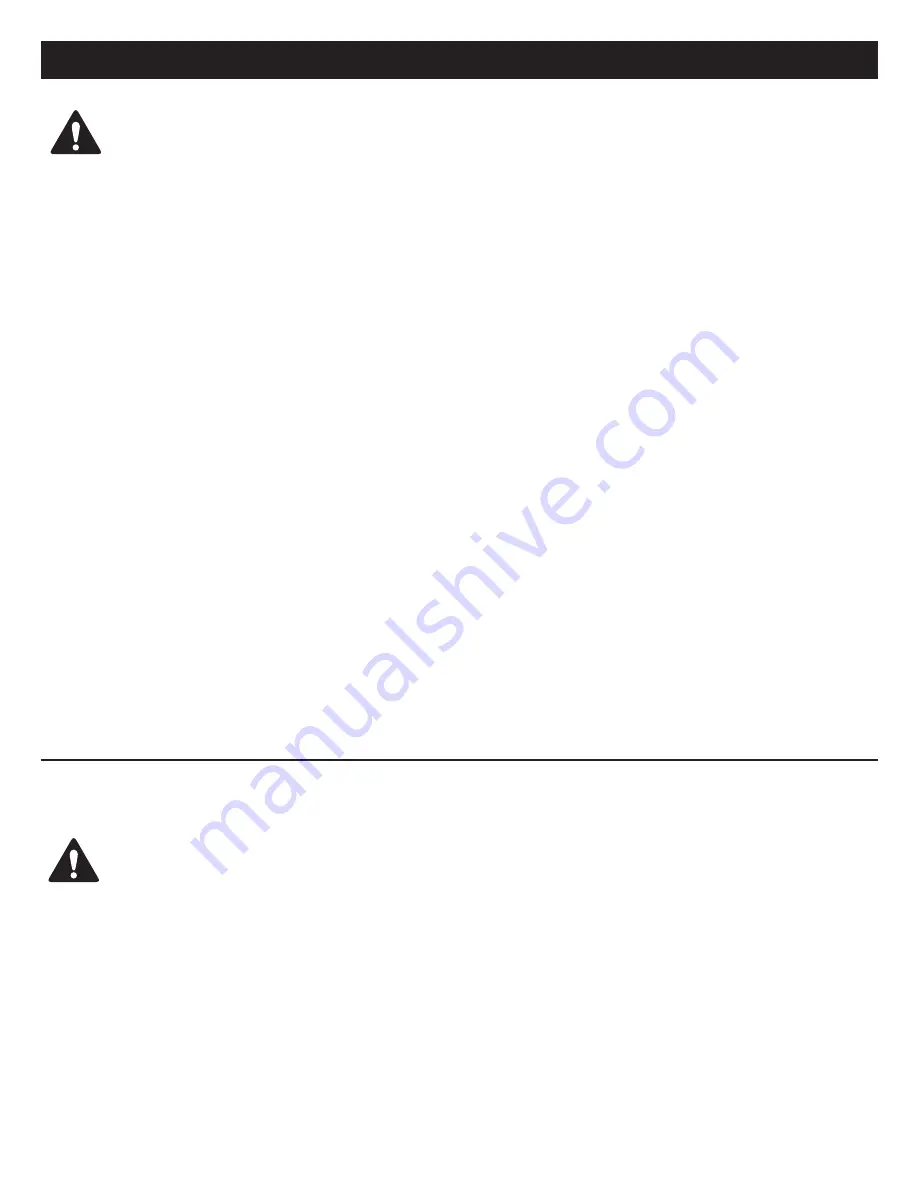
KTI63213/KTI63214/KTI63221/KTI63224
rev. 02/15/19
3
OWNER'S MANUAL
SETUP AND OPERATING INSTRUCTIONS
This is the safety alert symbol used for the SETUP and OPERATING INSTRUCTIONS section of this manual to alert you to
potential personal injury hazards. Obey all instructions to avoid possible injury or death.
PLEASE REFER TO THE EXPLODED VIEW DRAWING IN THIS MANUAL IN ORDER TO IDENTIFY PARTS.
1. Assemble the pump handle (#26) sections together to make one complete handle. One end of the handle has a cut out that will fit over the end of the release valve (#28) in the
base (#30) of the jack. This connection enables the user to turn the release valve (#28) in a clockwise direction until tight in preparation for pumping the jack and raising the load.
Slowly turning the release valve (#28) in a counterclockwise direction will lower the load. It is not necessary to open the release valve (#28) more than two full rotations.
2. The opposite end of the pump handle (#26) must be inserted in the handle receiver (#22) in preparation for pumping the jack.
3. The ram (#8) is that part of the jack which extends when the jack is pumped. The end of the ram includes an extension screw (#7) that makes contact with the load to be lifted.
Extension screw (#7) height can be extended by turning it in a counter clockwise direction. Extending the height is sometimes necessary when the full stroke of the ram (#8) is not
adequate to lift a load to its desired work height.
4. Sometimes air gets trapped in the hydraulic system during shipment. An air bound hydraulic system feels spongy when pumped and may not allow the jack to pump
full incremental strokes.
TO PURGE AIR FROM THE HYDRAULIC SYSTEM
a. Open the release valve (#28) by turning the handle (#26) in a counterclockwise direction two full turns from its closed position.
b. Pump the handle (#26) ten full strokes.
c. Close the release valve (#28) by turning the handle in a clockwise direction until tight.
d. Pump the jack until the ram (#8) is extended to maximum height.
e. Repeat steps "a" through "d" until all the air is purged from the system.
5. Do not lift more than one wheel of a vehicle at a time. Activate the hazard warning flasher, turn off ignition, move automatic selector to park position or reverse gear if it is a
manual transmission and set parking brake. The wheel diagonally opposite from the wheel being lifted shall be chocked in both directions. Consult the vehicle manufacturer
for the tire changing procedure and lift points.
6. Position the jack at the appropriate lift point. Estimate the required ram travel to raise the load to the desired height. If the desired height exceeds the entire ram travel,
unscrew the extension screw to make up the difference.
7. Pump the jack up until the extension screw (#7) comes close to the lift point. Make sure the lift point is flat, parallel to the ground and free from grease, any kind of lubricant, or debris.
Continue pumping the jack to lift the load to the desired height. During lifting, inspect the position of the jack in relation to the ground and the extension screw (#7) in relation to the
load to prevent any unstable conditions from developing. If conditions look like they are becoming unstable, slowly lower the load and make appropriate setup corrections after the
load is fully lowered.
8. When the load is lifted to its desired height, immediately place jack stands in their designated locations and adjust the stands' support columns up as close to the
designated support points as possible. Although jack stands are individually rated, they are to be used in a matched pair to support the load. Slowly and carefully open the
release valve (#28) of the jack in order to gently lower the load onto the jack stands. Make sure the load is safely supported by the jack stands' saddles and not the locating lugs
of the saddles. Inspect the relationship of the jack stands with the ground and the jack stand columns and saddles with the load to prevent any unstable conditions. If
conditions look unstable, close the jack's release valve (#28) and pump the jack to raise the load off the jack stands. Make the appropriate setup changes and slowly and carefully
lower the load onto the jack stand saddles.
9. After the work is done, close the release valve (#28) and pump the jack high enough to remove the load from the jack stand saddles. Be sure the load is stable. If it is not,
lower the load back onto the jack stands. Make appropriate setup corrections and repeat the step again. Remove the jack stands from under the load, being very careful not
to move the load.
10. Open the jack's release valve (#28) very slowly and carefully to lower the load to the ground.
PREVENTATIVE MAINTENANCE
This is the safety alert symbol used for the PREVENTATIVE MAINTENANCE section of this manual to alert you to potential personal injury hazards.
Obey all instructions to avoid possible injury or death.
IMPORTANT:
Any jack found to be defective as a result of worn parts due to lack of lubrication, or air/hydraulic system contaminated
with water, rust and/or foreign materials from the air supply or other outside source is not eligible for warranty consideration.
1. Always store the jack in a well protected area where it will not be exposed to inclement weather, corrosive vapors, abrasive dust, or any other harmful elements.
The jack must be cleaned of water, snow, sand, grit, oil, grease or other foreign matter before using.
2. The jack must be lubricated periodically in order to prevent premature wearing of parts. A general purpose grease must be applied to the threads on the extension screw.
Do not lubricate any portion of the lift saddle and make sure the saddle is free from grease, any kind of lubricant, or debris before using the jack.
3. It should not be necessary to refill or top off the reservoir with hydraulic fluid unless there is an external leak. An external leak requires immediate repair which must be
performed in a dirt-free environment by qualified hydraulic repair personnel who are familiar with this equipment. Authorized Service Centers are recommended.
IMPORTANT:
In order to prevent seal damage and jack failure, never use alcohol, hydraulic brake fluid, or transmission oil in the jack. Use Hydraulic Jack Oil.
4. Every jack owner is responsible for keeping the jack label clean and readable. Use a mild soap solution to wash external surfaces of the jack but not any moving hydraulic
components.
NOTE:
Disassembly of this tool by other than an authorized service center
will void
the war ran ty on this tool.