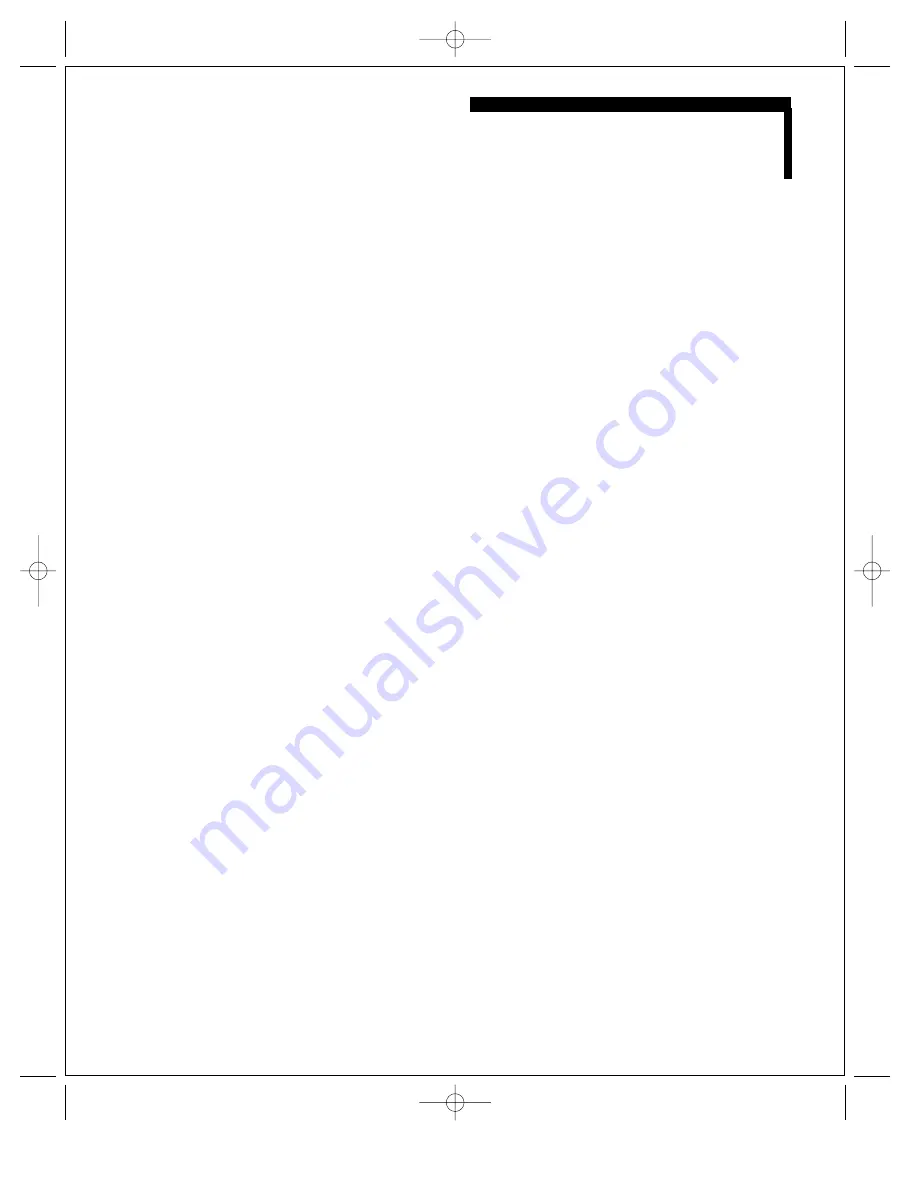
KARCHER OVERVIEW
Bypass Valve
When the trigger of the spray gun is pulled, the entire pump
capacity flows through the nozzle insert (32) to the water outlet
(34). At this time, the bypass valve remains in the upper position
and closes off the path between the pressure chamber and the
suction chamber.
When the trigger of the spray gun is released, water ceases to
flow through the nozzle insert (32). The pressure above the by-
pass valve (19) rises, which causes the bypass valve to be
pressed downwards. This will cause the pump to run in the
bypass mode. The pump continues to run, but only maintains the
circulation pressure.
When the trigger of the spray gun is again pulled, the pressure in
the high-pressure hose drops suddenly. The spring inside the
bypass valve (19), together with the restricted pressure at the
entrance to the nozzle insert (32), pushes the bypass valve
upwards. This causes the bypass valve to close, and the pump
builds up pressure once more.
Thermal Relief Valve
If the pump should continue to run in bypass mode for an extend-
ed amount of time (max 5 min.), the water circulating within the
pump will reach a temperature level that will cause internal
damage. This is prevented by the thermal relief valve (17). The
thermal relief valve will release the hot water and then automati-
cally reset itself.
Detergent Delivery System
In this system there is a nozzle insert (32) in the water outlet (34). The
entire pump capacity flows through the nozzle insert to the spray gun.
Detergent can only be drawn in by the nozzle insert (32) if the
nozzle of the spray wand has been set to low pressure. This
causes the pump pressure to fall to approximately 435 PSI (low
pressure), and the greatest degree of negative pressure (11.6
PSI) is generated at the lateral hole in the nozzle insert so that
detergent can be drawn into the unit via the detergent suction
tube (40) and detergent filter (41).
If the spray nozzle on the spray wand is set for high-pressure
operation, the hole in the nozzle insert (32) does not create any
negative pressure, and no detergent can be drawn into the unit.
The detergent non-return valve (36) consists of a small spring (39)
with a ball (38), O-ring (37) and nipple (35). When operating in the
detergent mode, the negative pressure created by the nozzle
insert (32) causes the ball to be drawn away from the O-ring (37),
against the tension of the spring (39). Detergent can then be
drawn into the unit.
When operating in the high-pressure mode, the ball (38) seals off
the detergent connection so that no water can flow into the con-
tainer of detergent.
Swash Plate Assembly
The three pistons (9) are driven by the swash plate assembly (6,7,8),
which is mounted on a pump shaft (3). In the case of a vertically
configured machine, a drive bolt is screwed into the engine shaft
and then inserted into the pump shaft. As soon as the engine shaft
rotates, the swash plate assembly (6,7,8) rotates as well. This caus-
es the pistons (9) to move backwards and forwards. The piston
stroke depends upon the angle of the swash plate assembly (6,7,8).
The greater the angle of the swash plate, the longer the piston
stroke. One revolution of the swash plate gives the pistons one
suction stroke and one pressure stroke.
Oil Bath
The swash plate and pistons are bathed in oil
(oil type 15W40 non-detergent).
This pump does not have a drain plug, oil reservoir and sight glass.
In order to add oil in this case, the pump head (48) and piston hous-
ing (11) will have to be removed. If servicing a pump without a sight
glass, the oil level is just above the high side of the swash disk (8).
Pistons With Seals
The three pistons (9) are pressed against the swash disk (8) of the
swash plate assembly (6,7,8) by powerful piston springs (10). These
three pistons are manufactured from tempered, surface-hardened
steel and are non-corrosive with regards to detergents and rust.
The pump delivery capacity is determined by
- the rotational speed of the motor
- the diameter of the pistons
- the length of the piston stroke.
The pistons (9) are fitted with a high-pressure bushing (30).
The three pistons each have an oil seal (28) mounted in the piston
housing (11). These three oil seals, along with the shaft seal (3),
retain the oil in the oil bath housing. The slot holes (12) are in the
piston housing (11) and allow water or oil to drip out into the open.
A water leakage rate of one drop per piston per minute is allow-
able during high-pressure operation.
If oil is leaking from the slot
holes (12), there is either a leak in the oil seals or there is piston dam-
age.
Low-Pressure and
High-Pressure Check Valves
Each piston (9) works with one low-pressure check valve (24-27)
and one high-pressure check valve (43-46). Each of these check
valves is constructed of the same basic components: the valve
basket, spring, valve plate with guide shaft and the valve seat with
O-ring.
The sealing surface between the valve plate (25) and the valve seat
(24) is conical. The valve plate and valve seat are manufactured
from either plastic or stainless steel depending upon the particular
unit involved.
When the piston (9) is forced backwards by the piston spring (10) in
the oil bath housing (1), the high-pressure check valve (43-46) clos-
es and water is drawn in through the supply line / suction chamber
at the water inlet (20), through the inlet filter (21), and through the
open low-pressure check valve (24-27).
When the piston (9) is pushed forward by the swash disk (8), the
low-pressure check valve closes and water is conveyed through
the open high-pressure check valve to the high-pressure outlet.
The pressure that is generated is dependent upon the flow rate and
the orifice diameter of the of the high-pressure nozzle.
5
Pump 629 9/28/01 3:22 PM Page 5
www.mymowerparts.com
For Karcher Pressure Washer Parts Call 606-678-9623 or 606-561-4983