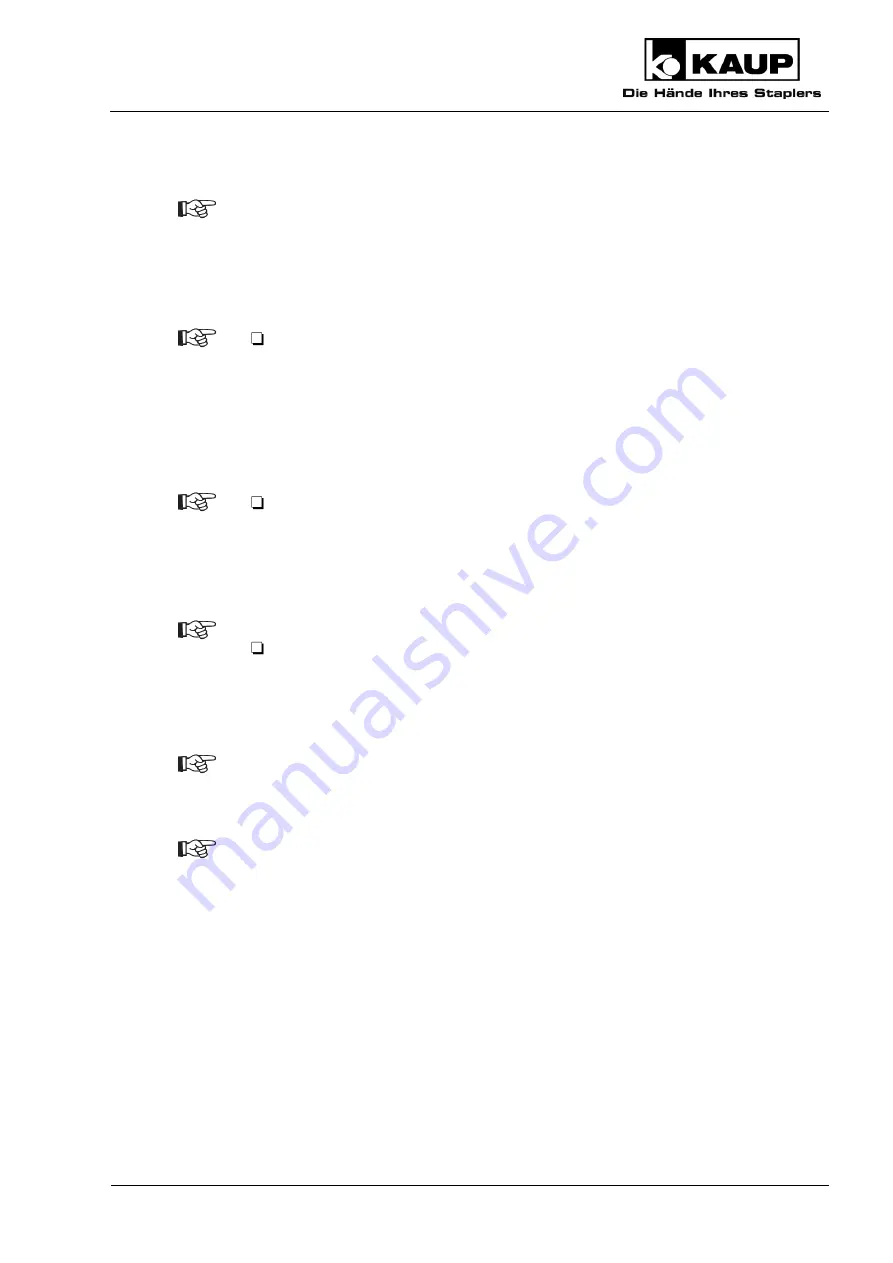
Operating Manual
Original Operating Manual
19
Daily
Check all lines, hoses and connections for leakage and damage.
After 50h / every 500h thereafter
Check:
srcrews (10) on the clamp body (7, 9) / flange (11).
Replace loose or damaged screws. Torque the screws as specified in Chapter 6.1
General.
Weekly
Grease:
Sliding pieces (2) by way of the greasing nipples (1).
The supporting rollers in the standard version are maintenance-free.
Every 200h
Check wear on:
Sliding pieces (2).
As necessary
Replace worn sliders (2) by removing nut (5) from each cylinder (6). Pull the arms to
the side to remove (see chapter 3.1). Remove the greasing nipple (1) and the screws
(3, 3a). Replace the sliders (2). When installing the new sliders, make sure that the
axial stops (4) are correctly seated. Remount the screws (3, 3a) and the greasing
nipple (1). Push the arms into clamp body and reinstall nuts (5) of cylinders (6).
After installing or removing a cylinder (6), always check the clearance between the
cylinder mount and nut of the cylinder (8). Cylinders are installed with axial clearance
of 1.5 to 2 mm.