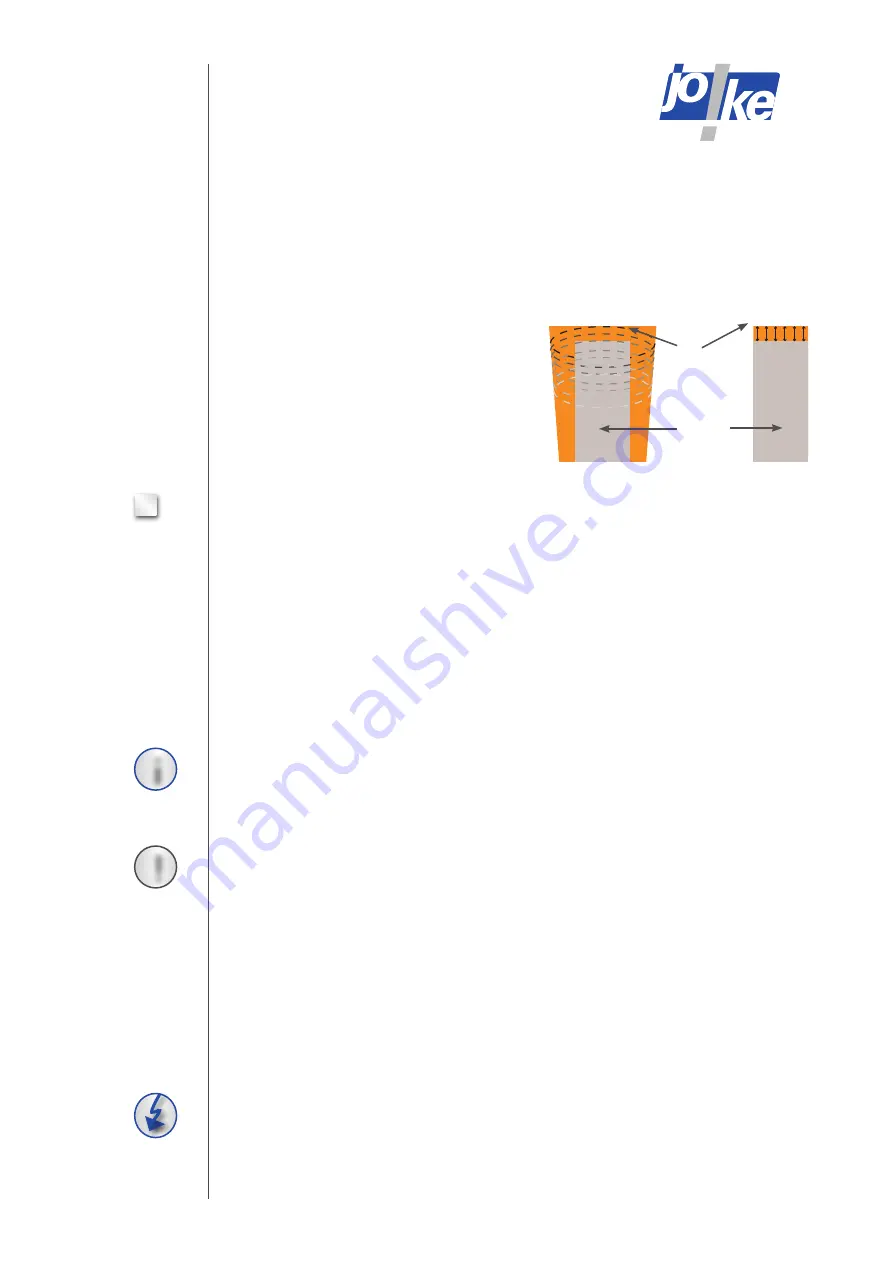
Surface Technology
Oberflächentechnik
Surface Technology
Oberflächentechnik
7
area that can
be worked
Scope of supply:
tool holder, collet, supply air hose 1.5 m, exhaust air hose, connecting sleeve ¼“ incl. filter
Turbolap TLS: the tool operates elliptically
(area marked in orange), depending on stroke length.
Turbolap TLL: the tool operates linearly
(area marked in orange), depending on stroke length.
tool
TLS
TLL
7
Operation / Use / Care
Notes on operation
• The recommended air pressure for operating the filing handpiece is indicated in chapter 6.
An increased air pressure may result in damage to the filing handpiece.
• The spindle must be treated particularly carefully during the working process and when at
a standstill. Under no circumstances must the spindle be knocked, as the components vital
to operation will be damaged as a result.
• Pay attention to the permitted cutting speeds and the tool manufacturer’s guidelines before
using the tools.
• Check that the tool is firmly seated and safely tighten.
Check the maintenance unit regularly. If condensation water and dirt are present, drain off the
condensation water and clean the filter (refer to care/maintenance section).
i
Wear goggles, protective gloves and hearing protection!
!
Filing:
The filing handpiece is excellent in combination with a wide selection of tools for precision and
deburring work on all steels and non-ferrous alloys. It offers the optimum prerequisites for use in
mould building during deburring, grinding and polishing tasks. Tools with a shaft diameter of
3.1 mm and less can be easily clamped. This is possible up to a height of 4.0 mm with flat tools.
Pay attention to proper handling of the device. Do not put any pressure on the tools. The tools
should only be guided over the surfaces.
Correct clamping of the tools is indispensable. Do not use any distorted or worn files.
Futher technical data:
Air consumption: ¼“ female thread (FT)
Dimensions in mm: Ø 28 x 218