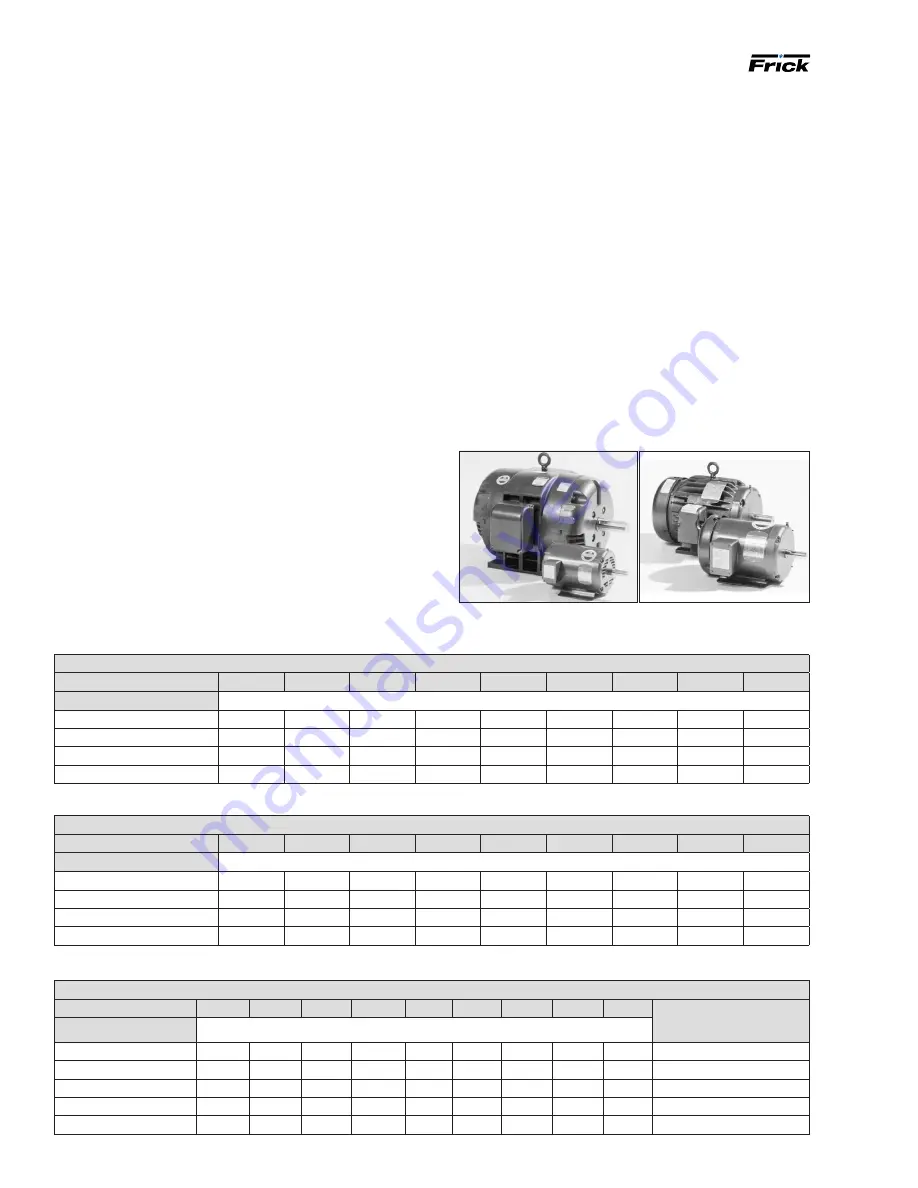
210.100-IOM (JUL 2021)
Page 44
AcuAir Hygienic Air Units
Maintenance
Table 8: Fan bearing lubrication intervals - ball bearing pillow blocks
Relubrication schedule (months)
Speed (rpm)
500
1000
1500
2000
2500
3000
3500
4000
4500
Shaft diameter (in.)
1/2 to 1 11/16
6
6
5
3
3
2
2
2
1
1 15/16 to 2 7/16
6
5
4
2
2
1
1
1
1
2 11/16 to 2 15/16
5
4
3
2
1
1
1
-
-
3 7/16 to 3 15/16
4
3
2
1
1
1
-
-
-
Table 9: Fan bearing lubrication intervals - spherical roller bearing
solid pillow blocks
Relubrication schedule (months)
Speed (rpm)
500
1000
1500
2000
2500
3000
3500
4000
4500
Shaft diameter (in.)
1 3/16 to 1 7/16
6
4
4
2
1
1
1
1
1/2
1 11/16 to 2 3/16
4
2
1 1/2
1
1/2
1/2
1/2
1/2
1/2
2 7/16 to 3 7/16
3
1 1/2
1
1/2
1/2
1/2
1/2
-
-
3 15/16 to 4 15/16
2 1/2
1
1/2
1/4
-
-
-
-
-
Table 10: Fan bearing lubrication intervals - spherical roller bearing-split pillow blocks
Relubrication schedule (months)
Speed (rpm)
500
750
1000
1500
2000
2500
3000
3500
4000
Grease to be added at
each interval (oz)
Shaft diameter (in.)
1 7/16 to 1 15/16
6
4 1/2
4
4
3 1/2
2 1/2
2 1/2
1
1
0.50 oz
2 3/16 to 2 11/16
5
4 1/2
4
2 1/2
2 1/2
1 1/2
1/2
1/4
1/4
0.75 oz
2 15/16 to 3 15/16
4 1/2
4
3 1/2
2 1/2
1 1/2
1
1/2
-
-
2.00 oz
4 7/16 to 4 15/16
4
4
2 1/2
1
1/2
-
-
-
-
4.00 oz
5 7/16 to 5 15/16
4
2 1/2
1 1/2
1
-
-
-
-
-
7.00 oz
3. Finally, rinse with plain water to completely remove all
traces of the powdery hydroxide and the cleaner.
4. Allow the cleaned surface to dry completely.
The drying process facilitates the formation of the passive
zinc-carbonate boundary layer that matures over time
with the naturally occurring rain and dry cycles.
Lubricating the fan bearing
Standard fan configurations ship with fan bearings factory
lubricated (ready for start-up). Turn off and lock out the
fan to prevent accidental start-up of the fan during lubri-
cation procedures. Also, secure sheaves before servicing
the unit to ensure that the fan cannot freewheel. Failure to
do so may result in severe personal injury.
Correct lubrication of bearings helps to assure maximum
bearing life. Generally, lubricate bearings every 1,000 hr
of operation or more frequently when exposed to wet
location, wide temperature variety or severe atmospheric
conditions.
Add grease with manual grease gun until a light bead of
grease appears at the bearing grease seal or see lubrica-
tion frequency in
and refer to TCF's
Direct Driven Fan/Motor guide. Observation of the condi-
tion of the grease expelled from the bearings at the time
of re-lubrication is the best guide as to whether to alter
the lubrication intervals and the amount of grease added.
Always lubricate bearings before extended shutdown or
storage and rotate shaft monthly.
Lubricant for fan bearings
A lithium/petroleum base grease conforming to an NLGI
Grade II consistency is normally used. Lubricant must be
free of any chemical impurities such as free acid or free
alkali, dust, rust, metal particles or abrasives. This light
viscosity, low torque grease is rust inhibited and water
resistant, has a temperature range of -30°F to +200°F
with intermittent highs of +250°F. Lubricate bearings as
required by the severity of required duty.
Correct interval and quantity
Fan segment-fan motor
Keep the motor clean, dry, and correctly lubricated at all
times. Blow dust and dirt out of windings periodically us-
ing low-pressure (50 psig) air. See the following figure
.
Figure 51: ODP (open drip proof) and TEFC (totally en-
closed fan cooled)
ODP
TEFC