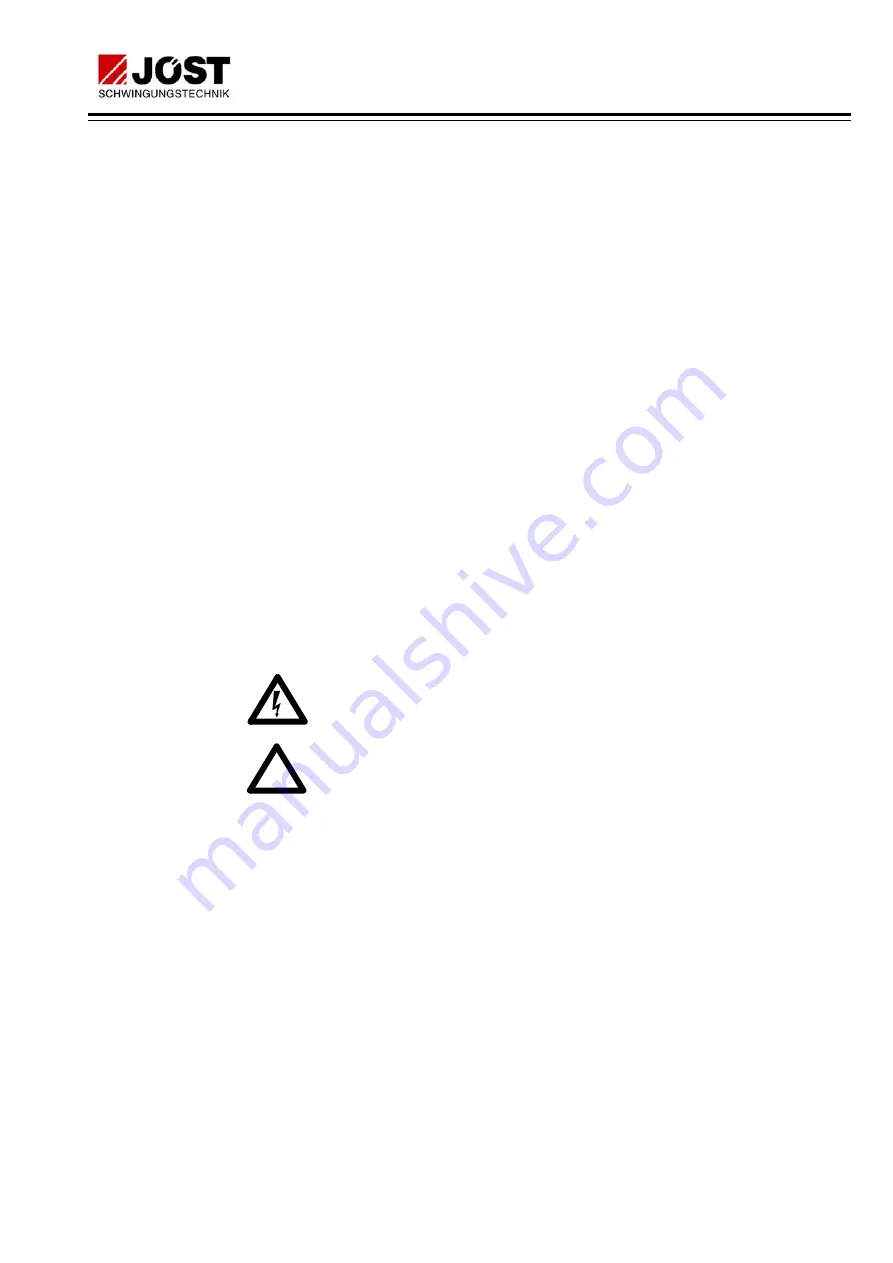
OPERATING MANUAL for
BRAKE UNITS
JB10/... JB16/... JB26/... JB40/... JB52/...
(Installation set)
JB
10 of 19
01.96/00/Scho
Please check the following points before switching on the mains voltage:
1. The brake unit must be used in conjunction with the relevant
vibrating machine.
2. The details on the brake unit rating plate must match those on
the motor. The nominal motor current (or its aggregate, in the
case of several motors) must be
≤
I
N
[A] (Entry under "A" on
the rating plate).
3. The mains voltage must be within the voltage range specified
on the rating plate (entry under "V" on the rating plate).
4. The mains must be connected to terminals a/8.
5. The brake unit must be earthed through the PE terminal.
6. Only potential free "make" contacts may be connected to
terminals 6/7.
7. The output cable of the brake unit must be connected to
terminals a/b. The motor(s) must be connected correctly.
8. No short circuits or short circuits to earth may be present.
9. Measures must be taken to ensure compatibility with EMC
legislation (see Section 2).
10. The braking contactor K1 and the motor contactor K2 (and K3)
must be electrically interlocked! See connection diagram in the
appendix.
9.2
INTERLOCKING TEST WITHOUT BRAKING CURRENT
•
Remove the motor fuses or switch off the motor protective switch.
•
Turn trimming potentiometer "T" to its maximum (clockwise).
•
Turn trimming potentiometer "I" to its minimum (anti-clockwise).
The mains voltage may now be switched on. LED "P" must light.
A dangerously high voltage will now be present at the JB
brake unit.
The braking and motor contactors must never be active at
the same time!
•
Operate motor contactor K2 (or K3) by hand: LED "M" must light.
•
Release motor contactor K2 (or K3): LED "M" will go out. LED "B"
must light and braking contactor K1 must pick up.
•
Operate contactor K2 (or K3) by hand while LED "B" is alight. Braking
contactor K1 must drop out.
!