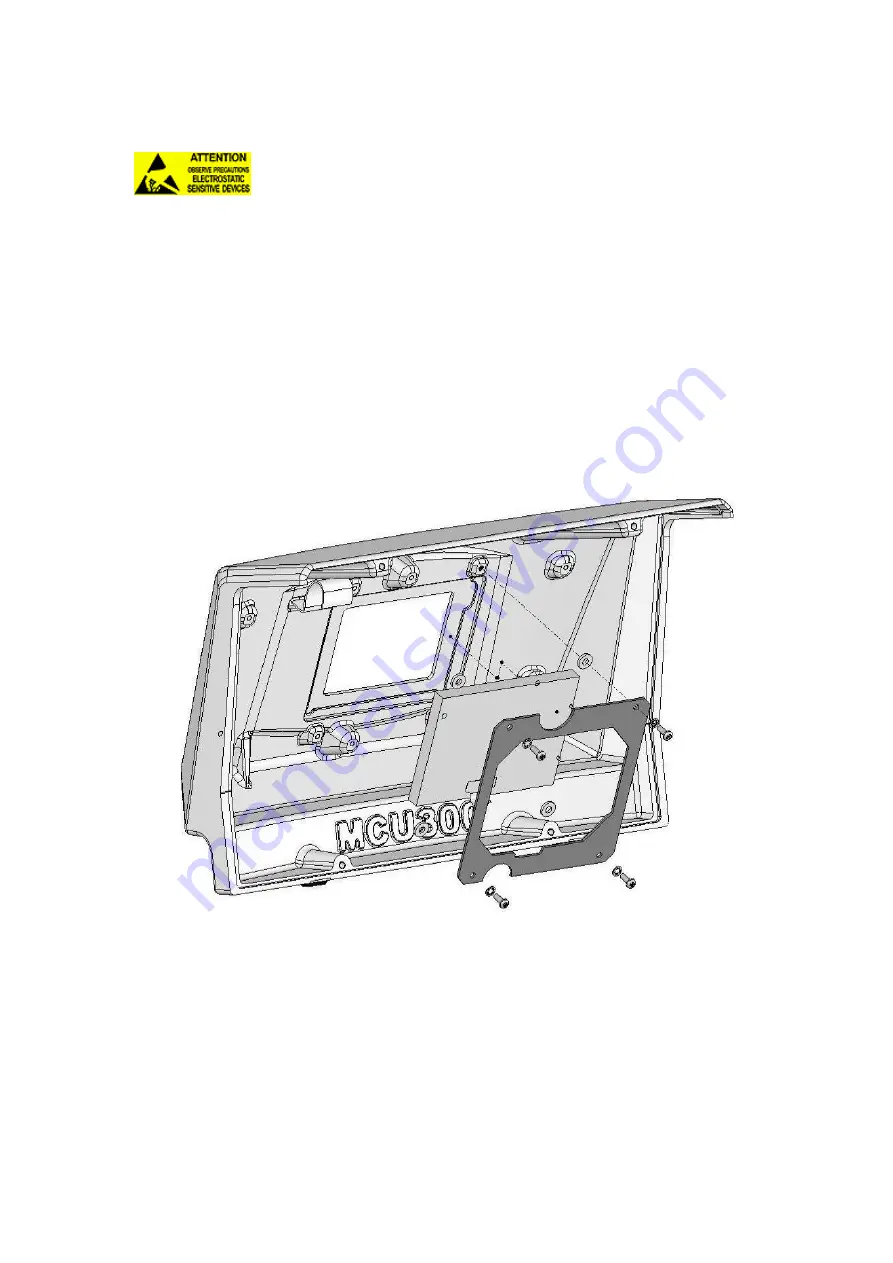
KCU401-2 Keeler Cryomatic Service Manual
LCD Panel
Observe proper precautions for the prevention of damage
to static sensitive devices.
It is unlikely that the LCD panel will fail but should the
need arise, the LCD panel can be removed in the following
manner.
a)
Remove the Controller PCB Assembly (see previous
section).
b)
Remove 4 pan-head screws which secure the LCD
retaining bracket. Ensure that the 4 spacers are
retained.
c)
Carefully remove the LCD Panel.
d)
Re-fitting is the reverse of removal – ensure that the
panel is centred correctly before finally tightening
the retaining bracket.