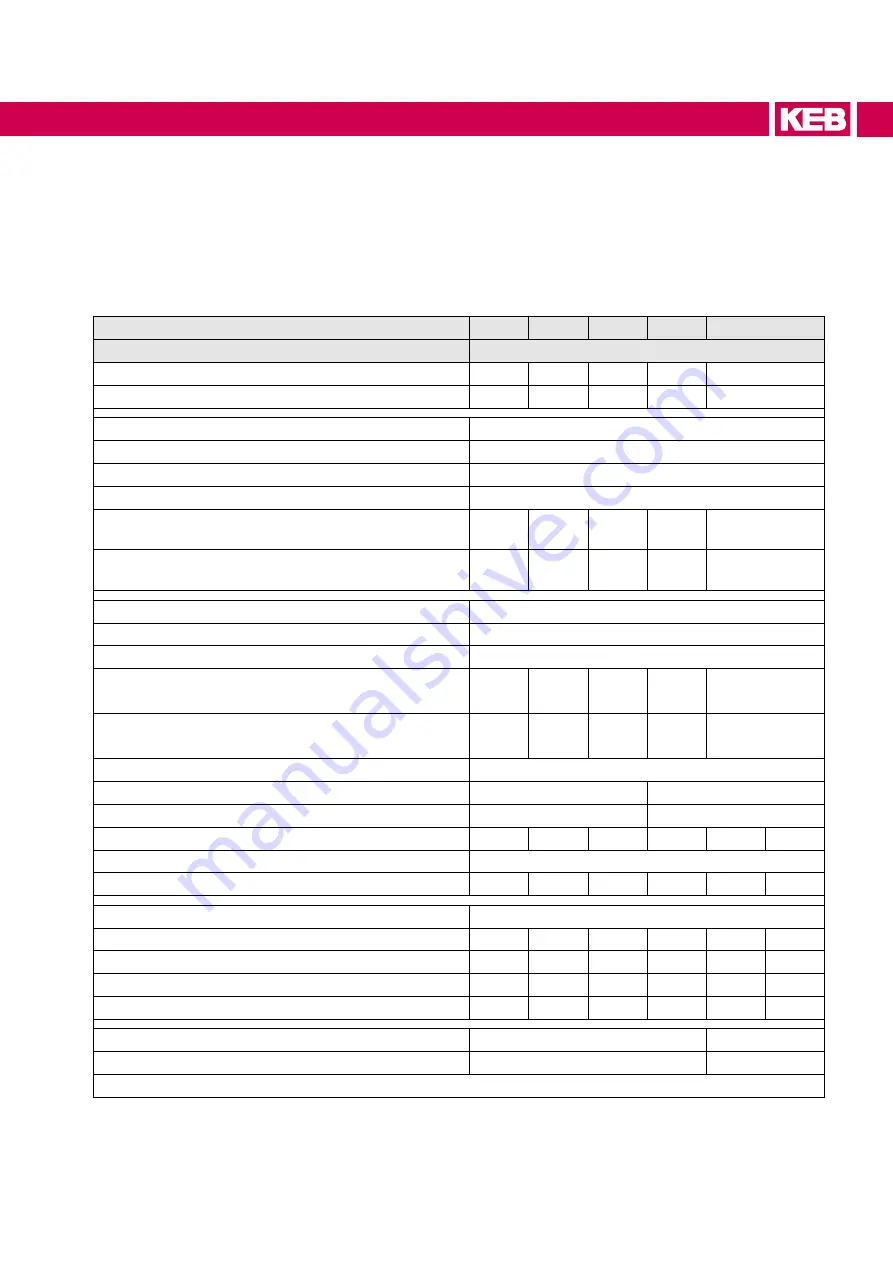
39
DeVIce DATA OF THe 400 V DeVIceS
3.3 Device data of the 400 V devices
3.3.1 Overview of the 400 V devices
The technical data are for 2/4-pole standard motors. With other pole numbers the drive
converter must be dimensioned onto the rated motor current. Contact KEB for special or
medium frequency motors.
Device size
12
13
14
15
16
Housing
2
Rated apparent output power
S
out
/ kVA
6.6
8.3
11.4
16.6
22.9
Max. rated motor power
P
mot
/ kW
4
5.5
7.5
11
15
Rated input voltage
U
N
/ V
400 (UL: 480)
Input voltage range
U
in
/ V
280...550
Mains phases
3
Mains frequency
f
N
/ Hz
50 / 60 ±2
Rated input current
@
U
N
=
400V
I
in
/ A
13
17
21
31
43
Rated input current
@
U
N
=
480V
I
in_UL
/ A
11
15
18
27
35
Output voltage
U
out
/ V
0...
U
in
Output frequency
2)
f
out
/ Hz
0...599
Output phases
3
Rated output current
@
U
N
=
400 V
I
N
/ A
9.5
12
16.5
24
33
Rated output current
@
U
N
=
480 V
I
N_UL
/ A
7.6
11
14
21
27
Rated output overload (60 s)
1) 5)
I
60s
/ %
150
Software current limit
I
lim
/ %
180
150
Overcurrent
1)
I
OC
/ %
216
180
Rated switching frequency
f
SN
/ kHz
8
8
4
4
2
4
Max. switching frequency
4)
f
S_max
/ kHz
16
Power dissipation at rated operation
3)
P
D
/ W
155
180
175
250
275
330
Overload current over time
I
OL
/ %
=> „Overload characteristic (OL) for 400 V devices“
Maximum current 0Hz / 50Hz at
f
S
= 2 kHz
I
max_out
/ % 211/216 216/216 157/216 108/180 100/180 127/180
Maximum current 0Hz / 50Hz at
f
S
= 4 kHz
I
max_out
/ % 168/216 200/216 145/216 100/180 75/166 100/180
Maximum current 0Hz / 50Hz at
f
S
= 8 kHz
I
max_out
/ % 116/216 100/216 72/187 50/129 48/118 91/180
Maximum current 0Hz / 50Hz at
f
S
= 16 kHz
I
max_out
/ % 63/168 58/150 42/109 29/75
24/69 58/124
Max. braking current
I
B_max
/ A
21.5
33.6
Min. braking resistor value
R
B_min
/ Ω
39
25
continued on the next page
Summary of Contents for COMBIVERT 10F6 Series
Page 2: ......
Page 82: ...82 NOTES...