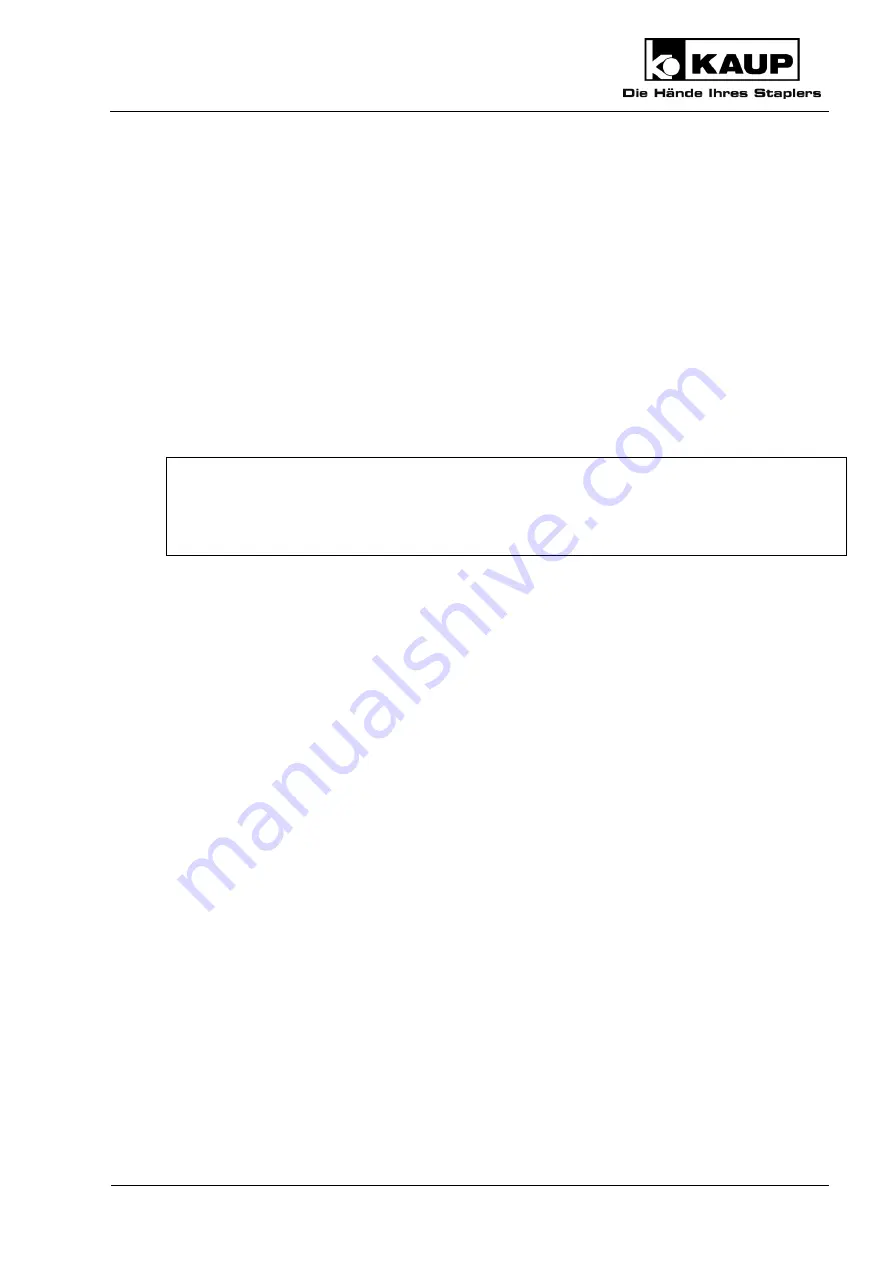
Operating Manual
Original Operating Manual
31
10.
Decommissioning and storage
If the attachment is to be stored for an extended period, all hydraulic connectors must be sealed
against contamination and damage. Store the attachment in a clean, dry environment.
11.
Spare parts list
(not part of the Operating Manual)
12.
EC Declaration of Conformity (Summary)
KAUP GMBH & Co. KG
•
Braunstraße 17 •
D-63741 Aschaffenburg
we hereby declare that the machinery
Model:
Drum Tippling Clamp
Type:
T 416 H, T 406 H, T416 2H, T 406 2H
T 416 U, T 406 U, T416 2U, T 406 2U
conforms to the latest valid version of the Machinery Directive 2006/42/EG.
The person authorised to compile the technical documents:
see EC-Declaration of Conformity
KAUP GmbH & Co. KG