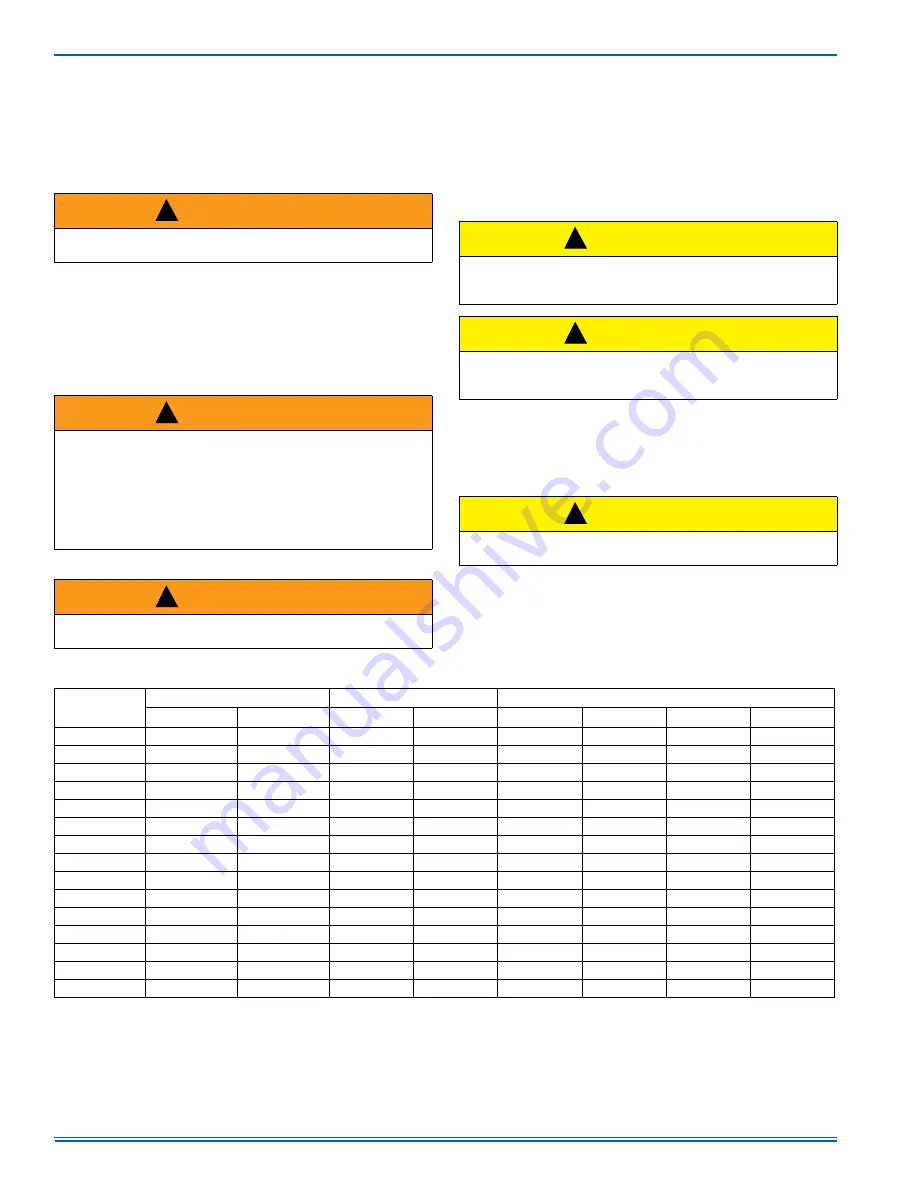
5750156-UIM-B-0919
4
Johnson Controls Ducted Systems
LOCATION
Use the following guidelines to select a suitable location for these units:
• Unit is designed for
outdoor installation
only.
• Outdoor coils must have an unlimited supply of air. Where a choice
of location is possible, position the unit on either north or east side
of building.
• Suitable for mounting on roof curb.
• For ground level installation, use a level pad or slab. The thickness
and size of the pad or slab used must meet local codes and unit
weight. Do not tie the slab to the building foundation.
• Roof structures must be able to support the weight of the unit and
its options/accessories. Unit must be installed on a solid, level roof
curb or appropriate angle iron frame.
• Maintain level tolerance to 1/8 in. across the entire width and
length of unit.
CLEARANCES
All units require particular clearances for proper operation and service.
Installer must make provisions for adequate combustion and ventilation
air in accordance with section 5.3 of Air for Combustion and Ventilation
of the National Fuel Gas Code, ANSI Z223.1 – Latest Edition (in
U.S.A.), or Sections 7.2, 7.3, or 7.4 of Gas Installation Codes, CSA-
B149.1 (in Canada) - Latest Edition, and/or applicable provisions of the
local building codes. See Table 5 for clearances required for combusti-
ble construction, servicing, and proper unit operation.
RIGGING AND HANDLING
Exercise care when moving the unit. Do not remove any packaging until
the unit is near the place of installation. Rig the unit by attaching chain
or cable slings to the lifting holes provided in the base rails. Spreader
bars whose length exceeds the largest dimension across the unit
MUST
be used across the top of the unit.
Units can be moved or lifted with a forklift. Slotted openings in the base
rails are provided for this purpose.
WARNING
Do not attach supply and return duct work to the bottom of the unit
base pan as the drain pan could be compromised.
WARNING
Excessive exposure of this unit to contaminated combustion air may
result in equipment damage or personal injury. Typical contaminates
include: permanent wave solution, chlorinated waxes and cleaners,
chlorine based swimming pool chemicals, water softening chemicals,
carbon tetrachloride, Halogen type refrigerants, cleaning solvents
(e.g. perchloroethylene), printing inks, paint removers, varnishes,
hydrochloric acid, cements and glues, anti-static fabric softeners for
clothes dryers, masonry acid washing materials.
WARNING
Do not permit overhanging structures or shrubs to obstruct con-
denser air discharge outlet, combustion air inlet or vent outlets.
!
!
!
CAUTION
All panels must be secured in place when the unit is lifted.
The outdoor coils should be protected from rigging cable damage
with plywood or other suitable material.
CAUTION
If a unit is to be installed on a roof curb other than a Unitary Products
roof curb, gasket or sealant must be applied to all surfaces that come
in contact with the unit underside.
CAUTION
Before lifting, make sure the unit weight is distributed equally on the
rigging cables so it will lift evenly.
!
!
!
Table 3:
Weights and Dimensions
Model
Weight (lb)
Center of Gravity
4 Point Load Location (lb)
Shipping
Operating
X
Y
A
B
C
D
PCG4A24050
346
341
28
15
120
95
81
71
PCG4A24075
356
351
28
15
124
96
81
76
PCG4A30050
391
386
28
15
139
99
90
84
PCG4A30075
395
390
28
15
146
93
82
95
PCG4A36050
399
394
28
15
141
107
94
78
PCG4A36075
406
401
28
15
135
115
103
74
PCG4A36100
410
405
28
15
139
113
99
80
PCG4A42075
446
441
28
15
145
112
99
85
PCG4A42100
448
443
28
15
148
110
96
89
PCG4B48065
465
460
28
15
189
116
93
117
PCG4B48100
473
468
28
15
169
139
115
100
PCG4B48125
478
473
28
15
164
145
124
95
PCG4B60065
482
477
29
15
174
142
124
92
PCG4B60100
486
481
28
15
177
140
117
102
PCG4B60125
493
488
27
15
151
167
141
84