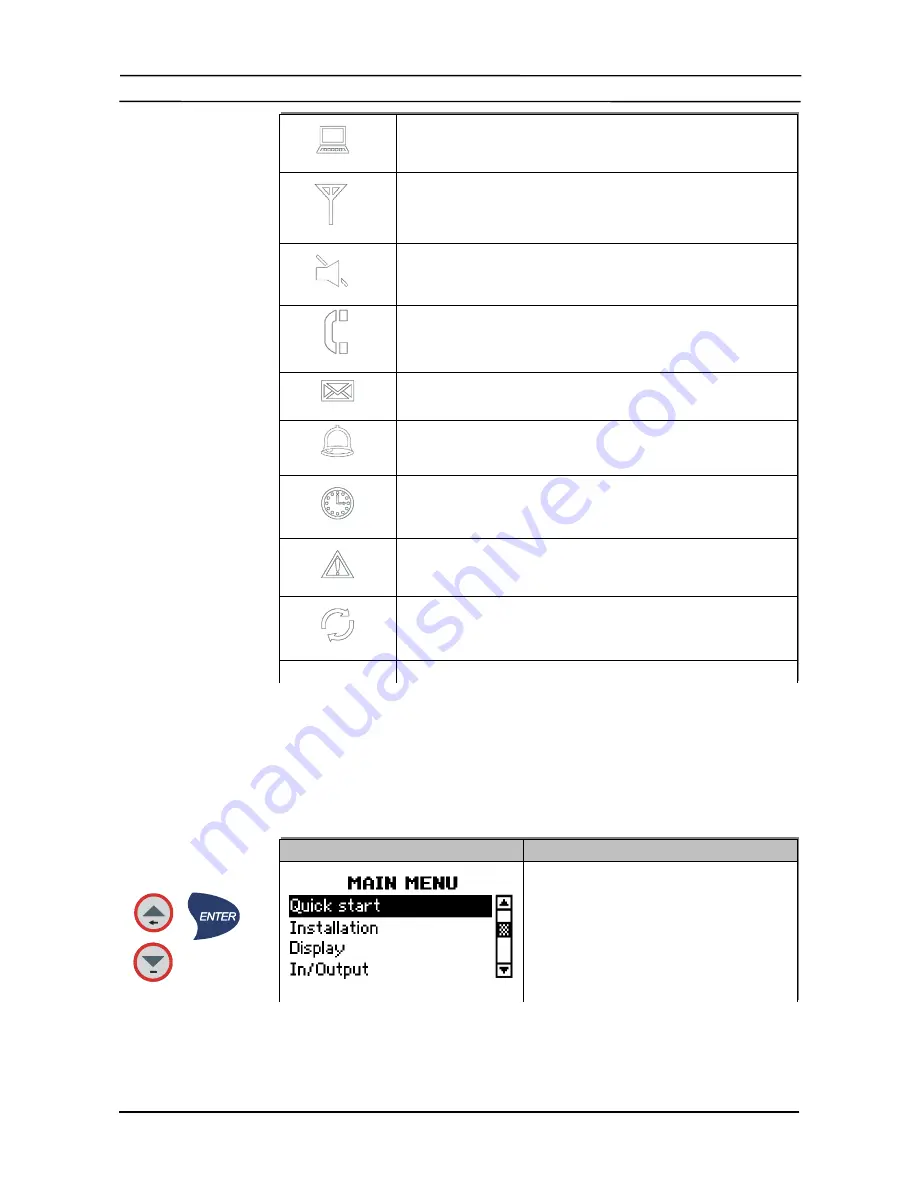
KATflow 100
4 Operation
On
Backlight switched on
Off
Backlight switched off
On
I/O processor error (internal screen only)
Off
I/O processor functioning correctly
On
Without strike-through:
Speaker on
Off
With strike-through:
Speaker off
On
Poor sensor coupling, low SNR (internal screen only)
Off
Sensor coupling OK
On
Not used
Off
On
Not used
Off
On
Time/date set (where specified)
Off
Clock error
On
Error recorded in error log
Off
No error detected
On
Serial communication on (where specified)
Off
Serial communication off
"L", "T" or "LT"
Displays whether flow is laminar, turbulent or mixed
4.3 Quick setup wizard (using programmer or screen)
The quick setup wizard allows for a speedy setup of the most important parameters
in order to achieve successful measurements in the shortest possible time:
Alternative specifications are shown in light grey.
Display screen
Operation
The main menu is displayed after first power
on and the boot-up sequence.
Use <
UP
> and <
DOWN
> cursor keys to select
Quick start
. Confirm by pressing <
ENTER
>.
23
Quick start wizard
Table 5: Quick setup wizard
Table 4: Display icons