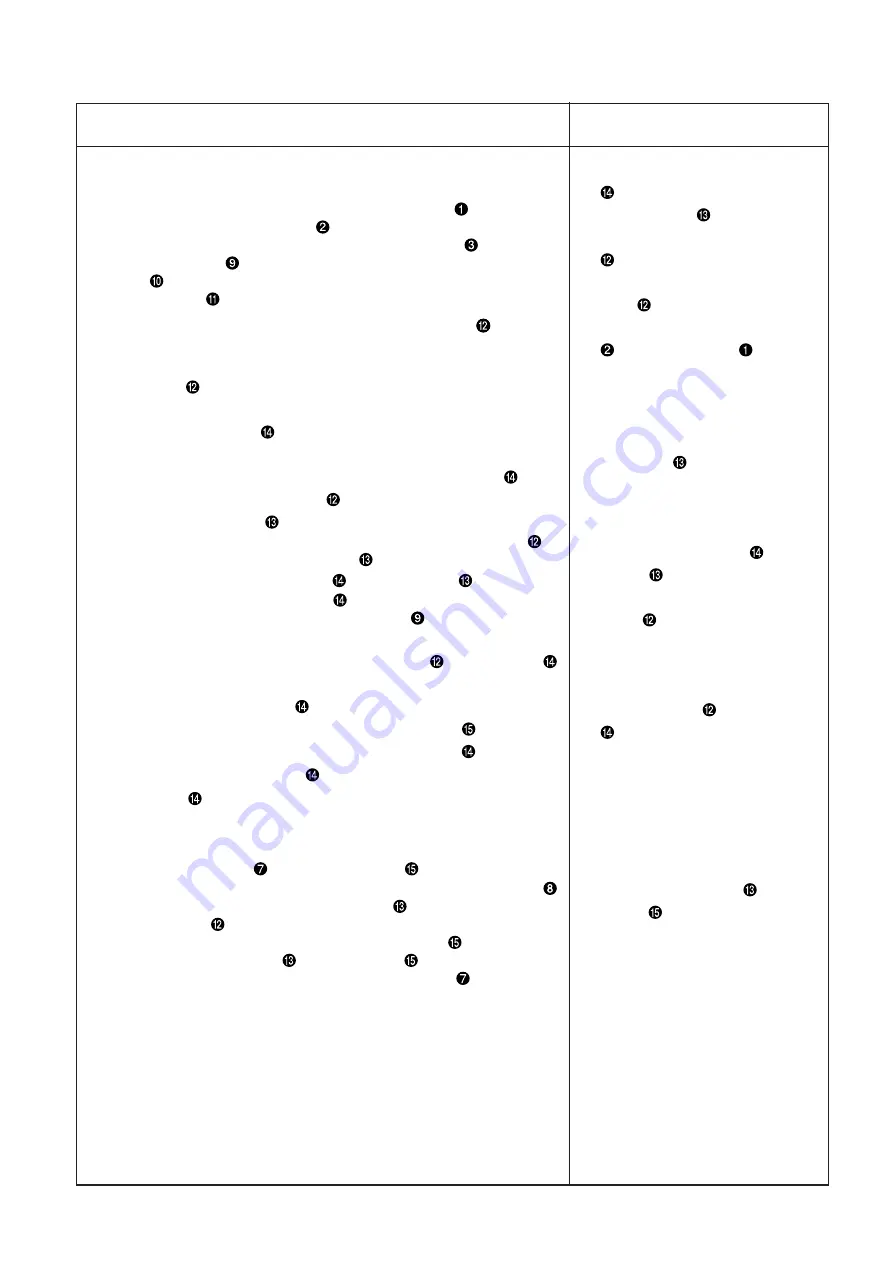
– 31 –
Adjustment Procedures
Results of Improper Adjustment
* Turn ON the power once, and turn OFF the power again after
making the intermediate presser in the lowered state.
1. Turn hand wheel by hand to ascend the needle bar
.
Adjust so that lower marker line
on the ascending needle bar aligns
with the bottom end of the needle bar bushing lower
.
2. Loosen setscrew
in the driver. Drawing bobbin case opening lover
hook
toward you, open it to the right and left until bobbin case
opening lover
comes off.
(Caution) At this time be careful not to let inner hook
come off
and fall.
3. Refer to 5. below and make tentative adjustments of timing for the
inner hook
.
4. Turn the pulley by hand and make adjustments for the needle loca-
tion block of the driver
by bending it in the direction of Arrow A so
that the clearance b attains 0mm to 0.5mm between the needle tip
and the lowest end of the needle location block of the driver
when
the needle tip of the inner hook
is protruded by 0.5mm from the
right end of the needle
.
5. Make an adjustment so that the blade point of the inner hook
is
aligned with the center of the needle
, and that the clearance be-
tween the front end of the driver
and the needle
is 0 mm be-
cause the front end of the driver
receives the needle to prevent
needle bending. Then, tighten the set screw
securing the driver.
6. Make adjustments so that the clearance (C) in the revolving direction
attains 0.3mm to 0.6mm between the inner hook
and the driver
by bending the inner hook holder block (reverse side of the needle
location block) of the driver
in the direction of the arrow (D).
(Caution) 1. Make sure not to damage the shuttle
race plane
while making adjustment of the driver
.
2. When the driver
is used for a long time, the driver
may be open to increase the clearance. In such
a case, replace it with a new one or adjust the clear-
ance.
7. Loosen the set screw
securing the shuttle
, and adjust the front-
rear position of the shuttle by rotating the shuttle adjusting shaft
so that the clearance between the needle
and the blade point of
the inner hook
becomes 0.05 to 0.1 mm.
8. After adjusting the front-rear position of the shuttle
, set the clear-
ance between the needle
and the shuttle
to 7.5 mm by adjust-
ing the rotating direction, and tighten the set screw
securing the
shuttle.
9. Make positional adjustments for the shuttle upper spring.
Refer to [3.-(43) Adjustment of the shuttle upper spring and lower
thread holder position].
o If the shuttle height of the driver
does not match the tip position
of the needle
, the needle tip
may interfere with the inner hook
and this can be a cause of
needle blunt or wear of the inner
hook
.
o If the engraved lower marker line
of the needle bar
does not
match, this can be a cause of
stitch skipping, thread breakage,
and poorly tense stitch.
o If the clearance is wide between
the needle
and the blade point
of the inner hook, this can be a
cause of thread breakage.
o If there is a clearance between
the shuttle of the driver
and the
needle
, this can be a cause of
needle blunt or wear of the inner
hook
, stitch skipping, and
thread breakage.
o If the clearance in the revolving
direction is too narrow between
the inner hook
and the driver
, this can be a cause of thread
breakage and poorly tense stitch.
If the clearance is too much, there
will be problems of noise, driver
breakage, and wear in the inner
hook race plane.
o If the clearance fails to match
between the needle
and the
shuttle
, this can be a cause of
thread breakage at the sewing
start, defective knotting, and stain
on thread.