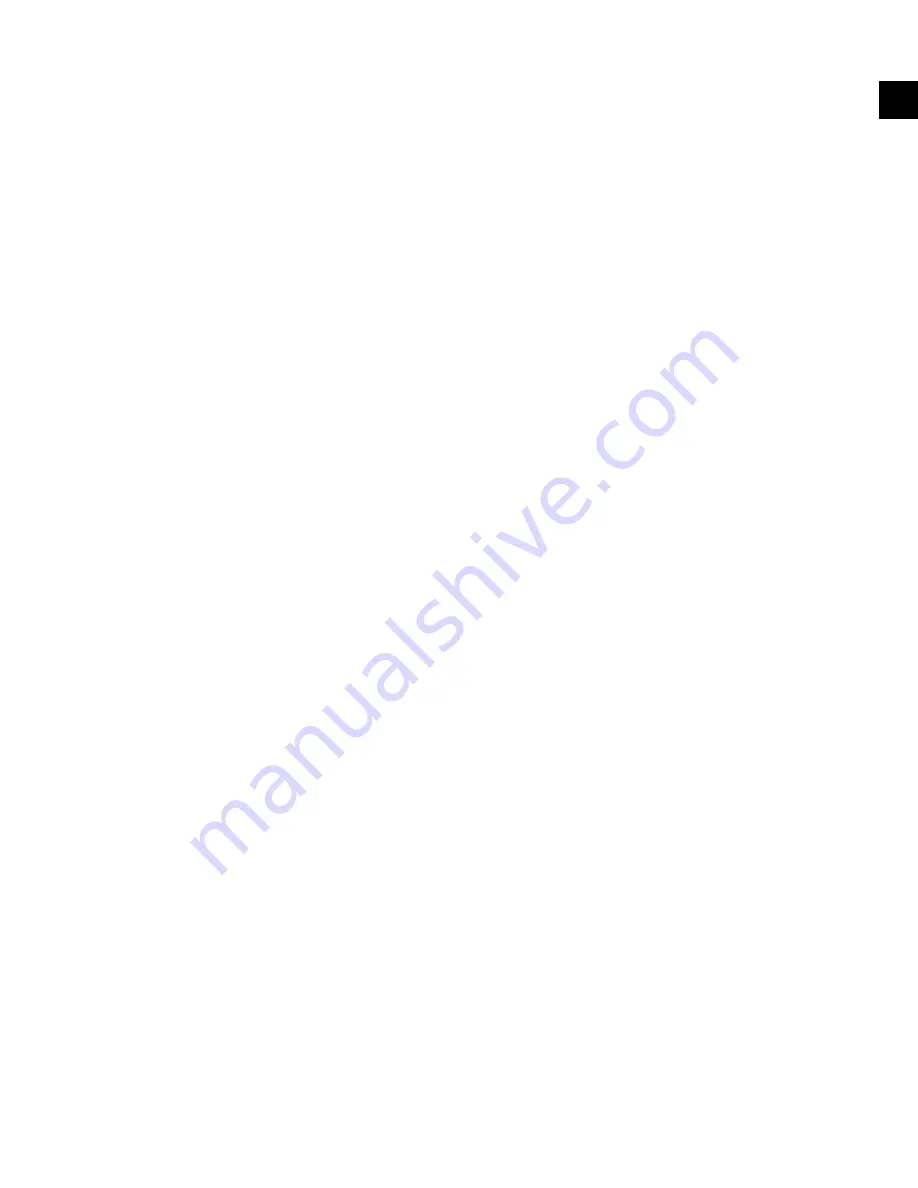
JOHNSON CONTROLS
7
FORM 160.69-N2
ISSUE DATE: 7/31/2015
1
GENERAL
This instruction describes the installation of a MOD-
EL YD Liquid Chilling Unit. This unit is shipped as
a single factory assembled, piped, wired package, re-
quiring a minimum of field labor to make chilled water
connections, condenser water connections, refrigerant
atmospheric relief connections, and electrical power
connections. (Refrigerant and oil charges shipped sep-
arately unless optional condenser isolation valves are
ordered.)
Chillers can also be shipped dismantled when required
by rigging conditions, but generally it is more econom-
ical to enlarge access openings to accommodate the
factory assembled unit. Chillers shipped dismantled
MUST be field assembled under the supervision of a
Johnson Controls representative, but otherwise instal-
lation will be as described in this instruction.
FIELD ASSEMBLED UNITS ONLY
Use Form 160.69-NM3 in conjunction with this instal-
lation instruction. This instruction will be furnished
with all units that are to be field assembled.
The services of a Johnson Controls representative will
be furnished to check the installation, supervise the
initial start-up and operation of all chillers installed
within Continental United States.
The Johnson Controls Warranty may be voided if
the following restrictions are not adhered to:
1. No valves or connections should be opened under
any circumstances because such action will result
in loss of the factory nitrogen charge.
2. Do not dismantle or open the chiller for any rea-
son except under the supervision of a Johnson
Controls representative.
3. When units are shipped dismantled, notify the
nearest Johnson Controls office in ample time for
a Johnson Controls representative to supervise
rigging the unit to its operating position and the
assembly of components.
4.
Do not make final power supply connections to
the compressor motors or control center.
5. Do not charge the compressors with oil.
6. Do not charge the unit with refrigerant.
7. Do not attempt to start the system.
8. Do not run hot water (110°F / 43°C max) or steam
through the evaporator or condenser at any time.
SHIPMENT
The chiller may be ordered and shipped in any of the
following forms:
Form 1 –
Factory Assembled Unit, complete with mo-
tor, refrigerant and oil charges.
1. The motor/compressor assembly mounted, with
all necessary interconnecting piping assembled.
OptiView™ Control Center is mounted on the
unit. Complete unit factory leak tested, evacuated
and charged with R-134A.
2. Miscellaneous material – Four (4) vibration
isolation pads (or optional spring isolators and
brackets).
Form 2 –
Factory Assembled Unit, complete with
motors (refrigerant and oil charges shipped separately).
1. The motor/compressor assemblies mounted, with
all necessary interconnecting piping assembled.
OptiView™ Control Center is mounted on the
unit. Complete unit factory leak tested, evacuated
and charged with holding charge of nitrogen.
2. Miscellaneous material – Four (4) vibration iso-
lation pads (or optional spring isolators and brack-
ets).
Form 3 –
Drivelines Separate From Shells – Shipped
as three major assemblies. Unit first factory assembled,
refrigerant piped, wired and leak tested; then disman-
tled for shipment. Compressor/motor assemblies re-
moved from shells and skidded. Evaporator/condenser
is not skidded.
All wiring integral with compressors are left on
them, and all conduit is left on shell. All openings on
compressors, oil separator, and shells are closed and
charged with dry nitrogen (2 to 3 PSIG) (14-21 kPa).
Miscellaneous packaging of control center, tubing,
water temperature controls, wiring, oil, isolators, solid
state starters (option), etc.; refrigerant charge shipped
separately.
SECTION 1 - INTRODUCTION