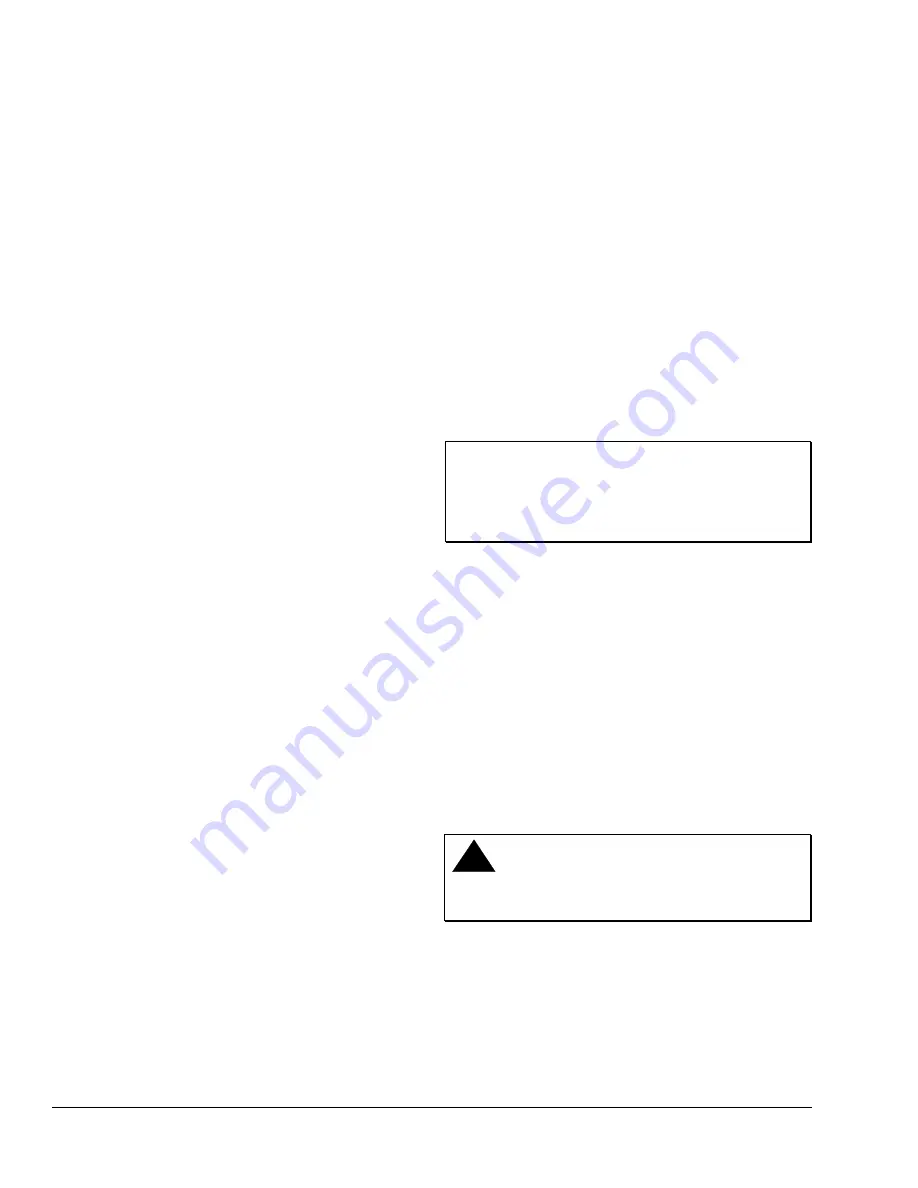
4 RLD-H10G Product/Technical Bulletin
C
alibration and Verification
The leak vial may be used as often as necessary to
assure proper operation of the RLD-H10G, and to
assist in determining the size of the leak. When using
the small leak range position, a leak of HFC causing
an audible signal equal to that produced by the
leak vial has a leak rate of approximately
one-half ounce/year. When using the medium leak
range position on a CFC or HCFC system, this leak
rate would also be approximately one-half ounce/year.
Proper unit response during the calibration test verifies
sensitivity and operation for all three test positions.
1.
Ensure that the range switch is in the small (“SM”)
position and idling at three or four beats per
second. (See Figure 8.)
2.
Remove the black, sticky-label disc from the cap of
the leak vial and discard. Allow a few minutes for
the leak rate to stabilize. Do not attempt to
unscrew the cap, as you may damage the bottle.
The vial contains enough refrigerant to last for
approximately six months.
3.
Test operation by briefly moving the probe tip over
the opening of the leak vial as if you are trying to
locate this leak. It is not necessary to hold the
probe over the leak, as this does not simulate field
conditions.
The RLD-H10G should respond with an increase
in flash rate and sound, verifying operation and
indicating the location of the leak.
4.
If the RLD-H10G does not respond to the leak vial,
make sure there is liquid in the bottle. If the unit
still does not respond to the leak, increase the
sensor heat slightly by turning the sensor heat
control knob (on the bottom of the unit) 1/16th of
a turn clockwise.
5.
Allow a minute for the sensor to heat, then repeat
the calibration procedure.
T
ips for Finding Leaks
•
Use the black rubber probe tip whenever possible
and hold the probe approximately 1/4 in. above the
area being tested. Move the probe tip at about
two inches per second along seams or joints
suspected of leaking.
•
Start leak checking anywhere, and continue in a
logical progression through the entire system to
locate all leaks.
•
Set the range switch to the appropriate range to
ensure maximum sensor life. If the leak size is
unknown, start at the large (“LG”) leak setting.
Adjust the balance control to maintain slow ticking
(three or four ticks per second) in the idle state.
(See Figure 8.)
IMPORTANT: Exposing the sensor to large
amounts of refrigerant or holding the
probe over a leak for a long period of
time will significantly shorten sensor
life.
•
On CFC and HCFC systems, the medium (“MED”)
range is sufficient to verify that the system is free
of leaks that require fixing.
•
On HFC systems, use the small (“SM”) range to
verify that the system is free of leaks that require
fixing.
•
Replace the filter often (as described in the
Maintenance
section) to retain airflow and
sensitivity.
•
Wipe all surfaces to be tested with a clean, dry
cloth.
•
Check ports for moisture before inserting the
probe.
!
CAUTION: Equipment Damage Hazard.
Submerging the probe in liquid
will damage the vacuum pump.