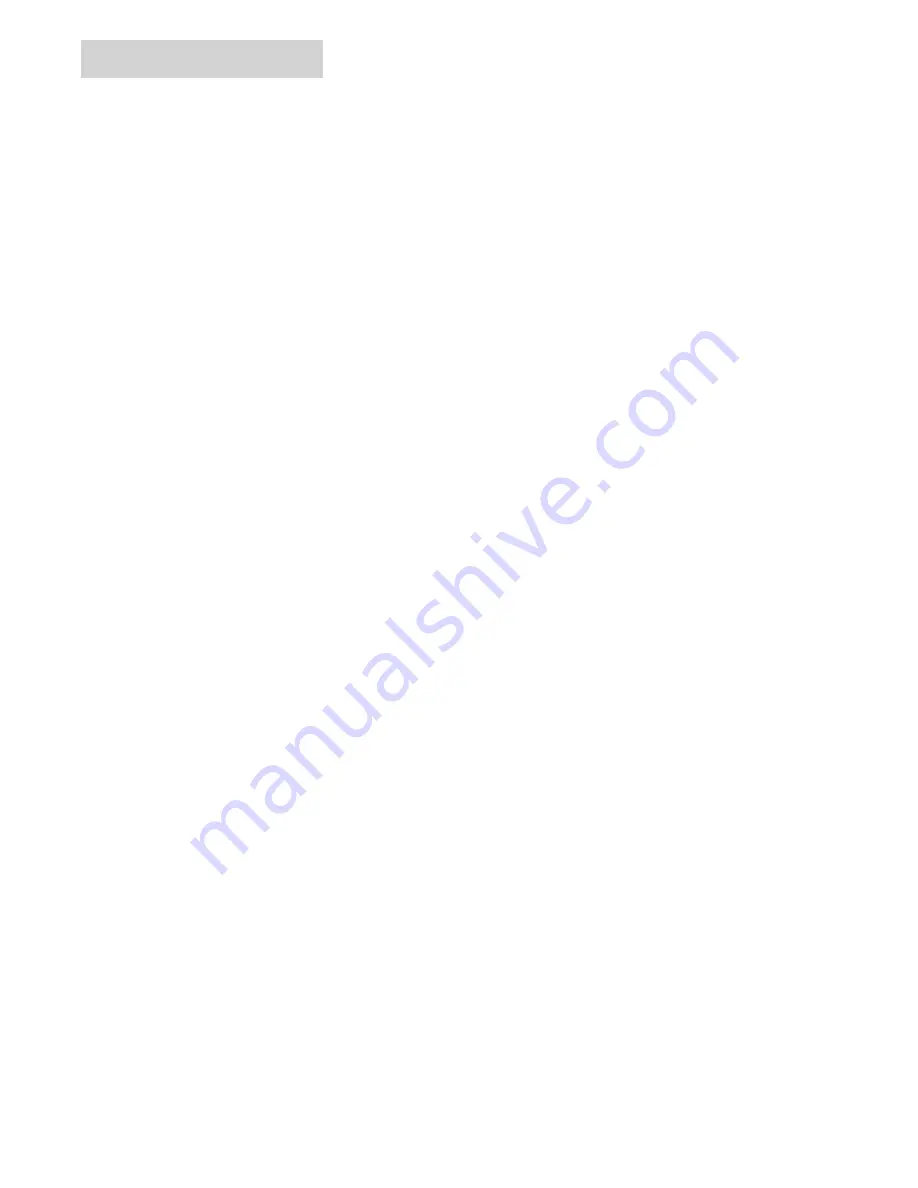
-
2
Hauptverband der gewerblichen Berufsg-
enossenschaften e.V. (HVBG). Liquified
gases (propellants) are butane and pro-
pane or a mixture of butane/propane. They
are available in special cylinders. The op-
erating pressure of these gases depends
on the outside temperature.
Danger
Risk of explosion! Do not handle liquified
gas like petrol. Petrol evaporates slowly,
liquified gas immediately turns into gas.
The risk of gas spreading in the room and
getting ignited is thus higher in case of liq-
uefied gas than in petrol.
Danger
Risk of injury! Use only liquefied gas cylin-
ders with propellant filled according to DIN
51622 of A or B quality, depending on the
surrounding temperature.
Caution
Use of cooking gas is strictly prohibited. For
the gas engine, use only liquid gas mix-
tures of propane/ butane or their mixtures
where the mixing ratio lies between 90/10
to 30/70. On account of better cold start
behaviour even at low outside sub-zero
temperatures (below 32 °F) always prefer a
mixture with a higher propane share be-
cause evaporation takes place even at low
temperatures.
–
All persons handling liquid gases are li-
able to acquaint themselves with the
special properties of the liquefied gases
for hazard-free handling of operations.
The current documentation is always to
be kept with the sweeper.
–
Propellant-operated units are to be
checked at regular intervals, at least
once a year, by an expert against leaks
(according to BGG 936) and ensure
that the unit is functioning properly.
–
The inspection must be certified and
documented. The inspection guide-
lines are § 33 and § 37 UVV (occupa-
tion accident prevention regulations)
"Use of liquid gas" (BGV D34).
–
General applicable regulations are the
guidelines for inspecting vehicles
whose engines are driven by liquefied
gases of the Federal Transportation
Minister.
–
Gas must always be drawn only from
one cylinder. Drawing gas from multi-
ple cylinders simultaneously can cause
liquid gas from one cylinder flowing into
the other. This causes the over-filled
cylinder to be subjected to an unpermit-
ted excess pressure when the cylinder
valve is closed later (refer B.1 of these
guidlines).
–
Ensure the correct positioning of the
cylinder with the "top" marking while
connecting a full cylinder (the connec-
tion screw points vertically upward).
Replace cylinders carefully. While con-
necting and disconnecting the gas cylin-
ders, the gas outlets of the cylinder valve
must be closed properly by tightening the
locking nuts with a spanner.
–
Discontinue the use of leaky gas cylin-
ders. Such cylinders are to be emptied
by slowly letting out the gas in open
spaces by conforming to all safety reg-
ulations and are to be indicated as
leaky. Also inform the issuing company
or its representative (the filling-station
attendant) in writing about the damage
to the cylinder while delivering or re-
ceiving the cylinders.
–
Before connecting the gas cylinder,
check that its connection neck is in a
proper state.
–
After connecting the cylinder, regularly
check that it is not leaky by using a
foaming agent.
–
Open the valves slowly. Do not use
hammers to open and close the cylin-
ders.
–
Use only dry fire extinguishers (with
carbonic acid gas) in case of fire
caused by liquefied gases.
–
The entire LPG unit must be continu-
ously checked to ensure that there are
no leaks and the unit is functioning
properly. Using the vehicle with a leaky
gas unit is strictly prohibited.
–
First close the cylinder valve before
loosening the pipe or tube connection.
Unscrew and loosen the connection nut
of the gas cylinder slowly because oth-
erwise the gas under pressure in the
tube will flow out instantly.
–
If the gas is refilled from a larger tank,
then ask the sales agent of the LPG
about the important regulations to be
followed.
Danger
Risk of injury!
–
LPG in a liquid state can cause frost
bites on bare skin.
–
After disconnecting the cylinder, tighten
the closing nut firmly on the connecting
threading of the cylinder.
–
Use soap water or some such foaming
agent to check whether the cylinder is
leaking. The use of open flames to illu-
minate the LPG unit is strictly prohibit-
ed.
–
Follow the manufacturer's installation
specifications while changing individual
parts of the LPG unit. Close all cylinder
and locking valves while doing so.
–
Regularly check the status of the elec-
trical unit of the LPG vehicles . Sparks
can cause explosions if the gas-carry-
ing parts of the unit are leaky.
–
If a LPG-driven vehicle has been idling
for a long time, then first ventilate the
setting room before commissioning the
vehicle or its electrical unit.
–
Immediately inform the trade associa-
tion and the concerned trade superviso-
ry authority about accidents with gas
cylinders or LPG units. Store the dam-
aged parts carefully until all investiga-
tions have been completed.
–
Propellants or LPG cylinders must al-
ways be stored according to the regula-
tions of TRF 1996 (Technical
Regulations for Liquid Gases, refer DA
to BGV D34, Appendix 4).
–
Always store the gas cylinders in a ver-
tical position. Use of open flames and
smoking at the installation site of the
cylinders and during repairs is strictly
prohibited. Protect the stored cylinders
against unauthorised access. Close all
empty cylinders properly.
–
Close the cylinder and main locking
valves immediately when you switch off
the vehicle.
–
Follow the regulations for garages and
the construction guidelines of the re-
spective State about the location and
structure of the parking areas for LPG-
driven vehicles.
–
Gas cylinders are to be stored in sepa-
rate rooms away from the parking areas
(refer DA to BGV D34, Appendix 2).
–
The electrical hand-held lamps used in
the rooms are to be equipped with
closed, sealed case and a strong pro-
tection cover.
–
Close all cylinder and main valves be-
fore working in repair workshops and
protect the gas cylinders against effect
of external heat.
–
A responsible person must check that
all valves, especially the cylinder
valves, are closed during operational
breaks and before closing the factory.
Do not carry out any jobs involving fire -
such as cutting and welding jobs - in the
vicinity of the gas cylinders. Do not
store gas cylinders, not even empty
ones, in the workshops.
–
The parking and storage rooms and the
repair workshops must be ventilated
properly. Please note that liquefied
gases are heavier than atmospheric air.
They get collected on the floor, in re-
cesses and other holes in the floors and
form a gas-air mixture that can lead to
explosions.
Safety Guidelines for liquified gas
vehicles (only KM 120/150 R LPG)
Liabilities of the factory management
and the employee
Maintenance by expert
Commissioning/Operations
In the installation and storage rooms as
well as the workshops
3
EN
Summary of Contents for KM 120
Page 20: ......