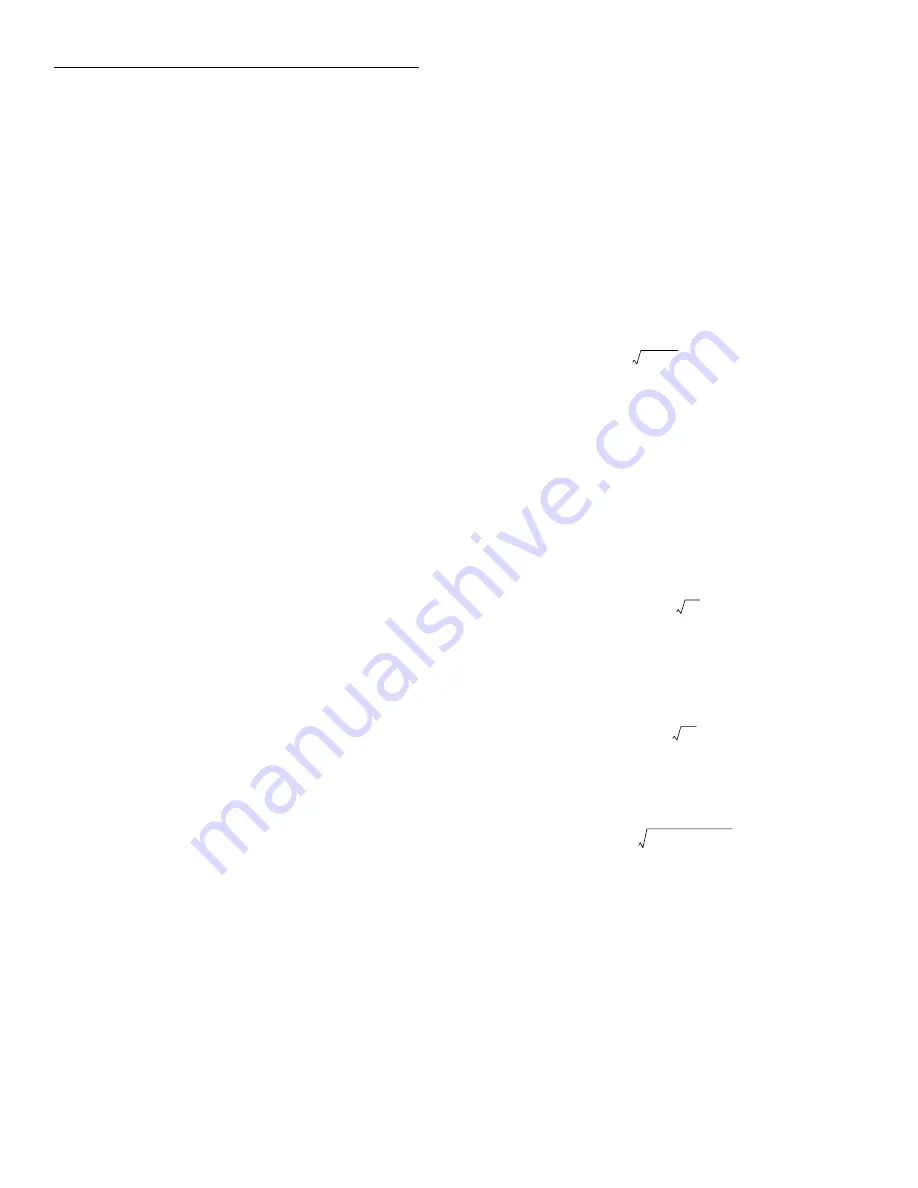
Operation
3-20
Minimizing thermal EMFs
To minimize thermal EMFs, use only copper wires, lugs,
and test leads for the entire test setup. Also, it is impera-
tive that all connecting surfaces are kept clean and free of
oxides. As noted in Table 3-2, copper-to-copper oxide
junctions can result in thermal EMFs as high as 1mV/°C.
Even when low-thermal cables and connections are used,
thermal EMFs can still be a problem in some cases. It is
especially important to keep the two materials forming
the junction at the same temperature. Keeping the two
junctions close together is one way to minimize such ther-
mal problems. Also, keep all junctions away from air cur-
rents; in some cases, it may be necessary to thermally
insulate sensitive junctions to minimize temperature vari-
ations. Always operate the preamplifier module in the
thermal isolation enclosure to minimize the effects of air
currents.
In some cases, connecting the two thermal junctions
together with good thermal contact to a common heat sink
may be required. Unfortunately, most good electrical
insulators are poor conductors of heat. In cases where
such low thermal conductivity may be a problem, special
insulators that combine high electrical insulating proper-
ties with high thermal conductivity may be used. Some
examples of these materials include: hard anodized alumi-
num, beryllium oxide, specially filled epoxy resin, sap-
phire, and diamond.
Nulling residual thermal offsets
Even if all reasonable precautions are taken, some resid-
ual thermal offsets may still be present. These offsets can
be minimized by using the Model 2001 relative feature to
null them out. To do so, place the instrument on the range
to be used for the measurement, and short the end of the
connecting cable nearest the measured source (first dis-
connect the cable from the source to avoid shorting out the
source). After allowing the reading to settle, press the
front panel REL button to null the offset, then make your
measurement as usual. Note that it may be necessary to re-
zero often to counteract preamplifier or thermal drifts, and
the rel process should be repeated whenever the range is
changed for best accuracy.
3.4.2 Source resistance noise
Noise present in the source resistance can be the limiting
factor in the ultimate resolution and accuracy of Model
1801 measurements. The paragraphs below discuss the
generation of Johnson noise as well as ways to minimize
such noise.
Johnson noise equation
The amount of noise voltage present in a given resistance
is defined by the Johnson noise equation as follows:
Where: E
RMS
= RMS value of the noise voltage
k = Boltzmann’s constant (1.38
×
10
-23
J/K)
T = Temperature (K)
R = Source resistance (ohms)
F = Noise bandwidth (Hz)
At a room temperature of 293K (20°C), the above equa-
tion simplifies to:
Since the peak to peak noise is five times the RMS value
99% of the time, the peak-to-peak noise can be equated as
follows:
For example, with a source resistance of 10k
Ω
, the noise
over a 0.5Hz bandwidth at room temperature will be:
Minimizing source resistance noise
From the above examples, it is obvious that noise can be
reduced in several ways: (1) lower the temperature; (2)
reduce the source resistance; and (3) narrow the band-
width.
E
RMS
4kTRF
=
E
RMS
1.27
10
-10
RF
×
=
E
p-p
6.35
10
-10
RF
×
=
E
'p-p
6.35
10
-10
10
10
3
×
(
)
0.5
(
)
×
=
E
p-p
45nV
=