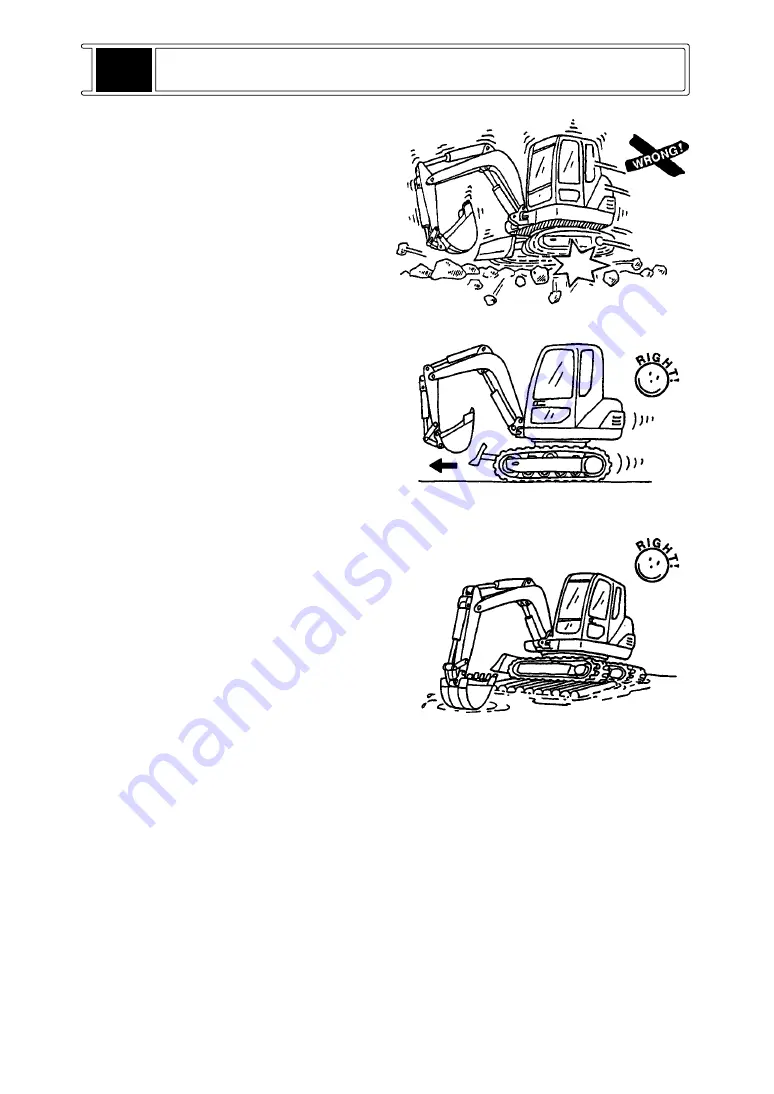
1 – 24
ᵏ
SAFETY
SLOWLY TRAVEL THE MACHINE IN
SPECIAL CONDITIONS.
Travel slowly when the ground is rough or
covered with chunks of rock. Control the travel
speed with the engine throttle lever.
NEVER
cause shocks to the tracks and the
machine.
POSITION THE DRVIE SPROCKET TO
THE RIGHT POSITION.
ALWAYS
travel with the drive sprocket to rear.
Keep the drive sprocket to rear in long travel
in particular. If you position tt to front, wear at
the lower structure will be enhanced.
UTILIZE MATS AT A SPECIAL JOB SITE.
Use mats made of lumbers to support the
machine on the soft ground or in a marsh.
Use the clean and level mats for safe
operation. Remember that the mats cannot
support the machine in every condition.
Carefully check the job site first and confirm
that safety can be secured by the mats.
Sprocket
Summary of Contents for 17VXE
Page 2: ......
Page 62: ...2 1 8 ...
Page 110: ...5 1 HYDRAULIC SYSTEM DIAGRAM 5 1 HYDRAULIC SYSTEM DIAGRAM 2 9 30 ...
Page 118: ...MINI EXCAVATOR 17VXE PUBLISHED MARCH 2017 KATO IMER S p A ITALY ...
Page 119: ......
Page 120: ......