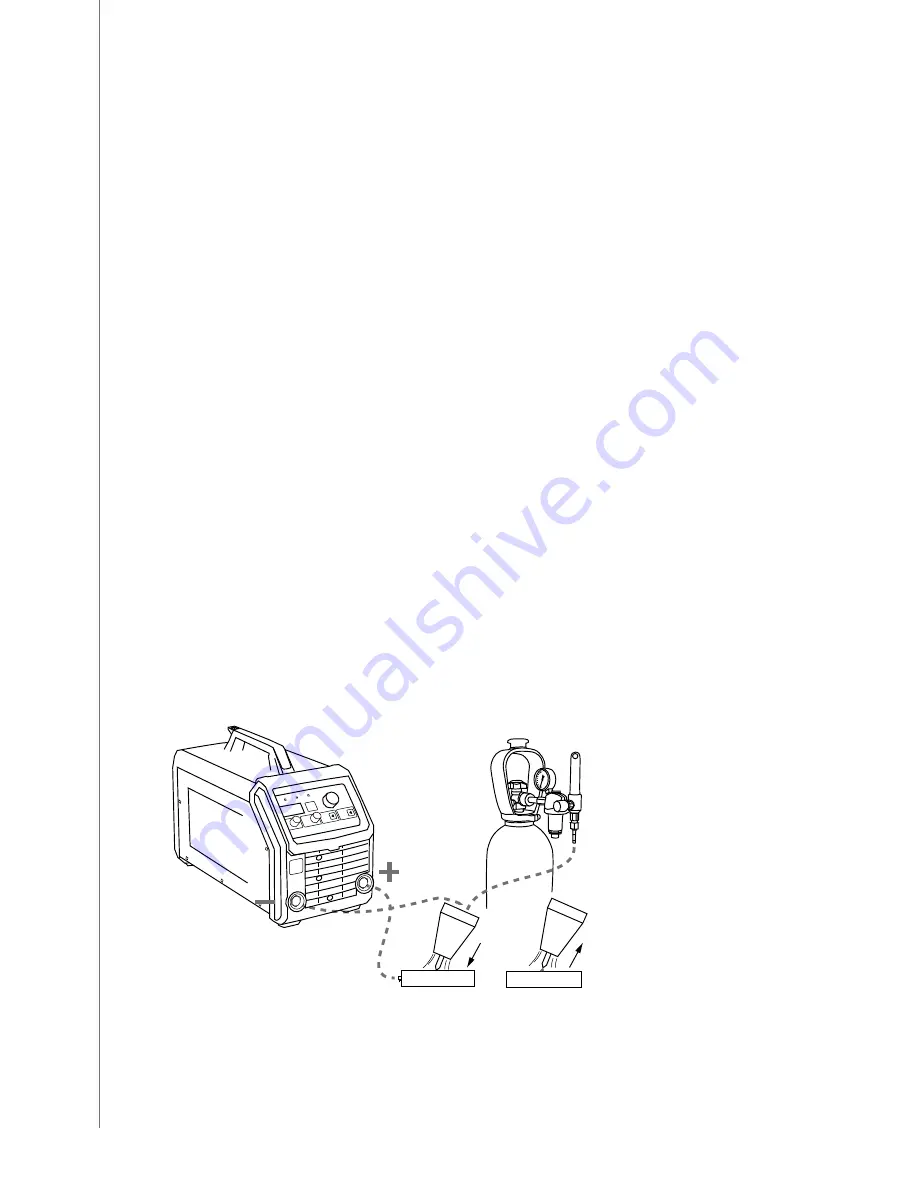
HiArc S 400R, 400A
12
EN
3.4 tig welding
TIG welding is possible only with HiArc S 400A model, not with the R model.
NOTE!
In TIG welding the welding cable must be connected to the negative (-) pole connection
socket and the earth return cable to the positive (+) pole connection socket.
Select your required welding parameters according to the manufacturer’s filler material
recommendations and the joint to be welded.
1.
Select the required polarity of welding current cable (-) and earth return cable (+) for TIG
welding.
2.
Select TIG welding mode by pressing the process selection button on the control panel.
3.
Select a suitable welding current by adjusting the current adjustment knob.
4.
Make a small test weld to check the selections made.
Shielding gas is used in DC TIG welding. Your dealer will give you advice on choosing gas and
equipment.
You can start welding after having made the necessary selections. Open the gas valve on the
TTM 15 V BC. When gas starts to flow, arc is lit by lightly scratching work piece with the tip of
the tungsten electrode, or with the touch and lift method (see 'Ignition by Lift TIG'). When arc
is lit, its length is regulated by holding the tip of the tungsten electrode at a suitable distance
from the work piece. Suitable arc length is usually about half the diameter of the electrode
core wire. Move the torch forwards from the starting point. If necessary, adjust current value.
The filler material, tungsten electrode and the welding current level are decided according to
the base material type and thickness, joint form and welding position.
Stop welding by lifting the torch off the welding piece and by closing the gas valve on the
torch.
NOTE!
The torch voltage will remain on.
NOTE!
Always fix the gas cylinder so that it stays steadily in upright position either in specially
made wall rack or cylinder trolley. Always close the cylinder valve after having finished welding.
ignition by lift tig
You can ignite TIG arc with the Lift TIG method. Gently touch the work piece with the
electrode and quickly lift the electrode from the work piece to a suitable welding distance to
ignite the arc. If electrode contact with the work piece exceeds 1 second, the power source
ignition will automatically shut off preventing damage to the electrode.
To stop welding, quickly pull the electrode away from the work piece.
< 1.0 s
Order information for the additional equipment (TIG torch) required for TIG welding can be
found in 'Ordering codes' section later in this manual.