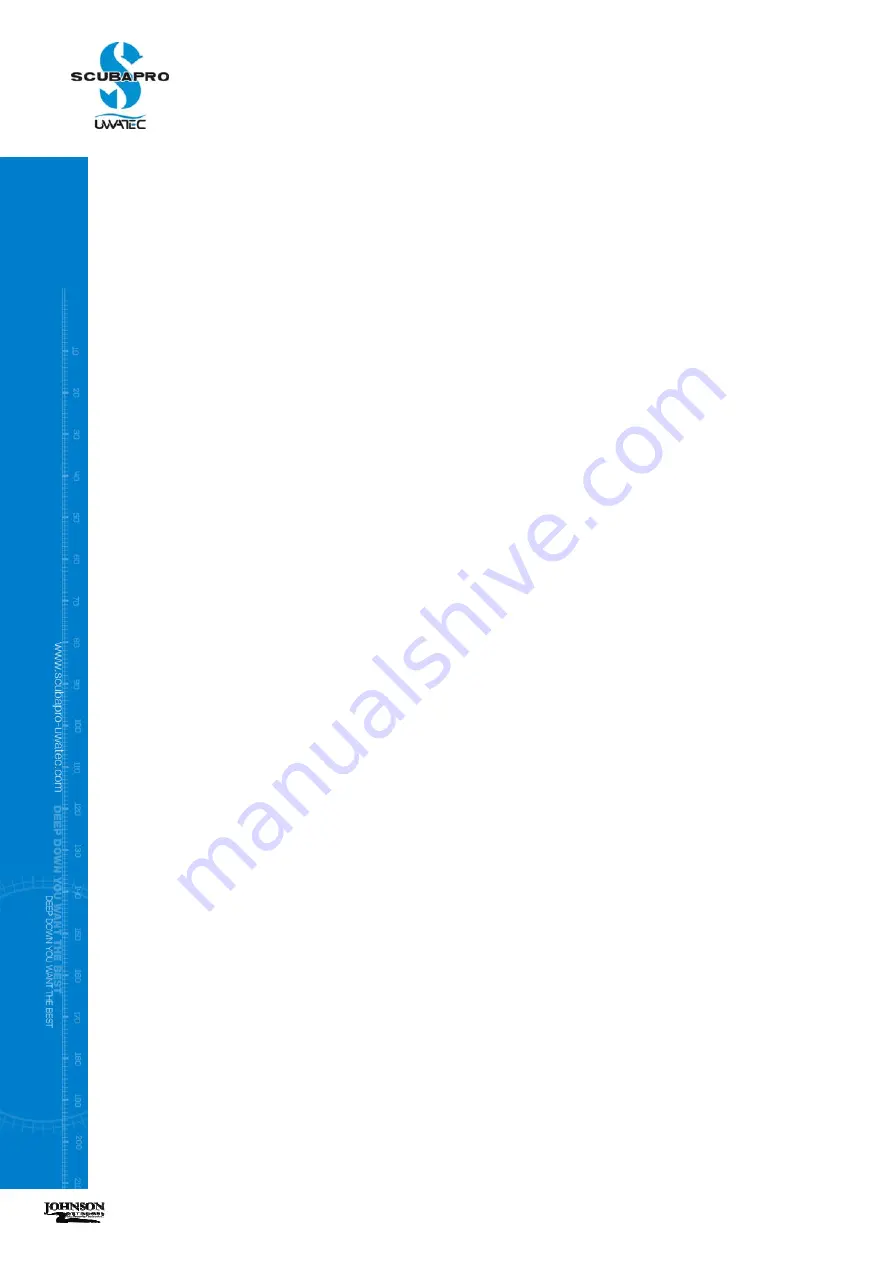
A 700 Maintenance Procedure
- 5 -
14. Assemble the shaft and sleeve assembly inside the Dive Switch. Put the o
ring P/N 01.050.126 on the stainless steel screw and fix the adjustment
knob using the 4mm Allen key.
15. Now insert this complete assembly on the inlet tube to align the ‘’tail’’ of the
Dive Switch in the grove of the flow reducer.
Warning: Make sure that the injection hole is facing the mouthpiece
tube when engaging the ‘’tail’’ of the Dive Switch in the flow
reducer
grove. If it is not the case, back the complete
assembly and rotate the
flow reducer in the correct position.
16. It is now important to engage the 2 tabs of the Dive Switch in the 2
recesses of the inlet tube. Place the Dive Switch lever in front of the
rotation limiting grove. Pull with one finger the lever into the case and at the
same time rotate anticlockwise the adjustment knob. When the 2 tabs are
aligned with the 2 recesses, the Dive Switch will go in position.
17. Maintain the pull on the Dive Switch lever and insert the clip to lock the
system in the case. Make sure that the clip is completely inserted in the
grove.
18. Check the diaphragm, there should be neither punctures nor distortion after
cleaning. Please follow the standard cleaning procedure.
19. Position the diaphragm on the case making sure that it is not distorted.
20. Assemble the retaining ring and purge cover.
21. Align the locator of the ring in the recess of the case and press.
22. Put the 4 small o rings in their groves on the inside of the front cover. Place
this assembly on the purge cover and maintain a constant pressure to keep
all the parts together.
23. Tighten crosswise the 4 screws with the Torx screwdriver without excessive
torque.
24. Assemble the mouthpiece support and the mouthpiece and secure with the
mouthpiece clip.
25. Place the inter stage pressure o ring in the groove of the inter stage
pressure hose and slightly lubricate.
THE 2ND STAGE IS NOW READY FOR ADJUSTMENT
WARNING: DO NOT ATTEMPT TO ADJUST A 2ND STAGE IF THE
INTERSTAGE PRESSURE IS NOT CORRECTLT ADJUSTED.
1. Before connecting the adjustment tool to the 2nd stage, and without
pushing on the purge, slowly blow through the inlet tube to detect a leak.
This information will indicate if the orifice is in contact (no leak) or not (leak)
with the seat. If a leak is detected, screw the 2nd stage adjustment tool to
the 2nd stage and slowly screw the orifice about one or two turns to stop
any leak.