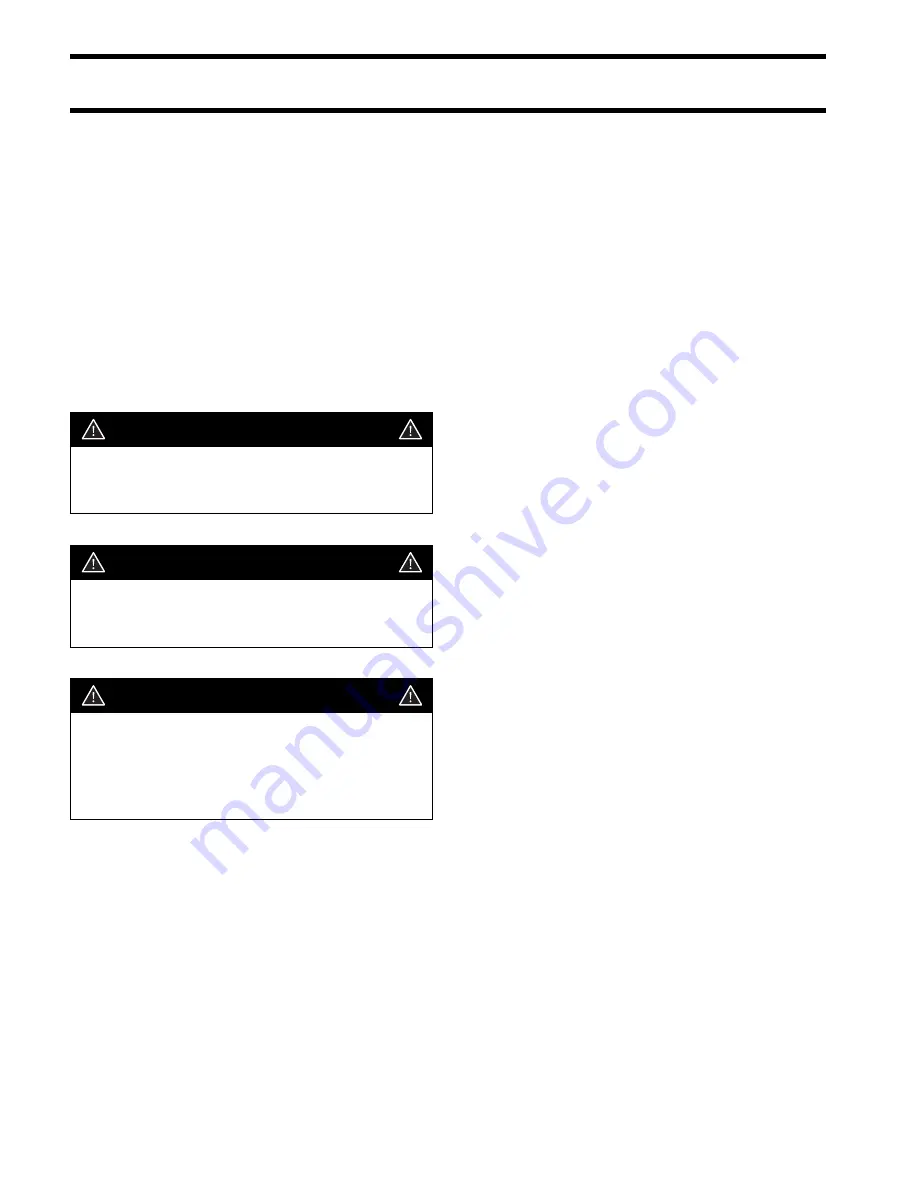
SAFETY INFORMATION
Before working on any part of the outboard, read the SAFETY section at the end of this manual.
This manual is written for qualified, factory-trained
technicians who are already familiar with the use
of
Evinrude
®
/Johnson
®
Special Tools. This man-
ual is not a substitute for work experience. It is an
organized guide for reference, repair, and mainte-
nance of the outboard(s).
This manual uses the following signal words iden-
tifying important safety messages.
IMPORTANT:
Identifies information that will help
prevent damage to machinery and appears next
to information that controls correct assembly and
operation of the product.
These safety alert signal words mean:
ATTENTION!
BECOME ALERT!
YOUR SAFETY IS INVOLVED!
Always follow common shop safety practices. If
you have not had training related to common shop
safety practices, you should do so to protect your-
self, as well as the people around you.
It is understood that this manual may be trans-
lated into other languages. In the event of any dis-
crepancy, the English version shall prevail.
To reduce the risk of personal injury, safety warn-
ings are provided at appropriate times throughout
the manual.
DO NOT make any repairs until you have read the
instructions and checked the pictures relating to
the repairs.
Be careful, and never rush or guess a service pro-
cedure. Human error is caused by many factors:
carelessness, fatigue, overload, preoccupation,
unfamiliarity with the product, and drugs and alco-
hol use, to name a few. Damage to a boat and
outboard can be fixed in a short period of time, but
injury or death has a lasting effect.
When replacement parts are required, use
Evinrude/Johnson Genuine Parts
or parts with
equivalent characteristics, including type, strength
and material. Using substandard parts could result
in injury or product malfunction.
Torque wrench tightening specifications must be
strictly followed. Replace any locking fastener
(locknut or patch screw) if its locking feature
becomes weak. Definite resistance to turning
must be felt when reusing a locking fastener. If
replacement is specified or required because the
locking fastener has become weak, use only
authorized
Evinrude/Johnson Genuine Parts.
If you use procedures or service tools that are not
recommended in this manual, YOU ALONE must
decide if your actions might injure people or dam-
age the outboard.
DANGER
Indicates an imminently hazardous situa-
tion which, if not avoided, WILL result in
death or serious injury.
WARNING
Indicates a potentially hazardous situation
which, if not avoided, CAN result in severe
injury or death.
CAUTION
Indicates a potentially hazardous situation
which, if not avoided, MAY result in minor
or moderate personal injury or property
damage. It also may be used to alert
against unsafe practices.
Summary of Contents for J10RLSUR
Page 1: ......
Page 2: ......
Page 147: ...POWERHEAD POWERHEAD VIEWS 145 7 POWERHEAD VIEWS Port Starboard View Manual Start DP0019 DP0020...
Page 148: ...146 POWERHEAD POWERHEAD VIEWS Rear View Manual Start DP0021...
Page 194: ...S 2...
Page 223: ...DR4698 Water Flow Diagram 9 9 15HP...
Page 228: ...A B C D E B C D E A 9 9 15HP DRC 6217 2 1...
Page 229: ......