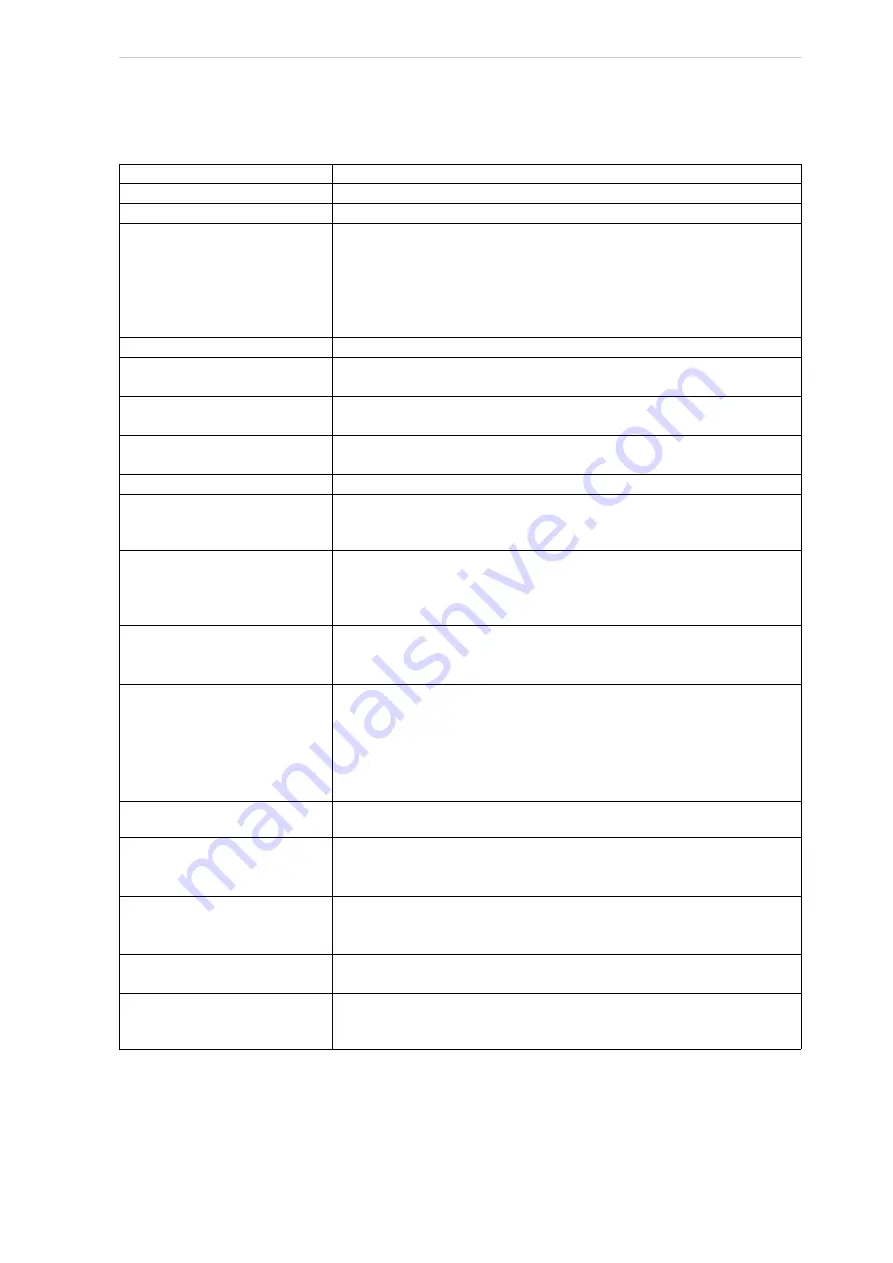
Engineering manual - SAB 193-233-283 S A-frame (including ATEX)
20/168
008831 en 2020.10
The unit name plate is positioned on the frame and contains this information:
Refrigeration unit No.
Identification no. (serial no.)
Year
Year of manufacturing.
Type
Manufacturer's type designation.
Scope
For EC PED/EAC approval: ‘Unit & Piping’ means that the CE/EAC
mark applies to the complete unit including the piping system.
’Piping’ means that the CE/EAC mark applies to the piping system
only, and it is the sole responsibility of the owner to ensure and
declare that the complete unit is in conformity with the provisions
of all relevant rules.
Design code
Design code used for the unit and piping system.
Approval no.
If the unit/manufacture has been approved by a 3rd party/notified
body.
Refrigerant - Fluid
Refrigerant of the unit.
Refrigerant designation according to ISO 817.
Refrigerant - Group
For EC PED approval:
Fluid group 1 or 2 according to the PED directive.
Supply voltage - Control
Supply voltage and frequency of the control system.
Refrigerant charge
Weight of the refrigerant charge on the unit.
This is only stated if the unit includes an evaporator and/or a
condenser.
Pressure system
The low-pressure side of the unit piping system is referred to as
the LP side.
The high-pressure side of the unit piping system is referred to as
the HP side.
Category
For EC PED approval:
The maximum category of the piping system (CAT 1, 2 or 3) or of
the assembly unit and piping (CAT 3 or 4).
Allowable pressure, max.
The max. pressure (pressure relative to atmospheric pressure)
that the unit/piping system has been designed for in terms of
pressure strength design.
The maximum practical operation pressure is lower than the maxi-
mum allowable pressure depending on the operating conditions
and safety equipment settings.
Test pressure
The test pressure that the unit/piping system has been strength
tested with.
Allowable temperature,
min./max.
The minimum and maximum temperatures that the unit/piping
system has been designed for at the indicated maximum allowable
pressures.
CE xxxx
The CE mark appears on the name plate for EC PED approval only.
The four digits make up the registration no. of the notified body/
3rd party in charge.
Ex
If the unit is designed in accordance with the EC ATEX directive,
there is an Ex mark on the name plate.
EAC
The EurAsian Conformity mark (EAC) indicates that the unit is in
compliance with all relevant technical regulations of the Eurasian
Customs Union.
Note: Main supply voltage
can be found on the motor and/or electrical panel name plate.
Summary of Contents for Sabroe SAB 193 L
Page 1: ...SAB 193 233 283 S A frame including ATEX Screw compressor units Engineering manual en ...
Page 2: ......
Page 169: ......