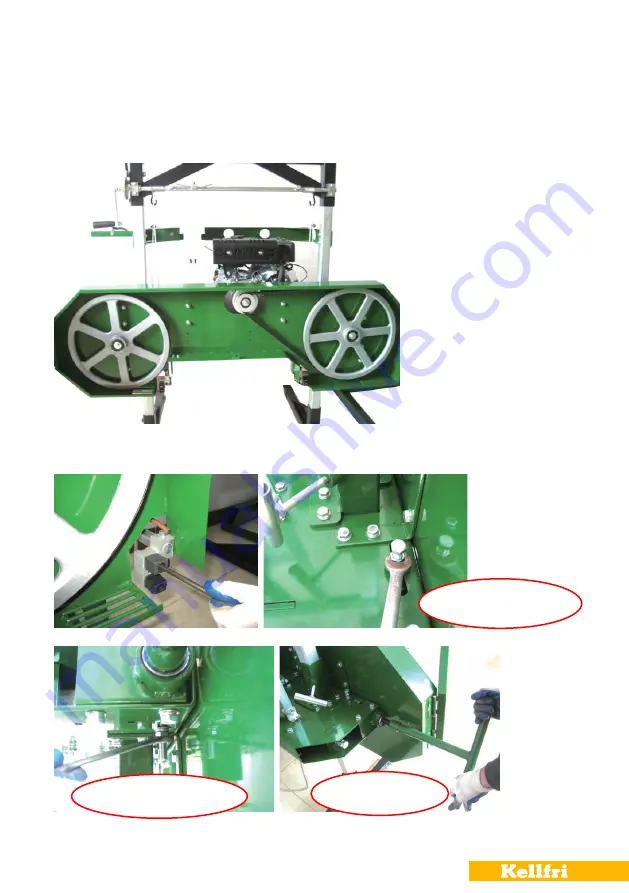
27
INSTALLATION AND ADJUSTMENT OF SAW BLADE
Instructions below must never be performed when the engine is running. For safety, remove
the spark plug cap. Gloves and eye protection is recommended to use when working with the
band saw.
1.) Loosen the 3 bolts with the 13 mm wrench and remove the protective cover.
2.) Loosen hex screw (# 91) on the blade guide blocks (# 90) on both the left and right side.
Loosen the upper and lower mounting bolts and release the clamping bolt (# 1). Move the
adjustment bolt forward for easier mounting of band saw.
mounting bolt- top
mounting bolt - bottom
Tighten bolt
1
2
3
4