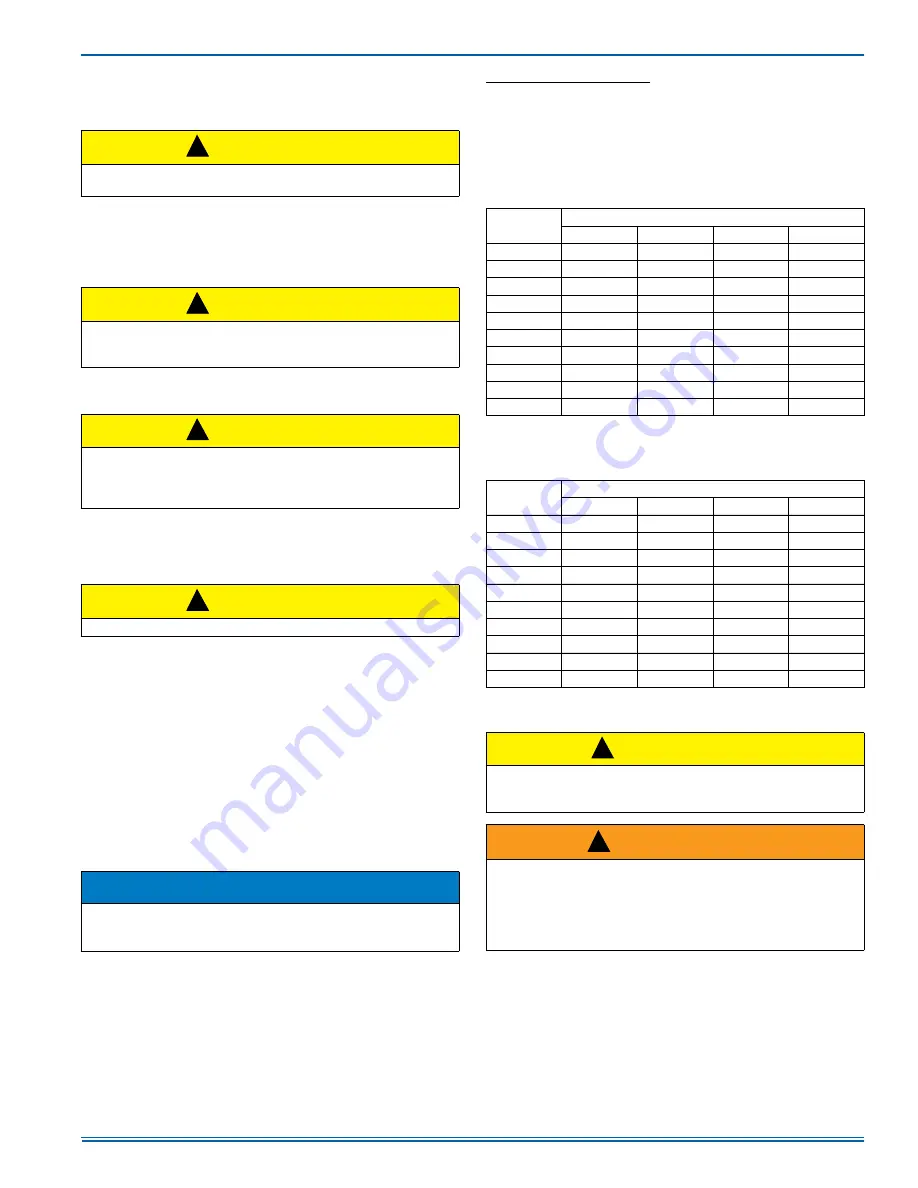
5750156-UIM-B-0919
Johnson Controls Ducted Systems
9
COMPRESSORS
The compressor used in this product is specifically designed to operate
with R-410A refrigerant and cannot be interchanged.
The compressor uses polyolester oil (POE oil), Mobile 3MA POE. This
oil is extremely hydroscopic, meaning it absorbs water readily. POE oil
can absorb 15 times as much water as other oils designed for HCFC
and CFC refrigerants. If refrigerant circuit is opened, take all necessary
precautions to avoid exposure of the oil to the atmosphere.
POE (polyolester) compressor lubricants are known to cause long term
damage to some synthetic roofing materials.
Procedures which risk oil leakage include, but are not limited to, com-
pressor replacement, repairing refrigerant leaks, and replacing refriger-
ant components such as filter drier, pressure switch, metering device, or
coil.
Units are shipped with compressor mountings, which are factory-
adjusted and ready for operation.
GAS HEAT
These single stage gas-fired heat sections have direct spark ignition.
GAS PIPING
Proper sizing of gas piping depends on the cubic feet per hour of gas
flow required, specific gravity of the gas, and the length of run. National
Fuel Gas Code Z223.1 or CSA B149.1 must be followed in all cases
unless superseded by local codes or gas company requirements. See
Tables 8 and 9.
The BTU content of the gas may differ with locality. Check the value
with the local gas utility.
GAS CONNECTION
The gas supply line must be routed through the 1-5/8 in. hole located on
the right side of the unit. See Figure 3 for the location. The unit is sup-
plied with a rubber grommet that fits in this hole and is used to seal
around the gas pipe. THIS GROMMET MUST BE INSTALLED TO
PREVENT LEAKAGE OF AIR AND WATER INTO THE HEATING/
CONTROLS COMPARTMENT.
Gas piping requirements:
• A drip leg and a ground joint union must be installed in the gas pip-
ing.
• When required by local codes, a manual shut-off valve may have
to be installed outside of the unit.
• Use wrought iron or steel pipe for all gas lines. Apply pipe thread
sealant sparingly to male threads only.
• All piping must be cleaned of dirt and scale by hammering on the
outside of the pipe and blowing out the loose dirt and scale. Before
initial start-up, ensure that all of the gas lines external to the unit
have been purged of air.
• The gas supply must be a separate line and installed in accor-
dance with all applicable safety codes. After the gas connections
have been completed, open the main shut-off valve admitting nor-
mal gas pressure to the gas valve. Check all joints for leaks with
soap solution or other material suitable for the purpose. NEVER
USE AN OPEN FLAME.
CAUTION
This system uses R-410A Refrigerant which operates at higher pres-
sures than R-22. No other refrigerant may be used in this system.
CAUTION
Do not leave the system open to the atmosphere. Unit damage could
occur due to moisture being absorbed by the POE oil in the system.
This type of oil is highly susceptible to moisture absorption.
CAUTION
Exposure to compressor oil, even if immediately cleaned up, may
cause embrittlement (leading to cracking) to occur in one year or
more. When performing any service that may risk exposure of com-
pressor oil to the roof, take precautions to protect roofing.
CAUTION
Do not loosen compressor mounting bolts.
NOTICE
There may be a local gas utility requirement specifying a minimum
diameter for gas piping. All units require a 1/2 in. pipe connection at
the gas valve.
!
!
!
!
Table 8:
Natural Gas Pipe Sizing Chart
1
1. Maximum capacity of pipe in cubic feet of gas per hour (based upon a pres-
sure drop of 0.3 in. W.C. and 0.6 specific gravity gas).
Length
(ft)
Nominal Inches Iron Pipe Size
1/2 in.
3/4 in.
1 in.
1-1/4 in.
10
132
278
520
1,050
20
92
190
350
730
30
73
152
285
590
40
63
130
245
500
50
56
115
215
440
60
50
105
195
400
70
46
96
180
370
80
43
90
170
350
90
40
84
160
320
100
38
79
150
305
Table 9:
Propane (LP) Gas Pipe Sizing Chart
1
1. Maximum capacity of pipe in thousands of BTU per hour (based upon a
pressure drop of 0.5 in. W.C.).
Length
(ft)
Nominal Inches Iron Pipe Size
1/2 in.
3/4 in.
1 in.
1-1/4 in.
10
275
567
1071
2,205
20
189
393
732
1496
30
152
315
590
1212
40
129
267
504
1039
50
114
237
448
913
60
103
217
409
834
70
96
196
378
771
80
89
185
346
724
90
83
173
322
677
100
78
162
307
630
CAUTION
If flexible stainless steel tubing is allowed by the authority having
jurisdiction, wrought iron or steel pipe must be installed at the gas
valve and extend a minimum of two (2) in. outside of the unit casing.
WARNING
Natural gas may contain some propane. Propane being an excellent
solvent, will quickly dissolve white lead or most standard commercial
compounds. Therefore, a special pipe thread sealant must be
applied when wrought iron or steel pipe is used. Shellac base com-
pounds such as gaskoloc or stalastic, and compounds such as Rec-
torseal # 5, Clyde’s or John Crane may be used.
!
!