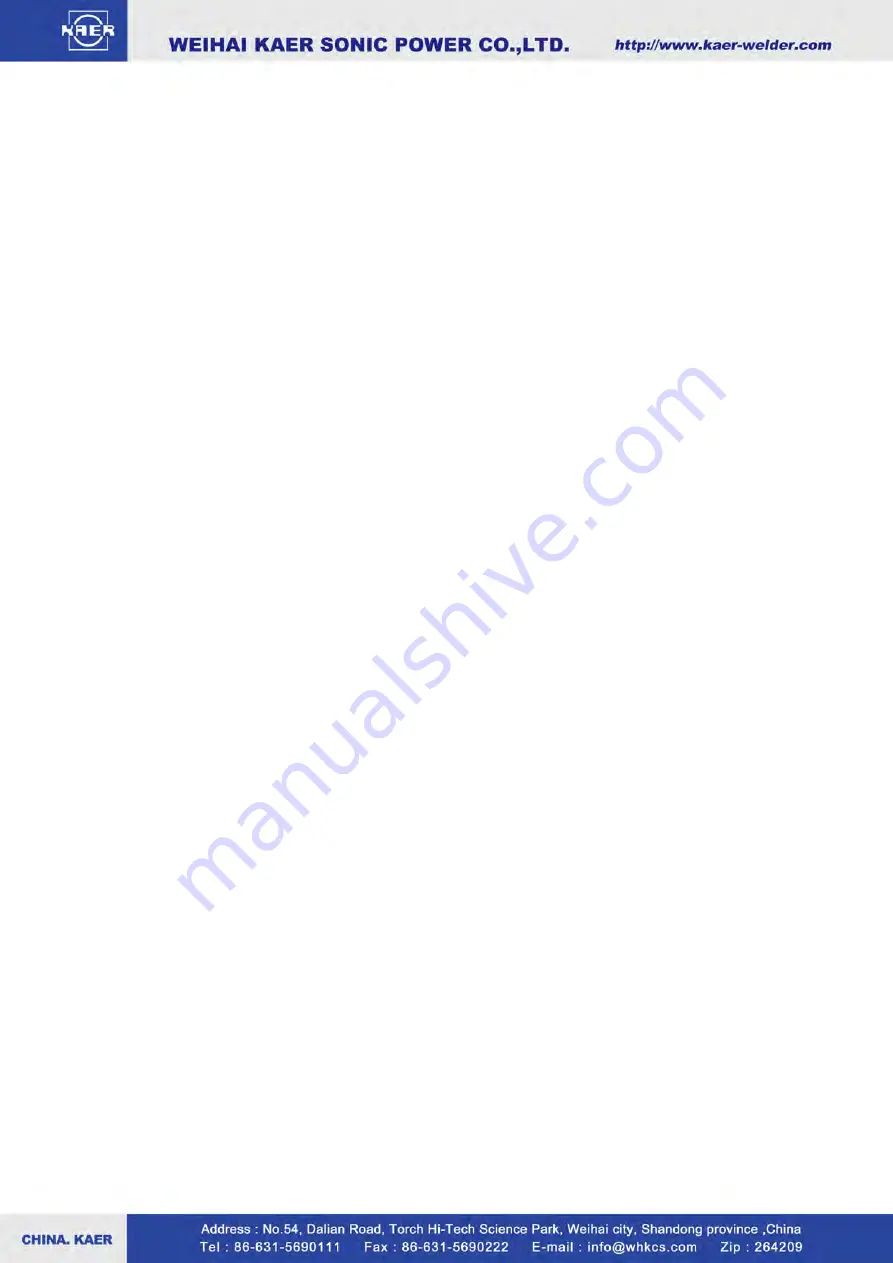
VI. Precautions for Application
1. User shall not alter welding head at option, or it may change frequency
parameters of transducer system, which will result in damages to
transducer system and ultrasonic power generating system.
2. Never leave
both hands under the welding head when the machine is in
operation or is testing ultrasonic sound, to guarantee operating safety for
operators!
3. No direct contact is allowed between the welding head and the machine
base or other metal fixtures during operation or test, to ensure safe
operation of the equipment;
4. No start-up or operation of this equipment is allowed before reliable
connection to earth!
5. Start-up or operation is prohibited where high temperature and high dust
environment exist!
6. Stable operational power supply is required while operation beyond the
rated voltage is prohibited!
7. Earplugs are recommended for a long-term operator to avoid injury by
noise pollution;
8. Proper ventilation facilities should be made available when processing
noxious plastic parts or those with peculiar smell,
9. Stop and check the machine immediately in case any abnormal noise
occurs or transducer system heats to over 50
℃
during operation. Only
after returning to normal can the production be continued; If temperature of
transducer system is still on the high side, continuous operation shall only
be allowed after cooling it down. In special situation, forced
heat-elimination measures should be taken.
10. If fuse of the machine is blown, a fuse with regulated nominal value should
be adopted. If fuse is blown for several times, the machine should be
stopped immediately for inspection. Only after an error (errors) is located
and proper repairing is conducted can it be put into application;
11. Ensure a clean air supply. When air filter is half full of water, immediate
discharging should be made.
12. Lubricate mechanical movable parts at regular intervals; remove dust from
electric cabinet regularly after a long time operation; if equipment is not
used, proper dust cover should be chosen to cover them;
13.
If heat emission fan gets blocked from running, stop immediately for
inspection. Continuous use will not be allowed until normal condition is
resumed;
14.
Special staffs shall be designed for debugging and maintaining the
equipment;
15. Please feel free to contact us should any error occurs. No continuous use
or optional alteration is allowed.
16. Press the operational button with both hands for operation. Foot operated