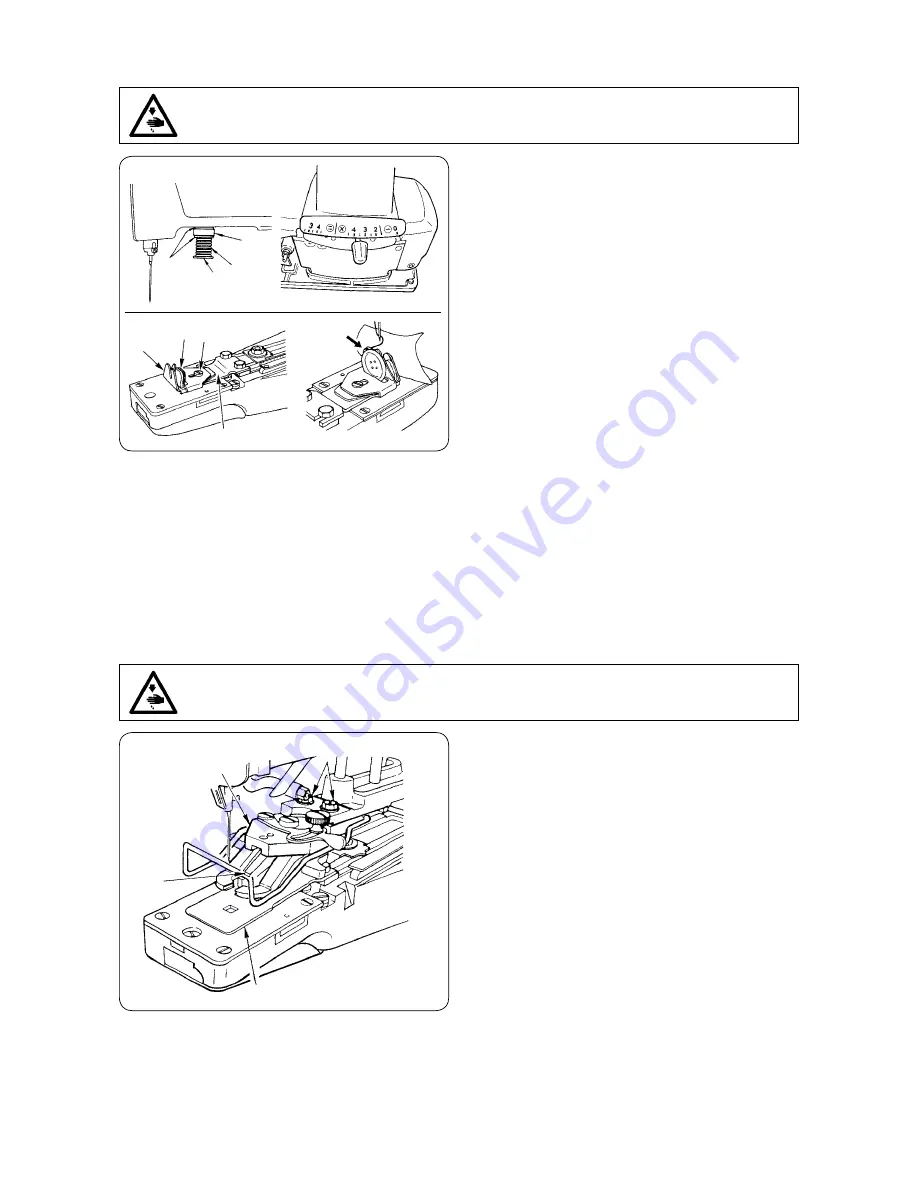
– 14 –
(3) attachment for the second process of wrapped-around buttons (Z035)
(InstallatIon)
Remove the button clamp mechansm assembly, but-
ton clamp pressure adjustng bar and feed plate from
the machne and nstall attachment for the second
process of wrapped-around buttons
1
. When you
nstall a Z035 attachment, you must remove also the
L-shaped lftng rod.
Insert movng knfe push-back sprng
3
, washer
4
, cushon
5
and washer
4
n sprng gude shaft
2
n ths order. Make certan that the stop-moton
mechansm has completely engaged, and nstall the
attachment assembly n place n the way that cush-
on
5
comes n close contact wth the surface of the
machne arm wthout play.
(aDJustMEnt anD oPEratIon)
1) Loosen screw
6
and adjust the thread shank length by movng gude (large)
7
and gude (small)
8
n
lne wth the pont of needle entry.
2) Set a button (tlt t slghtly for easy nserton) and pass the thread as the arrow shows.
3) Set the lengthwse feed to “0”.
(4) attachment for snaps (Z037)
(InstallatIon)
Remove the button clamp mechansm assembly
and the feed plate. Set both the crosswse feed and
lengthwse feed graduated plates to “4 mm”. Install
snap clamp feed plate
1
n the way that the needle
drops evenly at four corners of its square opening.
Install snap attachment assembly
2
on the machne,
place a snap on the snap clamp jaw levers and make
sure that the needle drops accurately n each hole n
the snap. If necessary. loosen hex head screws
3
and adjust the poston accurately. Lastly, make sure
that the concave secton on the bottom face of snap
clamp slde gude
4
accurately matches the convex
secton on snap clamp feed plate
1
.
WarnInG :
to protect against possible personal injury due to abrupt start of the machine, be sure to start the
following work after turning the power off and ascertaining that the motor is at rest.
WarnInG :
to protect against possible personal injury due to abrupt start of the machine, be sure to start the
following work after turning the power off and ascertaining that the motor is at rest.
1
(Z035)
2
5
4
3
1
2
4
3
7
8 6
Summary of Contents for MB-1373
Page 1: ...ENGLISH Instruction Manual...