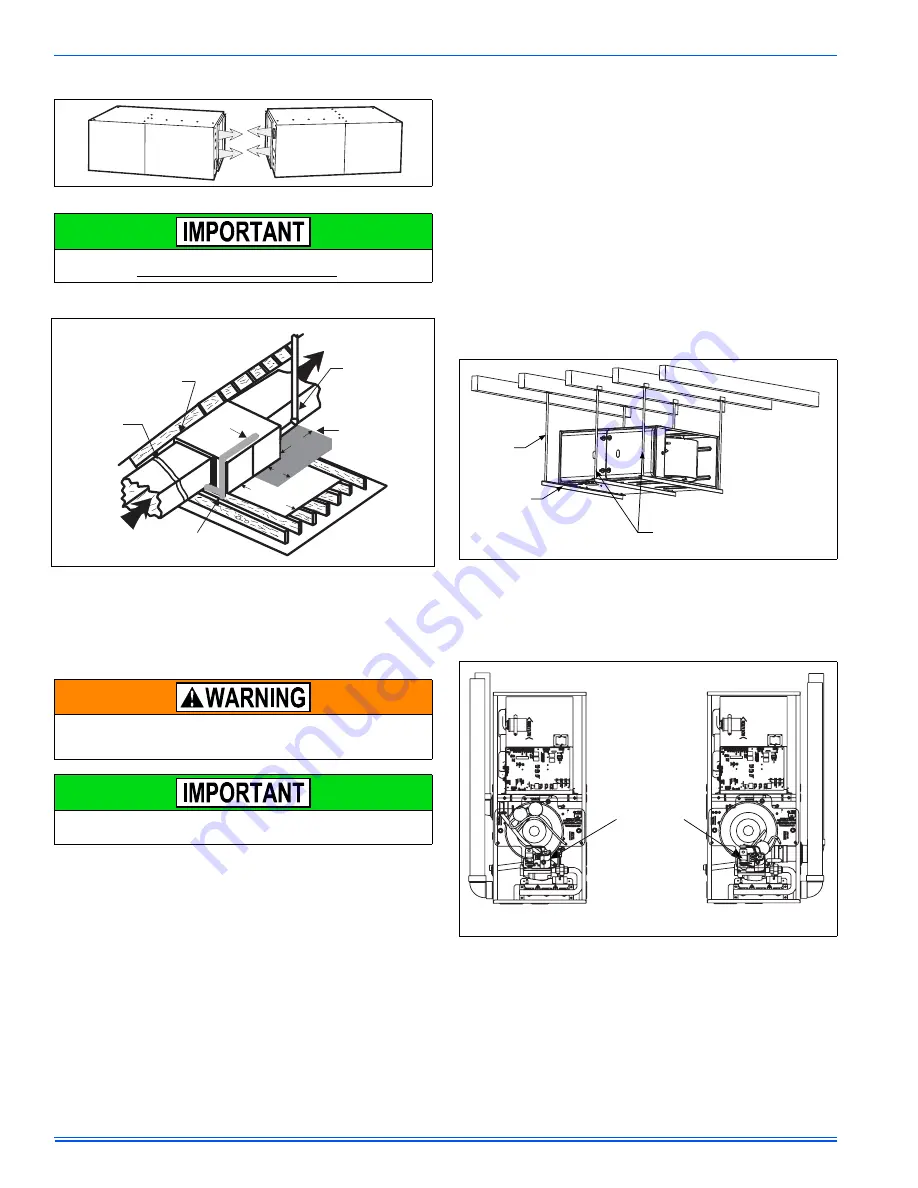
1083288-UIM-A-0114
8
Johnson Controls Unitary Products
HORIZONTAL APPLICATION
ATTIC INSTALLATION
This appliance is certified for line contact when the furnace is installed
in the horizontal left or right position. The line contact is only permissible
between lines that are formed by the intersection of the top and two
sides of the furnace and the building joists, studs or framing. This line
may be in contact with combustible material. Refer to Figure 10.
When moving or handling this furnace prior to installation, always leave
the doors on the furnace to provide support and to prevent damage or
warping of the cabinet. When lifting the furnace, support the ends of the
furnace rather than lifting by the cabinet flanges at the return air open-
ings (bottom or sides) or supply air opening.
It is acceptable to use the primary heat exchanger tubes as a lifting
point provided that the tubes are lifted at the front of the heat exchang-
ers where attached to the vestibule panel. Do not use the top return
bend of the heat exchangers as lifting points as the tubes may shift out
of position or their location brackets/baffles.
SUSPENDED FURNACE / CRAWL SPACE
INSTALLATION
The furnace can be hung from floor joists or installed on suitable blocks
or pads. Blocks or pad installations shall provide adequate height to
ensure that the unit will not be subject to water damage.
Units may also be suspended from rafters or floor joists using rods, pipe
angle supports or straps. In all cases, the furnace should be supported
with rods, straps, or angle supports at three locations to properly sup-
port the furnace. Place one support at the supply end of the furnace,
one support located approximately in the center of the furnace near the
blower shelf, and the third support should be at the return end of the fur-
nace. Maintain a 6” (15.2 cm) minimum clearance between the front of
the furnace and the support rods or straps.
All six suspension points must be level to ensure proper and quiet fur-
nace operation. When suspending the furnace, use a secure platform
constructed of plywood or other building materials secured to the floor
or ceiling joists. Refer to Figure 11 for details and additional information.
DOWNFLOW APPLICATION
To apply the furnace in a downflow position, it will be necessary to
rotate the vent blower 90° left or right so that the vent pipe passes
through the side of the furnace casing. See Figure 12.
FIGURE 9:
Horizontal Application
This furnace may be installed in a horizontal position on either side as
shown above.
It must not be installed on its back.
FIGURE 10:
Typical Attic Installation
When a furnace is installed in an attic or other insulated space, keep
all insulating materials at least 12î (30.5 cm) away from furnace and
burner combustion air openings.
During installation, doors should remain on the furnace when
moving or lifting.
Return
Air
Sediment
Trap
Gas Piping
Supply
Air
Vent (Maintain
required
clearances to
combustibles)
Line contact only permissible
between lines formed by the
intersection of furnace top
and two sides and building
joists, studs or framing
12”
30” MIN.
Work Area
Filter rack
must be a minimum
distance
of 18” (45.7 cm)
from the
furnace
12”
Sheet metal in
front of furnace
combustion air
Openings is
Recommended
FIGURE 11:
Typical Suspended Furnace / Crawl Space Installation
FIGURE 12:
Downflow Venting
Support
Rod
Support
Angle (x3)
Maintain 6” minimum
clearance between support
rods and front of furnace
LEFT SIDE VENT
RIGHT SIDE VENT
Rotate vent
blower 90°
either way