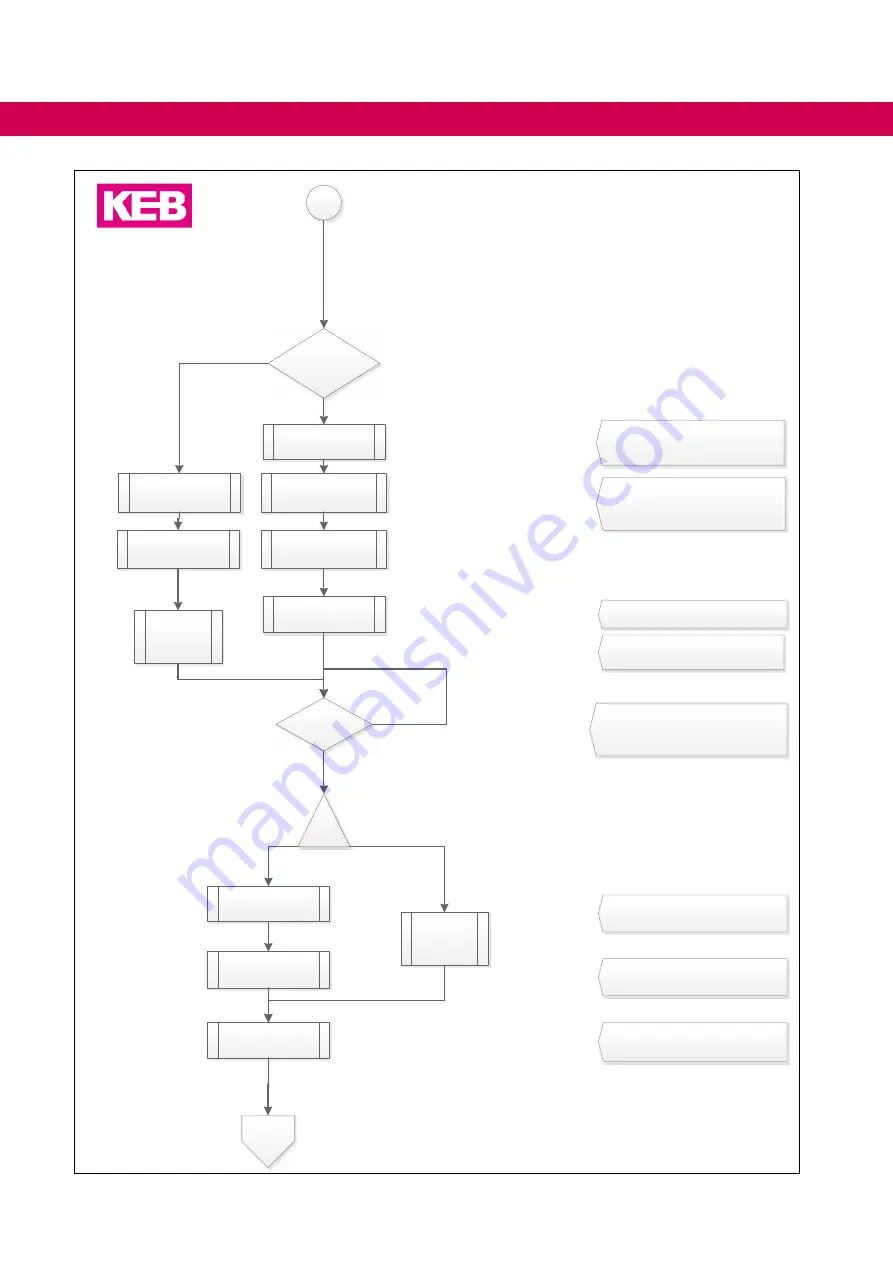
Precharging on
set control word
co00 := 3
ST with control
word?
set I2
yes
no
dr55 = 14?
set control word
co00 := 11
set control word
co00 := 3
set control word
dr54 := 0
Identification off
no
yes
Identification successfully completed?
1
2
3
4
5
6
7
8
9
10
11
modulation on
or
toggle I2
Modulation off
precharging off
set control word
co00 := 0
Start identification, see programming
manual determination of the network
impedance
set dr54 := 1
set dr54 := 1
set dr99 := 0
set dr99 := 0
sub procedure
mains ident
12
13
I2 start precharging und modulation on
78
START-UP
Summary of Contents for COMBIVERT 14H6 Series
Page 2: ......