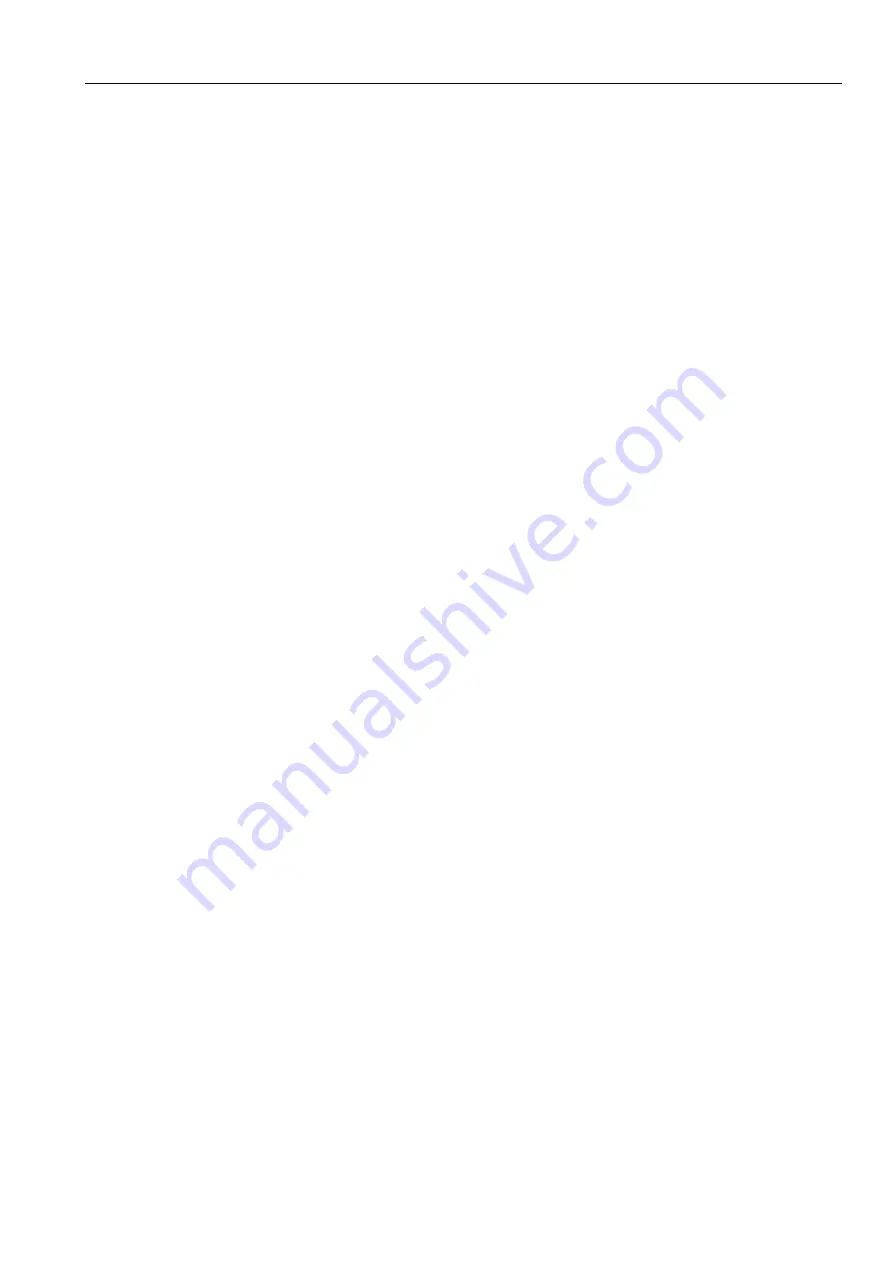
Kelly KLS-S Brushless Motor Controller User’s Manual
V1.5.02
23
from 5V to 0V.
Suggestion:factory default is Disable.
Note: Thermistor is optional. Default to KTY84-130 or 150
Chapter 5 Maintenance
There are no user-serviceable parts inside the controllers. Do not attempt to open the
controller as this will void your warranty. However, periodic, exterior cleaning of the controller
should be carried out.
The controller is a high powered device. When working with any battery powered vehicle,
proper safety precautions should be taken that include, but are not limited to, proper training,
wearing eye protection, avoidance of loose clothing, hair and jewelry. Always use insulated
tools.
5.1 Cleaning
Although the controller requires virtually no maintenance after properly installation, the following
minor maintenance is recommended in certain applications.
•
Remove power by disconnecting the battery, starting with battery positive.
•
Discharge the capacitors in the controller by connecting a load (such as a contactor coil,
resistor or a horn) across the controller’s B+ and B- terminals.
•
Remove any dirt or corrosion from the bus bar area. The controller should be wiped with a
moist rag. Make sure that the controller is dry before reconnecting the battery.
•
Make sure the connections to the bus bars, if fitted are tight. To avoid physically stressing
the bus bars use two, well-insulated wrenches.
5.2 Configuration
You can configure the controller with a host computer through either an RS232 or USB port.
•
Disconnect motor wiring from controller for configuring existing parameters in the user
program or Android APP. If this operation is too much extra job for you, please make sure
the motor must be stopped before programming.
•
The controller may display fault code, but it doesn't affect programming or
configuration.But it will affect the Identification angle operation.Please try to eliminate the
error codes before Identification angle operation.
•
Use a straight through RS232 cable or USB converter provided by Kelly to connect to a
host computer. Provide >+18V to PWR
(
for a 24V controller, provide >+8V
)
. Wire power
supply return(supply negative) to any RTN pin.